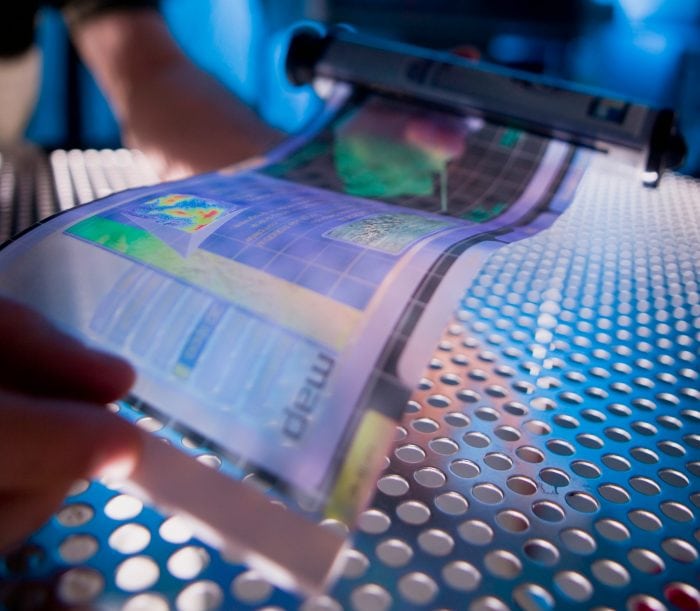
Plastics are polymers consisting of large molecules with long repeating chains of organic units. They offer the possibility of molecular design through chemical synthesis, good scalability, and low-cost potential, but their surface remains essentially inert, exhibiting very low electrical conductivity. This has marked them for many years in electronic applications as organic insulating materials.
There is, though, an emerging technology focused on the development of electronic devices incorporating plastics and opening prospects for flexible electronics that go beyond the Silicon Valley-popularized rigid silicon-based semiconductors. The growing attention on plastics as electronic materials grew in part because of their unique properties such as low density, good mechanical strength, flexibility, chemical resistance, and ease of processing.
The most used polymer substrates for flexible electronics are still, to this day, poly(ethyleneterephthalate) (PET), poly(ethylene naphthalate) (PEN), and polydimethylsiloxane (PDMS). The applications range from flexible solar cells to flexible piezoelectric devices, supercapacitors, electrodes, lithium batteries, LEDs, etc.
However, for a polymer to be used as an electronic device, its surface must become electrically conductive through metallization. Unfortunately, metallization of the polymer surface is not straightforward because the chemically inert polymer’s surface won’t bond to metals. This challenge is overcome with several surface activation methods such as physico-chemical, mechanical, and biological methods.
The science behind these surface activation methods is to provide the polymer’s surface with functional groups that bond well to metal ions and increase its superficial area. The downside to these methods is that they often rely on expensive (palladium salts) or hazardous chemicals (chromium compounds) and complex equipment (plasma reactors) and the resulting metal-polymer adhesion is, every so often, not satisfactory.
A research team at the Faculty of Engineering of the University of Porto (FEUP) recently developed a method to metalize a polymer surface by first “masking” it with another polymer displaying a strong affinity to the metal do deposit. This second polymer acts as a double-sided tape adhesive, one side being anchored to the base polymer and the other side with the potential to adhere to the metal film. The proof of concept was carried out with a thermoplastic polyurethane (TPU) by first immersing it in a solution of polyvinylpyrrolidone (PVP, the so-called double tape adhesive) in dimethyl sulfoxide (DMSO), creating an amide-rich network on the TPU surface that will further bond to silver during electroless silver plating.
The surface activation process developed by FEUP’s team takes advantage of the difference of solubility of TPU in DMSO and water. DMSO is a highly polar organic solvent that can dissolve both PVP and TPU and promote TPU chain extension, fostering the penetration of the PVP molecules into the TPU polymeric chain. When the TPU samples, that were swollen in a PVP: DMSO solution, are immersed in water (see Figure 1), their structure collapse giving rise to a TPU/PVP interpenetrating network. The water-soluble DMSO diffuses outside the polymer while PVP remains entangled in the TPU surface structure.
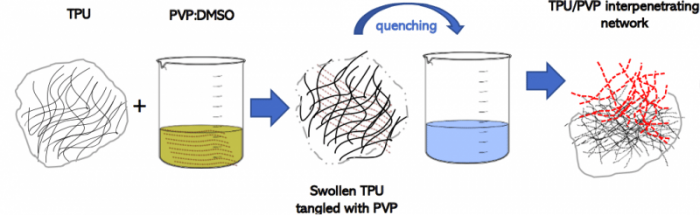
Figure 1. Schematic representation of the interpenetrating network method to activate the polymer’s surface. (Republished with permission from Applied Surface Science)
TPU’s surface becomes hydrophilic, and its contact angle (CA) decreases from 84.6º to 28º, mainly because of the PVP trapped at the surface. This lower CA translates into a higher surface energy, meaning that it is more prone to create bonds with other elements such as metals.
The metallization process is performed via electroless plating (ELP), a chemical, cost, and energy-saving process that has gathered attention due to its simplicity and efficacy in obtaining thin homogeneous coatings, particularly on complex shaped objects. ELP relies on the autocatalytic reaction of the metallic ions to deposit with a reducing agent occurring in an aqueous plating bath. Unlike electroplating, no external electrical power is needed, making the technique applicable to non-conductive materials.
