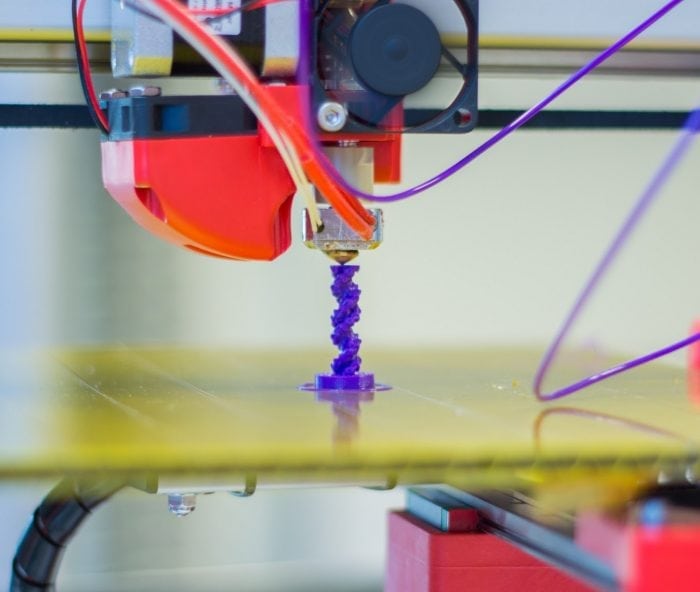
The vision to 3D-print fully functional devices that contain multiple materials in a press of a button has come a step closer to reality. Researchers from the University of Nottingham – UK have developed a method to 3D print structures that contain electrically-conductive silver inks and insulative polymeric inks in a single process. The key to this innovation is a new method to solidify metallic and polymeric inks rapidly using a single source of energy, a UV light.
The challenge of fabricating dissimilar materials is the various methods required to solidify each material. Silver inks contain nanoparticles of the metal dispersed in a solvent. To solidify the ink and form a layer of conductive silver high temperatures are required in order to evaporate the solvents and fuse the metal nanoparticles. Such high temperatures are destructive to most polymeric inks which limits the choice of printing conductive and non-conductive materials in a single structure.
Dr. Ehab Saleh and co-authors from the Centre for Additive Manufacturing (CfAM) at the University of Nottingham – UK found that silver nanoparticles in conductive inks are capable of absorbing UV light efficiently. The absorbed UV energy is converted into heat sufficient to evaporate the solvents of the conductive ink and fuse the silver nanoparticles but is localized to the conductive ink hence does not damage any adjacent printed polymers. The same compact and low-cost LED-based UV light was used to convert liquid polymeric inks (monomers) into solids in the same printing process to form 3D structures that contain multiple materials.
Professor Chris Tuck, Professor of Materials Engineering and lead investigator of the study, highlighted the potential of the breakthrough, ‘Being able to 3D print conductive and dielectric materials in a single structure with the high precision that inkjet printing offers, will enable the fabrication of fully customised electronic components. You don’t have to select standard values for capacitors when you design a circuit, you just set the value and the printer will produce the component for you.’
Professor Richard Hague, the Director of the Centre for Additive Manufacturing (CfAM), commented on the vision of multifunctional additive manufacturing (MFAM) “Printing fully functional devices that contain multiple materials in complex, 3D structures is now a reality. This breakthrough has significant potential to be the enabling manufacturing technique for 21st Century products and devices that will have the potential for significant impact on both industry and the public”.
This study, 3D Inkjet Printing of Electronics Using UV Conversion was recently published in the journal Advanced Materials Technologies.