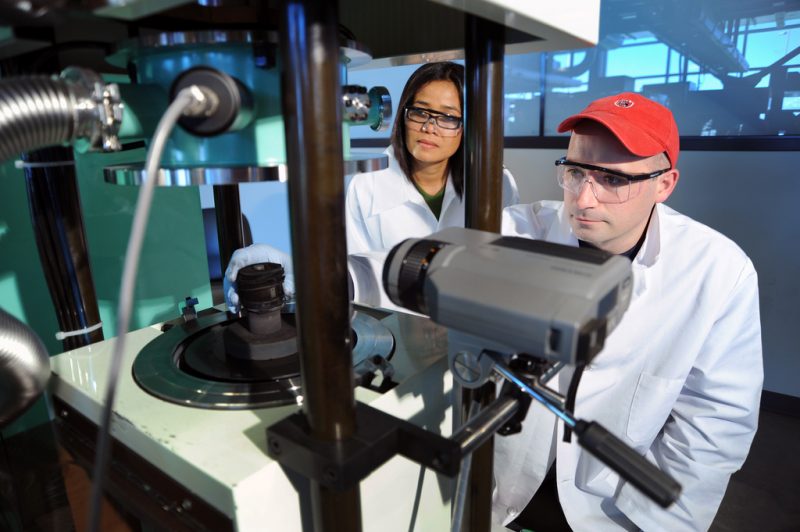
Sintering is the process of compacting a material, usually in powdered form, into a solid mass using heat or pressure, but without melting the material. It is a manufacturing technology that dates back to at least 3000 B.C. and was used to make ceramic objects that were hard to cast. Modern sintering of metallic and cemented carbides started in the 20th century. Today, nearly 20% of automotive parts are now produced by the powder metal (PM) sintering process.
The advantages of PM is the ability to produce net-shape parts that require minimal or even no machining. However, PM parts have pores, and this porosity has its advantages and disadvantages. The main advantage is that porous metals can be used to make oil-impregnated bearings that are, therefore, self-lubricating. The main disadvantage is that pores are actually defects in materials. The PM industry is, therefore, trying to make parts that have a high density (less porosity) for improved properties and performance. To make parts that approach the full density of the material being used is the “Holy Grail” of the PM industry.
One method for enhancing the density of sintered metal parts is to treat the parts with high magnetic fields. Many of us have seen demos where coins are shrunk in magnetic fields. The coins become smaller (a nickel becomes the size of a dime), but thicker, because the compressed material must go somewhere. With a sintered part, the same kind of magnetic treatment should simply push material into the existing pores, thus increasing the density of the part and decreasing its porosity. In addition, this magnetic compression will affect other properties of the part.
In this study, a small sample is placed inside a coil at the National High Magnetic Field Laboratory in Tallahassee, Fl. The sample had a radius of 0.375 (or 3/8) inches and a thickness of 0.3 inches. It was compacted to these dimensions with a pressure of 30 tons per square inch by Atlas Pressed Metals of DuBois, PA. The coil is connected to a capacitor charged to 7 kV. When the switch is closed, a large pulse of electric current (maximum value, one hundred thousand amps) runs through the coil for a little longer than a microsecond. The large current creates a large magnetic field in the coil of the order of 40 Tesla, or about eight hundred thousand times the strength of the earth’s magnetic field (magnetic fields in MRI machines are typically about 1 to 3 T). This magnetic field creates a maximum pressure on the sample of almost 60 tons per square inch.
The dimensional and property changes of the processed part depend on the electrical conductivity of the material. For steel, even with this large pressure, the volume of the sample doesn’t change much, but the small compression increases the density by about 2% when compared with a similar sample that is not subject to the magnetic field. In addition, the hardness of the sample is increased by the treatment. The texture of the em-processed specimen is also different, along with its response to heating and cooling cycles: the em-treated specimen shrank less when cooled and expanded less when heated. This means that it was less sensitive to temperature changes, a property that is highly desirable in many applications.
This initial study suggests that electromagnetic treatment of sintered parts can provide some advantages over sintering only. This process is also environmentally friendly, with few emissions.
These findings are described in the article entitled, Application of electromagnetic processing for development of high-performance sintered powder metal parts, recently published in the journal Current Applied Physics. This work was conducted by Daudi R.Waryoba from Penn State University and Winston Roberts from Florida State University.