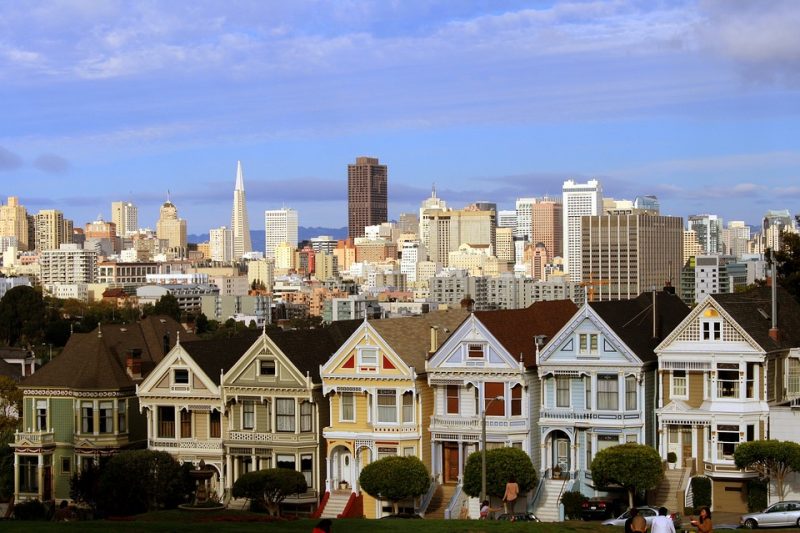
The last decades of worldwide social, economic, and technological developments have led to an increase in the number of people requesting energy-consuming living amenities. This results in an increased rate of primary energy use much higher than what could be justified by the population growth. Alongside the energy use increase rate, there has been a gradual rise in the average prices of conventional fossil fuels such as gas, oil, or coal.
Nowadays, these conventional fuels still cover a large share of primary energy needs and are, by far, the biggest contributors to the world’s greenhouse gas (GHG) emissions that lead, among other consequences, to climate changes and health problems. The need to question the use of these traditional fuels, of traditional energy conversion methods, and of current consumption patterns, has reached an unprecedented level of importance, and there is an imperative necessity to change them into low environmental impact, with secure and cost-effective alternative approaches based on renewable or highly efficient energy systems. The mentioned facts enlighten all applications or technologies that, somehow, work against these major issues.
One of those technologies receiving increasing attention from industries and research centers is the Organic Rankine Cycle (ORC). The ORC, which can be seen as a way to overcome the difficulties opposing the practical implementation of the Carnot Cycle, in its basic configuration involves four main components: a pump, an evaporator, an expander, and a condenser, as shown in Fig. 1. Its working principle may be briefly described as follows. The cycle starts with the pressurization of the working fluid in the pump leading to the evaporator, where it is heated and vaporized (and eventually superheated) by a heat flux from a suitable heat source. The pressurized vapor flows into the expander where it produces work while decreases its temperature and pressure. The low-pressure vapor at the exit of the expander is then directed to the condenser where, losing energy to a suitable low-temperature heat sink, passes from vapor into a liquid phase. The condensed fluid is then conducted to the pump to be pressurized again, closing the cycle.
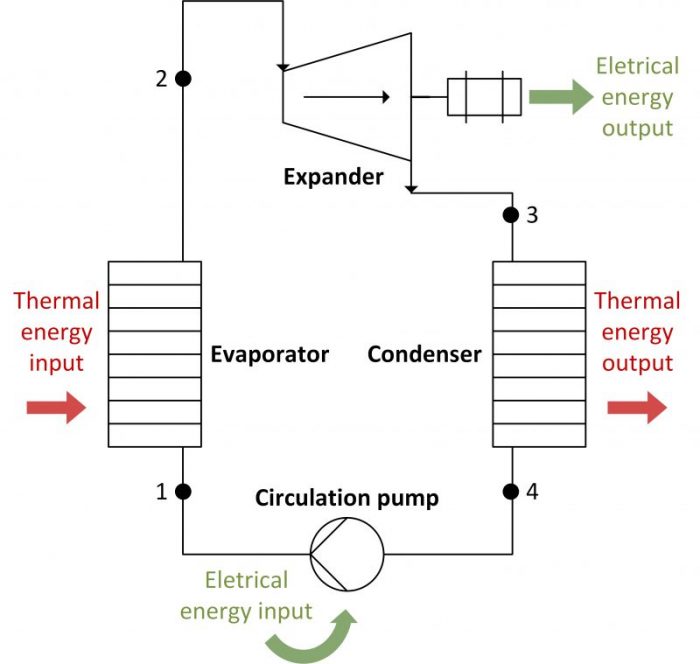
Fig. 1 – Schematic representation of a basic ORC with its main components and the energy fluxes. Published with permission from João S. Pereira
Often used together with ORC technology is the well-known technique of simultaneous production of heat and power, also known as CHP (Combined Heat and Power). CHP systems not only reduce the losses of the energy conversion process but also avoid the losses associated with its transportation and distribution, improving the sustainability of the whole process and contributing to the increase of grid reliability and to the reduction of grid dependence. Moreover, they not only provide significant savings over individual heating and power systems in terms of operational costs and of primary energy consumptions but also in terms of GHG emissions. Many researchers are referring to CHP, worldwide, as the major alternative to traditional systems in terms of significant energy savings and environmental conservation.
