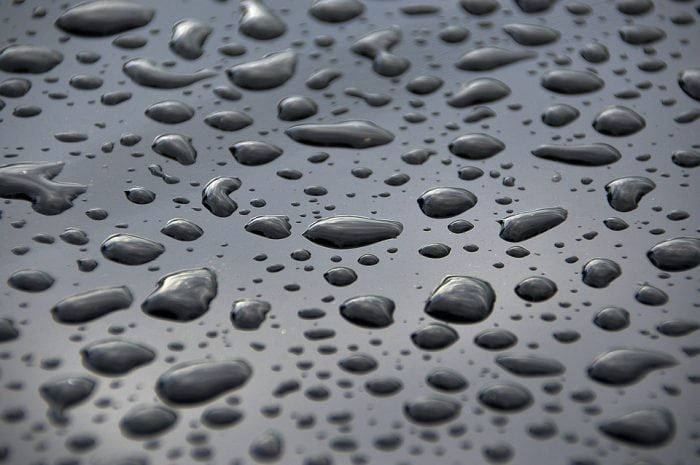
Self-cleaning surfaces are not easily wetted with water. Water droplets build upon such surfaces and roll away easily. This property affects surface properties such as oxidation, icing, bio-fouling, corrosion, wear, scaling, and dirt accumulation. Such properties are desirable in the water, cryogenic, refrigeration, wind turbine, and aerospace industries as well as in satellite dishes, solar energy panels, photovoltaics, exterior architectural glass, and greenhouses.
Self-cleaning properties are achieved by controlling the wettability of surfaces with water as characterized by their contact angle, i.e. the angle formed between a water droplet and a flat solid surface. If the angle is between 0 to 90 degrees, water wets the surface effectively, and the surface is hydrophilic. If the angle is in the range of 90-150, the surface is hydrophobic. A super-hydrophobic surface is one with a contact angle larger than 150 degrees.
The interest on super-hydrophobic surfaces has risen after the discovery of the self-cleaning properties of lotus leaves when it was found out that micro/nano surface features combined with low surface energy brings super-hydrophobic properties. Two strategies have been adopted in recent years for creating super-hydrophobic surfaces, i.e. roughening of intrinsically hydrophobic surfaces or chemically modifying the hydrophilic surfaces with low surface free energy coatings and compounds.
In order to associate physical and chemical properties with wettability, different models have been presented over the years. Yaung’s model describes the contact angle on ideally flat surfaces. Wenzel and Cassie-Baxter’s models are used to determine the contact angle on rough and undulating surfaces. Wenzel’s model is dominant for homogenous interfaces with low surface roughness. According to this model, the droplet maintains contact with the surface and can penetrate all the asperities. On the other hand, at a high surface roughness of appropriate size range, a droplet of water may rest on top of the peaks of the surface never coming in to direct contact with the valleys of the surface. Within these valleys, air pockets are trapped between the solid and liquid phases which consequently alter the wetting and surface properties of the material.
In the past few years, most super-hydrophobic surfaces have been principally made from the low surface energy materials and coatings, such as polymers, glasses, carbon nanotubes and silicon nanowires. However, these materials usually have a low mechanical strength and poor bonding with the substrate, leading to a short lifespan in service which limits their practical applications.
Recently, efforts have been devoted to fabricating super-hydrophobic surfaces on metallic surfaces. For metallic materials, mechanical abrasion, anodic oxidation, chemical and electrochemical deposition, chemical etching and phase separation have been used to increase the surface roughness, whereas techniques such as physical vapor deposition (PVD), chemical vapor deposition (CVD), and solution immersion have been used for modification of the surface energy. Most of these methods are either complicated, time-consuming, need special equipment for scaled-up applications, or require expensive chemicals that make the fabrication costly. Moreover, insufficient lifetime stability or adherence to the metallic substrates, lack of biocompatibility, as well as health issues related to the secondary coatings, are the main drawbacks of the current state of the art. For these reasons, development of simpler and more efficient methods to create stable and durable surfaces seems to be necessary.
The idea behind this work is that if surface hydrophobicity could be obtained through adjustment of surface microstructure, it will not be easily lost during service and provides a cheaper longer lasting solution to hydrophobicity problem.
Wettability is influenced by the interaction of the interfacial energies of phases present at the triple solid-liquid-gas joint, as well as surface roughness, surface heterogeneity, and physical and/or chemical processes occurring at the solid-liquid interface. Therefore, microstructural parameters of metallic alloys, such as their phase types, alloying elements distribution, grain size, grain orientation, texture, state of strain, and state of oxidation can affect wetting angle by altering the interface energies of the solid surface. One could imagine that the ideal method for creating a low wettability surface is to tailor its surface microstructure and roughness during the primary manufacturing process so that any need for subsequent secondary processing is eliminated.
Therefore, our group has embarked on a study on the effect of microstructural characteristics such as grain size and phase type on wetting angle of metallic surfaces. The overall objective of the study is to design cast surfaces with tailored hydrophobic properties and to develop an in-situ method to manufacture the same by controlling the surface architecture, where any need for subsequent secondary treatment is eliminated.
This work was directed toward cast iron because if its widespread use in water transmission equipment and accessories. Pipes, fittings, and pump bodies are among the most commonly used parts made of gray cast iron. However, gray cast iron is prone to corrosion and fouling. The common practice for reducing corrosion in parts made of gray cast iron is coating the parts with proprietary polymers such as Tridecafluoro tetrahydrooctyl, Polytetrafluoroethylene, and Fluoroalkyl phosphate. Reducing the wettability of cast iron surfaces without the need for any further coating or secondary treatment will be a valuable way of reducing the production costs and improving the production efficiency.
