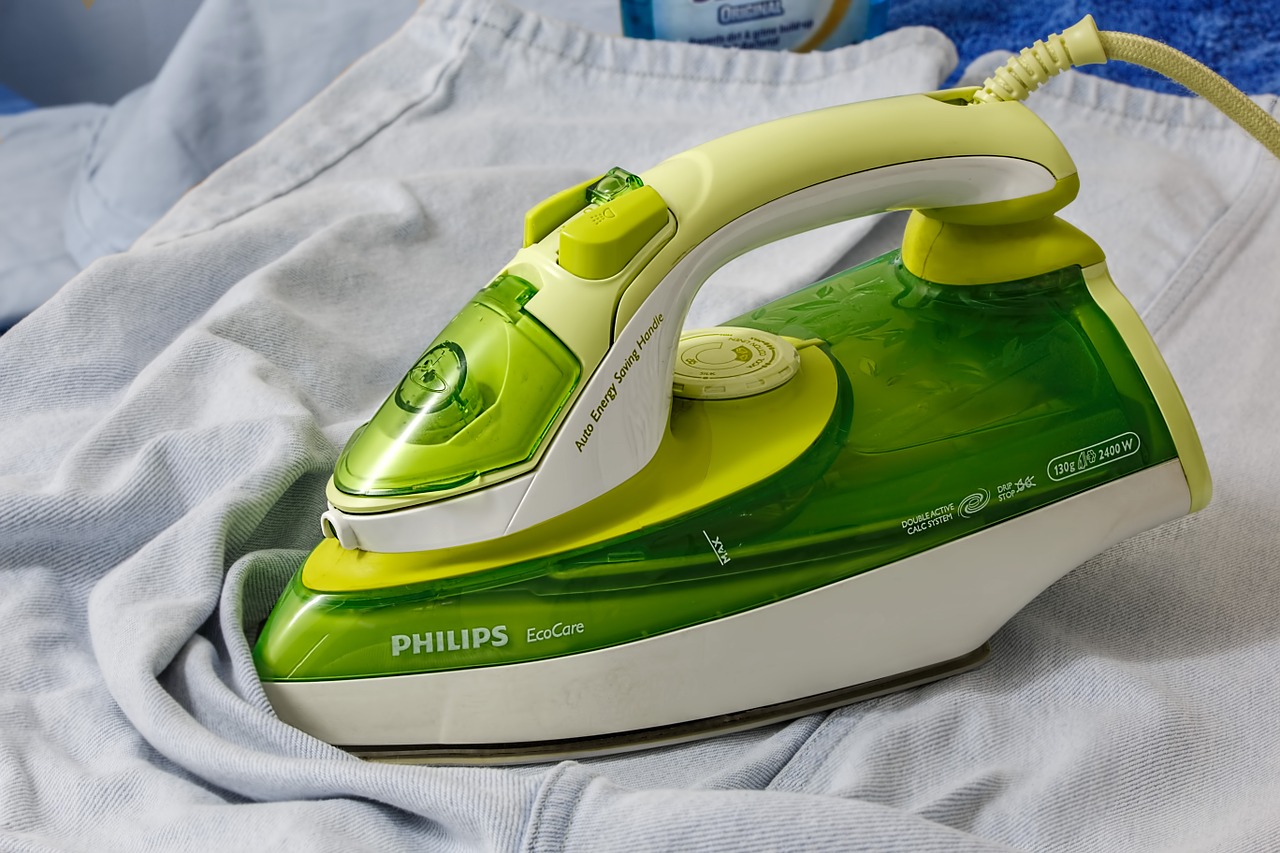
Various objects have been used for thousands of years to remove wrinkles. Metal pans filled with hot coals were used for smoothing fabrics in China in the 1st century BC. The early electric irons had no easy way of controlling their temperature, and the first thermostatically controlled electric iron appeared in the 1920s.
Later, steam was utilized for ironing clothes. Today steam irons are used in almost every home for removing wrinkles from clothes. However, when the water in an iron evaporates, calcite tends to form a layer of limescale on various surfaces, such as in the steam generating chambers and on the surfaces of the steam passageways. This leads to inefficiencies in ironing performance.
Ultrasonic vibrations, high-frequency sound waves beyond the range of human hearing, are being used in many existing technologies. For example, they are used for drying foods, cleaning objects such as teeth by dentists and water filtration. Recently, Associate Professor Hasan Koruk from MEF University, Mr. Muzaffer Serenli from Silter Company and Professor Kenan Y. Sanlıturk from Istanbul Technical University reported works on the use of ultrasonic vibration in steam irons to eliminate the accumulation of limescale.
The study was published in Applied Acoustics. They built a preliminary prototype of ultrasonic iron and conducted experiments to verify the expectation that ultrasonic vibrations are indeed beneficial in reducing the accumulation of limescale. Physical experiments were carried out using two steam irons, one with and one without an ultrasonic exciter. The duration of the experiments was a total of ten hours a day over a four-week period. During these experiments, the ultrasonic exciter was set at around 35 kHz. It was seen that there was significantly less limescale on the surfaces of the iron which were exposed to ultrasonic vibrations (approximately 32% less).
It is worth stating that the main purpose here is to prevent the accumulation of limescale at various locations of irons, including the steam generating chamber where water droplets evaporate and turn into steam, on the surfaces of steam passageways, and in the rear chamber. Examination of the predicted mode shapes of the preliminary design indicated that this design needed to be improved in order to create effective ultrasonic vibrations at the desired locations of the iron because the mode shapes at ultrasonic frequencies mostly comprised local modes due to local flexibilities in the iron structure (Figure 1).