Micro-CHP is the designation given to the cogeneration systems that are able to fulfill thermal loads that range from those typical public/commercial buildings (e.g. health centers or small and medium-sized enterprises (SME)), down to the needs of residential dwellings. In terms of nominal electrical power, these systems range from below 1 kWe to 50 kWe. At medium-to-large scale (electrical power above 50 kWe), CHP systems are a mature technology with a fairly widespread use, while the micro-scale systems are still limited by several problems. Nevertheless, the potential market for systems of this scale is huge since one of their possible applications is the domestic hot water generation (for sanitary and space heating purposes).
The most promising market for the micro-CHP systems lies in the residential sector, especially in countries like the United Kingdom, The Netherlands, Germany, France, Italy, Belgium, Denmark, and Ireland. In fact, the annual dimension in sales and stocks of the European residential boiler market in 2013 was around 8 and 100 million of units, respectively; while the sales and stocks of all other micro-scale sectors (e.g. SME or collective markets) is around 1 and 20 million of units, respectively.
The enormous dimension of the European potential market of micro-CHP systems can also be envisaged based on their predicted sales and stocks, for the years 2020 and 2030, shown in Table 1. On that table, the potential benefits that arise from the installation of all those micro-CHP systems in terms of primary energy savings and GHG emission reductions are also shown. The numbers presented in Table 1 implicitly assume a pro-active and a strong political will regarding the promotion of the use of micro-CHP products. Acknowledging the great potential of micro-CHP products, considered as the “boilers of the future,” the European Committee for Standardization (CEN) already drawn several standards addressing the product characteristics and the evaluation of their efficiency. Some certification entities, such as the Eurovent Certita Certification, have already used these standards to develop certification schemes for these kinds of products.
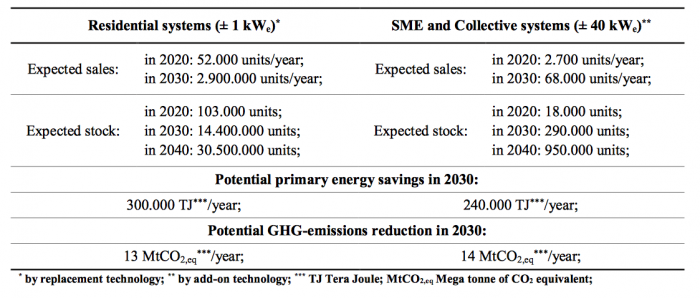
Table 1 – Micro-CHP predicted sales, stocks and potential primary energy savings and GHG emission reductions for the residential and SME/collective sector of the EU-27 (source: CODE 2 – Cogeneration Observatory and Dissemination Europe. Micro-CHP potential analysis – European level report; 2015). Published with permission from João S. Pereira
In spite of the huge market and the potential benefits regarding primary energy savings and GHG emission reductions that are known to result from their widespread use, micro-CHP systems have still not reached a sufficient state of maturity to be considered an actual valid alternative to the standard domestic heating systems wherein the gas and electricity prices will play a very important role to achieve a competitive unit that needs to be characterized by a low investment cost and easy operation.
ORC technology appears as the most suitable and promising solution to convert low-grade heat into power since it is the simplest and the less likely to create difficulties in retrofitting the current heating systems in domestic dwellings. In fact, two of the most important ORC components for micro-CHP systems, the pump and the condenser, are completely off-the-shelf products; while different kinds of expanders and working fluids have been deeply characterized and studied for this type of use. However, when high-temperature sources (e.g. biomass/ natural-gas combustion gases) are employed, an intermediate circuit between the heat source and the organic fluid heat-exchanger (the ORC-evaporator) has been used.
The use of this intermediate circuit, conceptually more complex and less efficient, can be justified by the absence of a market available OCR-evaporator capable of performing a direct energy exchange between the high temperature combustion gases and the power cycle, by concerns regarding the possible thermal degradation of the organic working fluid or even by difficulties in controlling the system. Nevertheless, this appears not to be the best solution for a residential application since it will promote, at least, longer response times due to its higher thermal inertia. To mitigate these longer response times, manufacturers are forced to add to the micro-CHP unit a thermal storage tank; however, this can preclude the retrofitting of the wall-mounted conventional or combi-boilers currently applied in residential dwellings.
To take advantage of the huge economic and environmental potential that comes from the replacement of the residential heating systems by CHP units, the way primary energy reaches the ORC-evaporator needs to be reformulated, and more studies, or even the development of a new concept of evaporator, capable to deal with all the residential restrictions, appear to be necessary.
These findings are described in the article entitled ORC based micro-cogeneration systems for residential application – A state of the art review and current challenges, recently published in the Renewable and Sustainable Energy Reviews Journal. This work was conducted by João S. Pereira ([email protected]), José B. Ribeiro, Ricardo Mendes and Jorge C. André from ADAI-LAETA, Department of Mechanical Engineering, University of Coimbra and Gilberto C. Vaz from ISEC, Polytechnic Institute of Coimbra, Department of Mechanical Engineering.