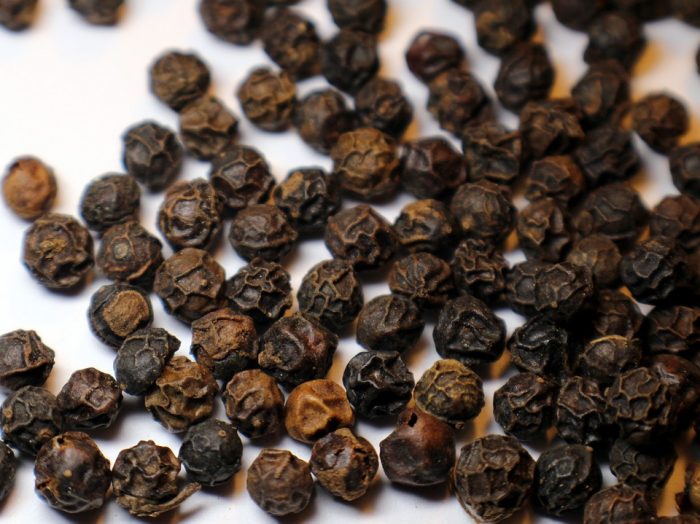
Spices occupy a unique place in our diet due to their distinct aroma, color, and taste. In general, spices are primarily preferred in powdered form. The quality and safety of the spice powder need to be addressed by processors for better consumer acceptability.
Grinding or milling, a size reduction operation, is a traditional method of obtaining spice powder. However, heat generated during the energy-intensive grinding process results in the loss of thermo-sensitive flavoring compounds. The limitations of traditional grinding processes, such as high energy requirements, loss of flavoring components or volatile oil, and restricted particle size can be ruled out by advancing cryogenic grinding (cryo-grinding) method. In the cryo-grinding technique, the grinding of spices is performed at a lower temperature with the aid of a cryogen such as liquid nitrogen (LN2; boiling point −196 °C) to obtain a superior quality of the powder.
Nevertheless, the higher operating costs and overall energy requirements restrict the industrial application of cryo-grinding techniques, particularly in developing nations. A cryo-grinding unit usually consists of two main components, namely, (i) precooler (to lower a spice temperature with the aid LN2 such that spice becomes brittle); and (ii) grinder/mill/cryo-mill (any mill used for grinding the brittle spice).
The operational cost of cryo-grinding can be reduced by efficient utilization of LN2 at an optimal grinding temperature. Furthermore, the understanding of micro-mechanical behavior and heat transfer phenomena of the granules at the optimal cryo-grinding condition is obligatory in improving the design aspects of the system. The breakage of brittle spices in a cryo-mill may happen due to individual or combination of size reduction mechanisms, i.e., impact, compression, cutting, and shearing; however, the exact mechanism is still unknown. Direct analysis of particle breakage and motion of spices in cryogenic condition is often difficult due to practical measurement limitations and higher cost association compared with the analytical/numerical techniques [1–3]. However, the relevant numerical modeling method should be selected to model the complex cryo-grinding phenomena accurately.
The discrete element method (DEM) is a potential mechanistic/predictive numerical method that can provide an in-depth understanding of particle mechanics in complex operations such as cryo-grinding. The paper uses DEM modeling to represent three-dimensional motion and breakage phenomena of black pepper seeds, The King of Spices, in a cryo-mill/hammer mill at an optimized cryo-grinding condition. Hertz-Mindlin contact model coupled with Bonded particle model (BPM) was utilized in EDEM software (EDEM 2.7.1 Academic Version, DEM Solutions Ltd., Edinburgh, UK) for the DEM modeling. BPM was used to create a breakable body/whole particle/black pepper of 5 mm size (assembly of fraction particles) by cementing a packed mono size distribution of 255 and 552 soft spheres or fraction particles (0.5 mm), separately. The granules/particles interact as per Hertz-Mindlin contact model before bond formation and after bond breakage.
In the first part of the study, BPM parameters or bond parameters were calibrated in DEM using uniaxial compression test. Calibrated set of bond parameters for the whole particle made of 255 fraction particles are as followed: 3.12 × 1011 Pa m−1 normal stiffness, 1.56 × 1011 Pa m−1 shear stiffness, 3.88 × 108 Pa critical normal stiffness, and 1.94 × 108 Pa critical shear stiffness. The numerical simulation with this calibrated values of BPM parameters along with calibrated DEM material and interaction parameters [3] provided a close agreement with the experimental findings. Failure force, failure strain, and failure time vary within 10.79%, 3.85%, and 25.23%, respectively of the experimental outcomes which can be observed in the force-deformation curve (Fig. 1).