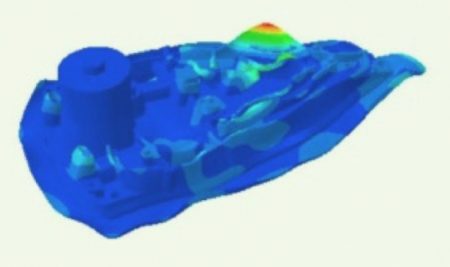
Figure 1. Mode shape of the preliminary ultrasonic iron at around f = 35 kHz. Republished with permission from Elsevier from: https://doi.org/10.1016/j.apacoust.2018.01.024
In order to create a more effective ultrasonic iron, first of all, the authors designed and optimized a piezoelectric-type ultrasonic exciter with a working frequency range of 35–40 kHz. The exciter includes of piezoelectric ceramics, thermal isolator and electrodes (Figure 2).
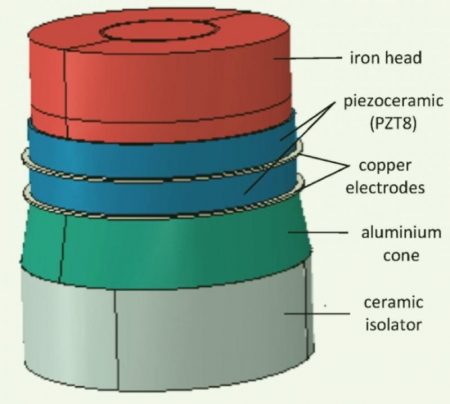
Figure 2. The model of the piezoelectric exciter. Republished with permission from Elsevier from: https://doi.org/10.1016/j.apacoust.2018.01.024
Then, the authors revised and optimized the iron structure to create more effective ultrasonic vibrations in order to minimize limescale accumulation. The mode shapes of the optimized ultrasonic iron suggested that the vibrations within 35–40 kHz could be quite effective in the steam generating chamber, steam passageways, and the rear chamber compared to the preliminary situation (Figure 3).
It is worth restating that these locations are where lime particles are mostly seen to accumulate. The predicted mode shapes implied that a narrow band excitation could create effective vibrations at the desired locations. In an effort to verify the predictions, a test rig was developed and ultrasonic vibration measurements on a prototype iron were carried out (Figure 4). It is seen that measured operational deflection shapes are quite similar to the estimated mode shapes (Figure 5).
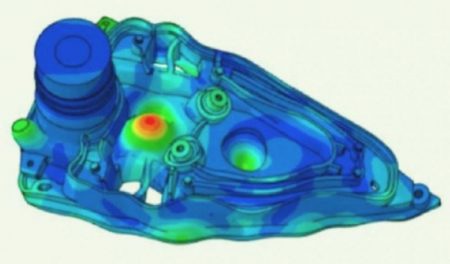
Figure 3. Mode shape of the optimized ultrasonic iron at around f = 35 kHz. Republished with permission from Elsevier from: https://doi.org/10.1016/j.apacoust.2018.01.024
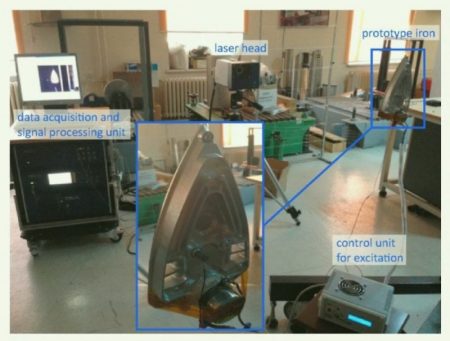
Figure 4. The experimental setup including the prototype steam iron with the excitation unit, the control unit for excitation, the laser head, and the data acquisition/signal processing unit of the laser vibrometer. Republished with permission from Elsevier from: https://doi.org/10.1016/j.apacoust.2018.01.024
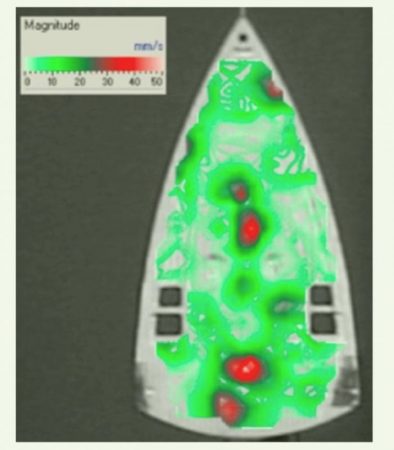
Figure 5. Vibration shape at around f = 35 kHz measured using a laser vibrometer. Republished with permission from Elsevier from: https://doi.org/10.1016/j.apacoust.2018.01.024
In conclusion, measurement of the operational deflection shapes confirmed the expected behavior of the prototype. Furthermore, both predicted and measured vibration results suggested that an ultrasonic excitation, with narrowband-sweeping frequency characteristics, could provide effective ultrasonic vibrations at desired regions in an iron.
The results of the theoretical and experimental vibration analyses, as well as the physical experiments on steam irons in this study, prove promising in the design of ultrasonic irons, so as to minimize the accumulation of limescale. Furthermore, the authors believe that ultrasonic vibrations can also improve performance by better smoothing wrinkles on fabrics and clothes. This is a topic which requires further research in the future.
These findings are described in the article entitled Application of ultrasonic vibrations for minimization of the accumulation of limescale in steam irons, recently published in the journal Applied Acoustics. This work was led by Hasan Koruk (MEF University), Muzaffer Serenli (Silter İleri Ütüleme Sistemleri Sanayi ve Ticaret Ltd), and Kenan Y. Sanliturk (Istanbul Technical University).