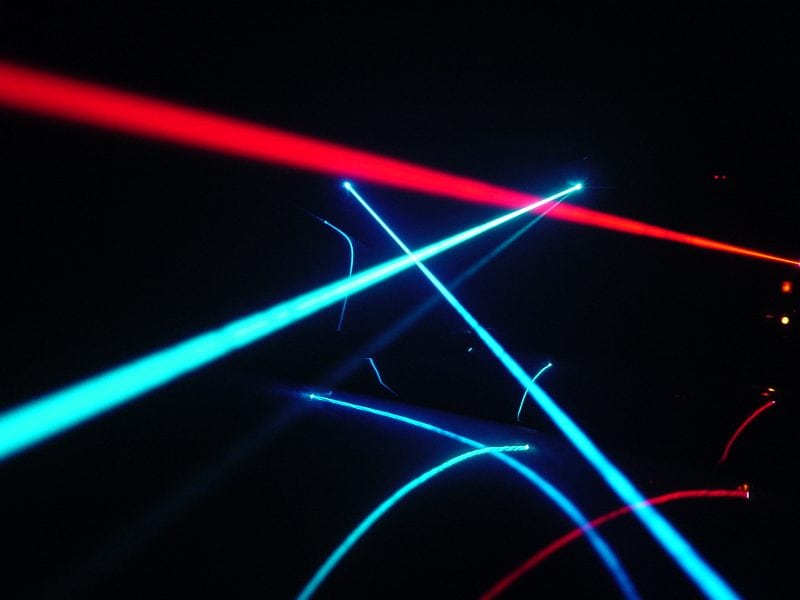
The photoacoustic effect, which was discovered by A. G. Bell in 1881, refers to the generation of sound as a result of absorption of optical radiation. The effect takes place in gases, liquids, and solids following conversion of the optical energy into heating. For almost any material, heating causes an expansion, which, as a mechanical motion, results in the launching of a sound wave. In the case of a gas, it is easy to see from the ideal gas law
PV=nRT
where P is the pressure, V is the volume, n the number of moles, R the gas constant, and T the temperature, that an increase in the temperature of a gas as a result of absorption of optical radiation results in a pressure increase for a fixed volume of gas. When the light source, typically a laser, is intensity modulated, the gas temperature varies as well resulting in a pressure variation at the frequency of light modulation that can be detected with a microphone.
Interest in the photoacoustic effect was stimulated in the 1970’s following the discovery of high power infrared lasers for use as the optical source. The high power and narrow bandwidth characteristic of lasers resulted in much greater signal amplitudes for the photoacoustic effect in comparison with what conventional light sources produced so that photoacoustic measurements became practical, especially in the field of trace gas detection.
The employment of modulated, continuous wave lasers tuned to the absorptions of gases in the infrared showed that use of an infrared laser together with a microphone and lock-in detector resulted in a technique with remarkably high detection sensitivity and respectably high selectivity. The basic method of trace gas detection shown in Fig. 1 uses a continuous laser, a chopping wheel, an acoustic resonator equipped with a pair of infrared transmitting windows in which the gas sample is placed, a microphone, and a lock-in amplifier which records the sound pressure level in phase with the modulation.
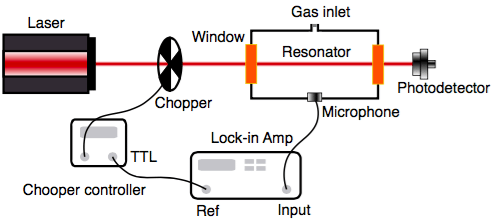
Fig. 1. A typical setup for photoacoustic trace gas detection. A continuous laser beam whose wavelength tuned to the absorption of target gas is intensity modulated by a chopping wheel is directed into an acoustic resonator equipped with a pair of infrared transmitting windows. The pressure within the resonator varies in accord with the laser heating, thus generating a cylindrical acoustic wave which is detected by a microphone. The voltage signal at the modulation frequency is then filtered and amplified by a lock-in amplifier. Credit: Wenyu Bai
In principle the sensitivity of photoacoustic detection is governed by two factors: first, the laser power and the strength of the molecular absorption, which governs the amount of optical power deposited in the photoacoustic cell; and, second, the sensitivity of the microphone, which is remarkably high. With the basic configuration shown in Fig.1, it was found that although the sensitivity of the photoacoustic effect was high, a small acoustic window signal generated at the entrance and exit windows of the photoacoustic cell gave a background signal that limited detection sensitivity from its theoretical limit. Over the years, there have been numerous schemes employed to reduce the amplitude of the window signal each of which has given a concomitant increase in detection sensitivity.
