
Throughout history, humans have sought to find or design materials with desirable properties for different applications. Since each material has its advantages and disadvantages, oftentimes we want to try and combine them to get the “best of both worlds.” However, the way in which the materials are combined has a significant impact on the resulting material properties.
A great example of this can be seen by comparing the properties of metals and rubbers. Metals (e.g. steel) require a lot of energy to deform and break, however, they cannot stretch or elongate to long lengths and instead fracture brittlely. Rubbers (e.g. a rubber band) can stretch to many times their original length before breaking, however, they lack the high strength of the metal. By selecting the appropriate geometry (in this case, a core of metal surrounded by an elastic shell), we have been able to develop fibers that combine the strength of metal with the elasticity of rubber!
The fibers can elongate many times their original length but are also very tough (i.e. harder to deform). This toughness arises from the fact that the metal core breaks over and over while the polymer shell maintains the overall integrity of the fiber.
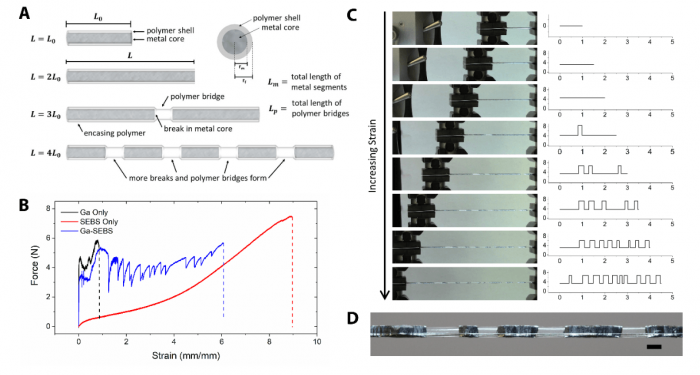
A) A schematic of how the fiber dissipates energy during stretching. B) The fibers combine the best attributes of metal (black line) and polymer (red line) to show significantly improved mechanical properties (blue line). C) Images of the fiber as it is stretched and the metal cores breaks repeatedly. D) Fiber stretched to eight times its original length. Figure republished with permission from Science Advances from doi.org/10.1126/sciadv.aat4600
Why would we want to create tough, stretchable fibers? The most promising application is for more effective energy dissipation in devices. In general, effective energy dissipation by one material protects other more fragile materials. Consider, for example, the human body, which is composed of an endoskeleton of bone surrounded by a soft matrix of tissue. Many of us have suffered an injury such as a fall in which we broke a bone. Luckily for us, the bone served to dissipate most of the energy from the impact of the fall and thus protected more fragile body parts such as organs from harm. The same energy-dissipating design is being applied in the metal-polymer core-shell fibers. By sacrificially breaking the metal core, the fiber dissipates energy from large loads. Thus, the fibers are useful for a range of potential applications, especially those in which a fiber geometry is particularly desirable. Think wearable electronics, next-generation textiles, soft robotics, and advanced packaging.
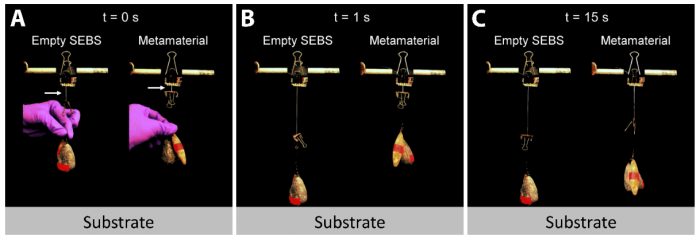
The fibers are able to hold much heavier loads without elongating rapidly (due to their toughness), allowing them to gently lower the weight down. Figure republished with permission from Science Advances from doi.org/10.1126/sciadv.aat4600
The fiber’s metal core is also electrically conductive until the first break. Additionally, increasing the temperature to just above room temperature (when the metal core will melt to a liquid) allows the fiber to quickly and reversibly alternate between soft and rigid mechanical properties and also allows the fiber to repair itself after damage. The fibers could be used in soft robotics by mimicking other examples of effective energy dissipation in the human body, which include collagen fibers that dissipate energy and prevent cuts from spreading in human skin, and titin that does the same for human muscle. The fibers are over twice as tough as titin!
And while we specifically used a metal core and a polymer shell, the fibers could in principle be extended to a range of core-shell materials, thus allowing the mechanism to be highly tunable depending on the optimal strength or operational conditions.
These findings are described in the article entitled Toughening stretchable fibers via serial fracturing of a metallic core, recently published in the journal Science Advances.