In this research, a gray and a white cast iron with a similar chemical composition were cast and the effect of surface microstructure, roughness, and oxidation on their wetting characteristics were examined. First, a Fe-2.6C-2.9Mn-1.8Si cast iron was melted and cast in a chilled sand mold corresponding to ASTM chill test standard (ASTM A367). Optical microscopy of the cast sample showed that the lowest section of the casting solidified with a white cast iron microstructure due to the very high cooling rate near the chill. Above the white cast iron layer, there was mottled followed by gray cast iron microstructures with different flake graphite distributions which varied with height from the chill. Wettability of two sections, one with white cast iron microstructure and the other with gray cast iron microstructure was studied. Two different methods, i.e. mechanical abrasion and electroetching, were used for surface roughening.
In the first method, samples were mechanically abraded in four stages with 80, 320, 800, and 1200 grit sandpapers. At each stage of roughening, the wetting angle and roughness of the surfaces were measured. In the second method, samples were polished with 0.3 µm alumina powder and their wetting angles and roughness were measured. The polished samples were then electroetched with a solution of 96% acetic acid and 4% perchloric acid and their wetting angle and roughness were measured. Electroetching was then repeated for the second, third and fourth time (stage) on each sample following the same procedure and the wetting angle and roughness of electroetched samples were measured after each stage. Furthermore, after the final electroetching stage, samples were left in the air and their wetting angles were measured after 1, 2, 3 and 4 weeks.
Size of microstructural features was measured using a scanning electron microscope (SEM) and it was made sure that the size of the droplets used in this study (2 µl of distilled water) were sufficiently larger than both the microstructural features and the wavelength of the surface asperities of the samples.
A simplified geometrical surface roughness model was developed to determine the wetting angles according to Wenzel and Cassie-Baxter models as well as the solid fraction in contact with water droplet in Cassie-Baxter model using experimentally obtained results.
It was shown that, on average, water could penetrate about 90% of the height of the peaks above zero line of the surface roughness profile and the average height of the unwetted part of the peaks above zero line was about 10%. It was concluded that the wetting regime followed a quasi- Cassie-Baxter behavior.
The gray cast iron sample with lower roughness values (stages 1 and 2 of electroetching process) generally followed the quasi-Cassie-Baxter prediction. In stages 3 and 4 of electroetching, however, with an increase in surface roughness, the wetting behavior appeared to follow the Wenzel prediction and changed little with increase in roughness. In all stages of mechanical abrasion, wetting of the gray cast iron sample followed Wenzel model. The electroetched white cast iron sample, which had a much smoother surface, followed a Wenzel type behavior in all stages of electroetching as well.
A general decreasing trend in the wetting angle with increasing the surface roughness was observed in the mechanically abraded white cast iron sample suggesting full penetration of water into surface asperities. However, wetting behavior of the surface of this sample did not follow either of Wenzel or Cassie-Baxter models. The surface of gray cast iron sample in stages 1 and 2 of the electroetching process followed the Cassie-Baxter model.
In order to determine the extent of water penetration in the surface asperities of these surfaces, the average heights of the trapped air and the water penetration height in grooves were calculated. The results showed a high tendency for water to penetrate into the surface asperities and that only a little fraction of air could be trapped between the surface and water, which in turn, favored reduction of the water contact angle.
To sum up, the results obtained revealed that wetting behavior of cast iron samples of a given composition is influenced not only by the surface roughness but also by the surface roughening method and the type of phases present in the microstructure. In gray cast iron, selective electroetching can create a surface roughness on a different length scale than mechanical abrading. These findings suggest that investigation of the wetting behavior of a rough surface is a very complex process which cannot be simply predicted by the two classical models of Wenzel and Cassie-Baxter.
Another parameter investigated in this study was the effect of air exposure on the water contact angle of gray and white cast iron samples. If the characteristics of a surface change with time due to air exposure, so should its contact angle.
The results showed that wetting angles of both samples increased to above 90˚ just after one week of air exposure rendering them hydrophobic. Comparison of SEM micrographs of gray and white cast iron samples immediately after stage 4 of electroetching and after 1 week of air exposure, indicated a change in the surface characteristics of both cast iron surfaces after 1 week of air exposure. It appeared that a surface layer had been formed on parts of the microstructure as a result of air exposure.
Other researchers have shown an increase in the carbon and oxygen content of metallic surfaces exposed to the atmosphere using X-ray photoelectron spectroscopy (XPS) and Energy-dispersive X-ray spectroscopy (EDS) analyses. The changes in carbon and oxygen content have been associated with the adsorption of hydrocarbons onto the surface and formation of metallic oxides on metallic surfaces, respectively. However, since metallic oxides are not hydrophobic, they do not favor higher contact angles, and the induced hydrophobicity of metallic surfaces exposed to air should be mainly associated with the formation of a low surface energy carbon layer through adsorption of hydrocarbons onto the surface.
The results presented are the preliminary results of a more extensive research on the effects of type, percentage, size and distribution of different phases present in the microstructure, as well as the surface roughness and roughening method of cast iron samples of a given composition on their surface water contact angle.
Considering the results obtained, one could expect that a combination of microstructural and surface treatment parameters as well as recognizing the related influencing factors, would eventually lead to the ability of tailoring of the wetting behavior of surfaces by controlling their microstructure, roughness, roughening method, and environmental exposure.
These findings are described in the article entitled Effect of microstructure and surface features on wetting angle of a Fe-3.2 wt%C.E. cast iron with water, recently published in the journal Applied Surface Science. This work was conducted by Samira Riahi and Behzad Niroumand from the Isfahan University of Technology, and Afsaneh Dorri Moghadam and Pradeep K. Rohatgi from the University of Wisconsin-Milwaukee.