Although it was shown by Gusev and Karabutov some time ago that when a laser beam is moved in a one-dimensional geometry at the speed of sound in an absorbing medium that the photoacoustic amplitude increases linearly with time and without bound (at least according to the laws of linear acoustics), there has been no practical application of this effect until recently when a group at Brown University showed that it could be used to advantage in trace detection, in particular for eliminating the window signal. To create a source moving at the speed of sound, the Brown group passed the 10.6 μm output from a CO₂ laser through a pair of acousto-optic light modulators which split the laser beam into two beams with slightly different frequencies, which when combined in a detection cell made a grating in the light intensity with a wavelength of Λ. Since the frequencies of the beams from the modulators were made to be different by an amount f so that fΛ=c, where c is the sound speed, the optical fringes in the grating moved at the sound speed.
The ultrasonic wave generated at each antinodal region of the grating moved towards a highly sensitive BiB₃O₆ crystal, specially fabricated by the Yu group at Shandong University, with a resonance frequency of 443.15 kHz and a quality factor of 10,800. In addition to generating a voltage, the crystal reflected the acoustic wave back to a second surface inside a photoacoustic resonator located a few cms from the crystal so that a longitudinal resonance of the acoustic cell was created resulting in a standing acoustic wave. The voltage from the BiB₃O₆ crystal was amplified and fed to a lock-in amplifier at the crystal resonance frequency, as shown in Fig. 2.
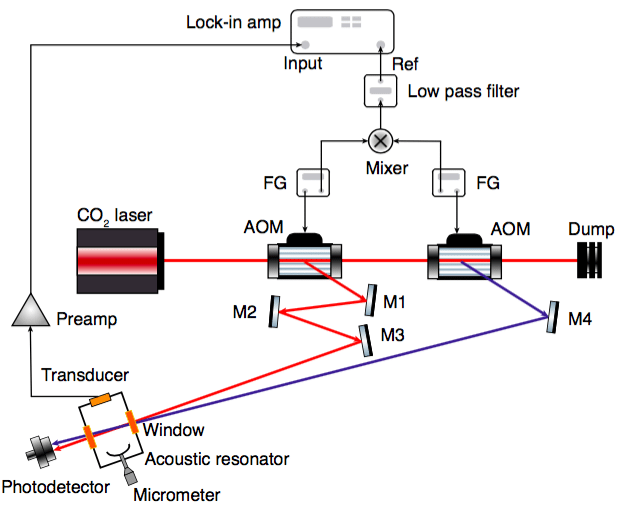
Fig. 2. Experimental apparatus using a moving infrared grating for photoacoustic trace gas detection. A 10.6 μm cw CO₂ laser beam enters two acousto-optic modulators consecutively. The frequency difference between two first-order diffracted beams is tuned to match the resonance frequency of the piezoelectric crystal that is used as the acoustic transducer. Two diffracted beams intersect within the acoustic resonator with the angle tuned by rotating the mirror such that the moving speed of the grating matches the sound speed. The acoustic resonator is made of two parallel ZnSe windows, a resonant transducer, and a concave reflecting surface attached to a micrometer thus enabling adjustment of the resonator length for constructive interference of the acoustic wave. The signal is processed by a lock-in amplifier with the reference frequency provided by first mixing the signal from two function generators, and then passing it through the low pass filter to generate the difference-frequency signal. FG: function generator; AOM: acousto-optic modulator; M: mirror. Credit: Wenyu Bai
It was found in the experiments that the resonant cell acted much like a laser resonator with two end reflecting surfaces. As such, total enclosure of the acoustic wave as is the case with most photoacoustic detection schemes was not necessary–the device could operate in the open air. Another feature of the detector is that there was virtually no interference found from electrical or acoustic noise sources at the relatively high frequency of 443 kHz. The salient feature of the instrument is its high sensitivity, which was recorded to be 750 parts-per-quadrillion of SF6 in ultrapure (99.999% ) Ar. Aside from the remarkable properties of the resonant crystal, the sensitivity of the experiment can be attributed to a triple-resonance where the resonance frequency of the crystal, the longitudinal resonance frequency of the acoustic cell, and the frequency of the acoustic wave matched to the sound speed of the gas were all made to be identical.
The results published by Lian Xiong, Wenyu Bai, Feifei Chen, Xian Zhao, Fapeng Yu and Gerald J. Diebold, in the Proceedings of the National Academy of Sciences 114, 7246 (2017) DOI:10.1073/pnas.1706040114 should expand the capabilities of the already powerful trace gas detection capabilities of the photoacoustic effect for pollution detection in the atmosphere.
These findings are described in the article entitled Photoacoustic trace detection of gases at the parts-per-quadrillion level with a moving optical grating, recently published in the journal Proceedings of the National Academy of Sciences. This work was conducted by Lian Xiong, Wenyu Bai, and Gerald J. Diebold from Brown University, and Feifei Chen, Xian Zhao, and Fapeng Yu from Shandong University.