The electroless silver plating process is performed in 2 steps: (i) development of “silver seeds” on the TPU surface to enable the growth of the silver film and (ii) development of a continuous silver film. When the PVP-functionalized TPU sample is in contact with a silver nitrate (AgNO3) solution, the lone pairs of oxygen and nitrogen from PVP amide’s group occupy the “sp” orbitals of Ag+ and a PVP:Ag+ complex is formed. Next, in this first step, a strong reducing agent, sodium borohydride (NaBH4), is added to form the surface silver aggregates, or “seeds,” that will further act as anchoring points for the development of a continuous film.
The second step takes place in a Tollens solution, widely known as the process to produce silver mirrors. In this case, glucose is used as a reductant, allowing a slow plating rate so that a uniform and continuous film is deposited as the Ag+ present in the solution is attracted to the previously NaBH4-reduced complex PVP(Ag). The result is a uniform and compact silver film adhered to the TPU’s PVP rich surface, with an average thickness of 12.5 µm, presented in Figure 2.
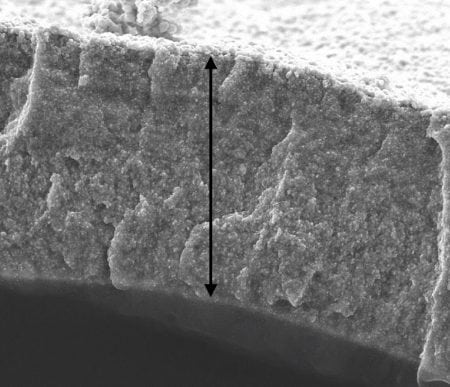
Figure 2. SEM micrograph of silver plated TPU surface. The coating is limited by the arrow. (Republished with permission from Applied Surface Science)
One of the main concerns when performing a metallization process in polymers is the adhesion between the film and the substrate’s surface. The surface activation process is intended to promote a strong substrate/film adhesion. To assess adhesion a simple test is performed using a tensile testing machine that peels off a double-sided adhesive tape, as seen in Figure 3. In the present case, the scotch tape tore before the film could be pulled out from the substrate, which means that the silver is well bonded to the surface, showing a peel strength higher than 8.5 N/cm.
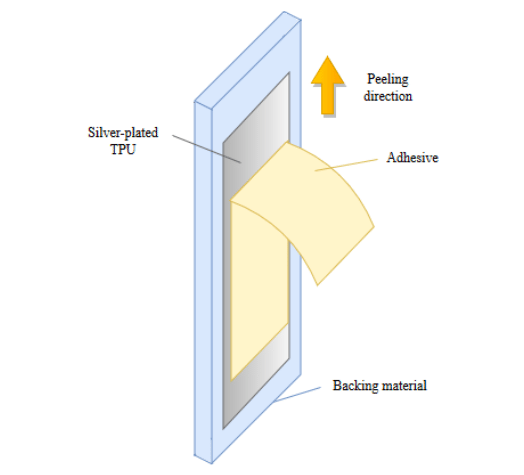
Figure 3. 180º T-peel test. One of the tensile machine claws grips the backing material with the TPU sample while the other grips the adhesive tape during displacement. (Republished with permission from Applied Surface Science)
An obvious trait for a flexible conductive substrate is its ability to bend while keeping its conductivity. In other words, it is important that the metallic film remains intact and conductive while being compressed, stretched, or twisted. By cyclically conforming/straightening the silver plated TPU sample around cylinders of different radii, the samples were subjected to compressive or stretching efforts, in the same way as pictured in Figure 4 (left). In the most demanding situation, 150 cycles for a 5 mm diameter cylinder, the resistance increased from 0.9 to 3.2 Ω, and, most importantly, the sample returned to its original shape and resistance after some minutes. For stretching alone, with FEUP’s team method, it is also possible to obtain a conductive TPU that withstands a deformation of 400% before conductivity failure, Figure 4 (right).
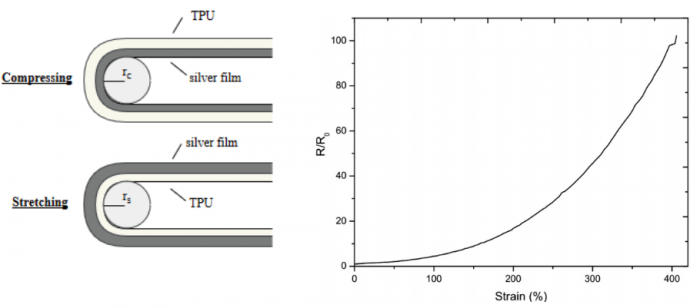
Figure 4. Left: bending tests performed in cylinders with radii of 15, 10 and 5 mm. Right: normalized resistance (R0 = 1.7 Ω) of silver plated TPU samples during tensile test. (Republished with permission from Applied Surface Science)
All in all, given the strong affinity of many metals to PVP, this activation technique, prior to metallization, has the potential to be applied to the plating of other metals and other polymer substrates, provided that the chosen solvent dissolves the PVP and swells the polymer without dissolving or degrading it.
These results are described in the article entitled Mechanically robust silver coatings prepared by electroless plating on thermoplastic polyurethane, recently published in the journal Applied Surface Science. This work was conducted by B. Vasconcelos, K. Vediappan, J.C. Oliveira, and C. Fonseca from the University of Porto and the University of Coimbra.