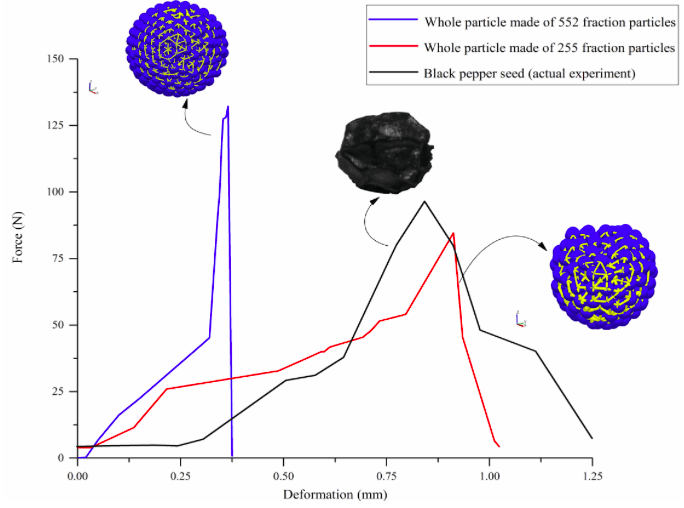
Fig. 1. Comparison of force-deformation curve of actual black pepper seed, whole particle made of 255 fraction particles, and whole particle made of 552 fraction particles [4]. Republished with permission from Elsevier from https://doi.org/10.1016/j.apt.2018.01.023.
In the second part of the study, the validity of a calibrated set of BPM parameters along with calibrated DEM material and interaction parameters [3] were tested for 50 whole particles each made of 255 fraction particles in the hammer mill at the optimal cryo-grinding condition. The optimal conditions such as −43 °C grinding temperature, 26 m s−1 peripheral speed of the rotor, and feeding sample at 1.5 kg h−1 and −50 °C were maintained closely during experimentations. The term breakage defines initial rupture/failure in bonds of the whole particles which followed partial disintegration and then completes disintegration, i.e., ≥ 90% failure of the bonds. Initial breakage was observed at hammer surface on some instances while partial disintegration and or complete disintegration of whole particles majorly occurred at the periphery of mill casing as shown in the whole particle, vector, and bond breakage snapshots (Fig. 2).
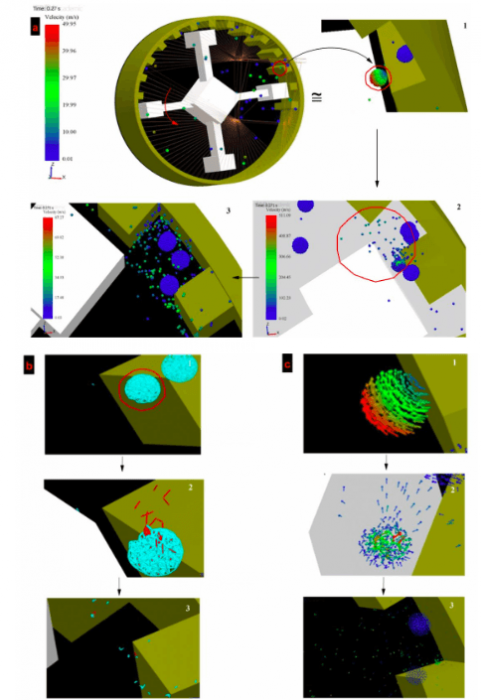
Fig. 2. Event of whole particle breakage to disintegration at the right side of milling chamber: (a) particle, (b) bond, and (c) vector images [4]. Republished with permission from Elsevier from https://doi.org/10.1016/j.apt.2018.01.023.
The problems of backflow at the feed section of the mill and cushioning effect (fraction particles act as a buffer of the shield) at the hammer surface were associated with the cryo-grinding operation which may have restricted further reduction in particle size. Thus, appropriate modifications were suggested in the hammer mill geometry. Overall, DEM modeling offered an insight into the milling process, particularly the flow pattern and mechanism of black pepper breakage. In the future, the calibrated model parameters of DEM can be coupled with a CFD code (for LN2/fluid flow) for precisely examining the granular heat transfer, breakage, collision, and flow dynamics in different cryo- mills.
These findings are discussed in detail in the article entitled Modeling breakage and motion of black pepper seeds in cryogenic mill, recently published in the journal Advanced Powder Technology. This work was conducted by Bhupendra M Ghodki, K. Charith Kumar, and T.K. Goswami from the Indian Institute of Technology Kharagpur.
References:
- D. Markauskas, R. Ramírez-Gómez, Á. Kačianauskas, E. Zdancevičius, Maize grain shape approaches for DEM modelling, Comput. Electron. Agric. 118 (2015) 247–258.
- V. Alexiades, A.D. Solomon, Mathematical modeling of melting and freezing processes, Washington DC, 1993.
- B.M. Ghodki, T.K. Goswami, DEM simulation of flow of black pepper seeds in cryogenic grinding system, J. Food Eng. 196 (2017) 36–51.
- B.M. Ghodki, K. Charith Kumar, T.K. Goswami, Modeling breakage and motion of black pepper seeds in cryogenic mill, Adv. Powder Technol. 29 (2018) 1055–1071.