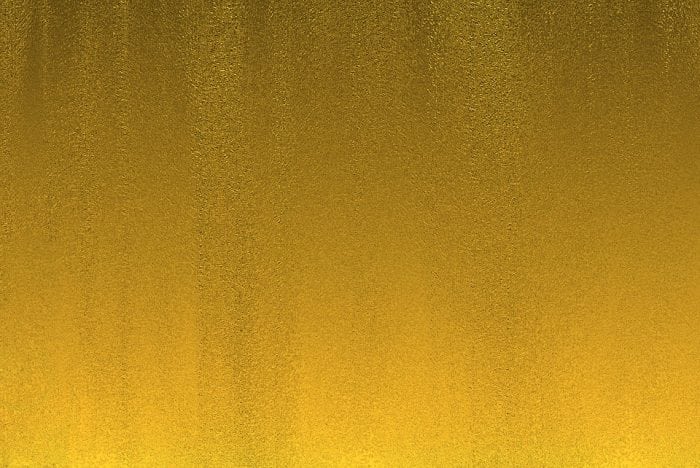
Sustainable ammonia production is vital for the global population growth due to ammonia’s wide use as a fertilizer in agriculture. The global production of ammonia was 146 million tons in 2015 and is estimated to increase by 40% in 2050. Additionally, ammonia, as a carbon neutral liquid fuel, can be utilized for the development of a clean transportation sector. Ammonia can be a promising substitute for hydrogen as a combustion fuel with superior advantages in terms of energy density, ease of liquefaction, and high hydrogen content (i.e., 17.6 wt%).
Conventional ammonia synthesis mainly relies on the Haber-Bosch process, which converts nitrogen and hydrogen to ammonia at high operating pressures (150-250 bar) and temperatures (350-550oC) over iron-based catalysts. The extreme condition requirements for this process necessitates high-cost demands for centralized infrastructure that should be coupled with the global distribution system. Additionally, this process consumes 3-5% of the global natural gas supply, 60% of the global hydrogen production, and emits 450 million metric tons of CO2 annually.
As the cost of renewably-derived (e.g., solar and wind) electricity continues to decrease given the rapid progress in technology and economies of scale, there is a growing interest for ammonia electrosynthesis from nitrogen and water under ambient conditions. This approach can provide an alternative pathway to the Haber-Bosch process for an energy-efficient, clean, and distributed ammonia synthesis.
Electrification of ammonia synthesis in a scale requires an effective electrocatalyst that converts dinitrogen to ammonia with a high yield and efficiency. To date, most studies have shown low electrocatalytic efficiency for ammonia production mainly due to the high energy required for N≡N cleavage and to the competition with the hydrogen evolution reaction (HER). Using molten salt systems and electrochemical lithium cycling strategy result in higher ammonia yield and faradaic efficiency; however, they are not energetically efficient and require high temperatures. Developing an efficient heterogeneous electrocatalyst to remarkably increase the rate of ammonia production through an energy-efficient and environmentally-friendly technique is imperative in energy and agriculture-based industries.
Gold (Au) has been known as one of the best catalysts for the electrochemical NH3 production through an associative mechanism where the breaking of the triple bond of N2 and the hydrogenation of the N atoms occur simultaneously. The selectivity of N2 molecules on the surface of nanocatalysts has been demonstrated to be one of the major challenges in electrochemical NH3 synthesis.
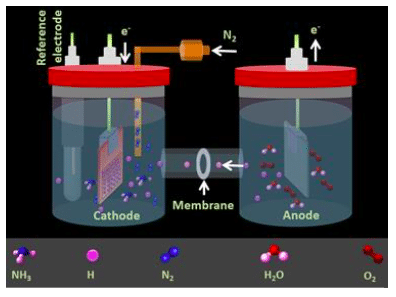
Figure 1: Schematic of an electrochemical cell for ammonia production. The anode and cathode compartments are separated by a cation exchange membrane (CEM). Republished with permission from Elsevier from https://doi.org/10.1016/j.nanoen.2018.04.039.
In our work, we showed that the nanoscale confinement of N2 near the electrocatalyst’s surface
enhances the conversion of N2 to NH3 remarkably using hollow Au nanocages (AuHNCs). The significant enhancement in the rate of reaction using AuHNCs is attributed to the entrapment of N2 molecules within the cavity, as these likely experience high-frequency collisions with the hollow Au interior surface of the cages. This increases the residence time of N2 molecules on the nanoparticle inner surface, which facilitates the conversion of N2 to NH3. Our reported ammonia yield rate and efficiency are greater than the highest values currently reported in the literature in aqueous solution under ambient conditions.
Electrochemical dinitrogen fixation experiments are conducted in H-type cells where anodic and cathodic compartments are separated by a proton conductive cation exchange membrane (Figure 1). On one side (anode) water is oxidized to produce oxygen gas and protons (H+). The protons produced at the anode are transported through the proton conductive membrane to the other compartment where supplied N2 gas and protons will produce NH3. This electrochemical ammonia generation system is fairly cheap and easy to operate with low maintenance demands.
Although at the first glance, it is thought that using Au is not economically feasible for the electrosynthesis of ammonia on a scale, due to the nanoscale nature of the particles, our calculation revealed that the cost of the material used for synthesis is only 8% of the price of ammonia ($800 per ton of ammonia) the farmers currently purchase in the market.
As this approach offers the potential to be scaled to industrial levels, it would be exciting if we can commercialize this technology and be able to produce farmers’ fertilizer need on site which mitigates the cost associated with ammonia transportation and storage. To this end, we are involved in a unique program at Georgia Tech called Technological Innovation-Generating Economic Results (Ti:GER) where we work with business, law professors, and practitioners to further explore the possibility of bringing our technology into the market.
These findings are described in the article entitled Enhancing the rate of electrochemical nitrogen reduction reaction for ammonia synthesis under ambient conditions using hollow gold nanocages, recently published in the journal Nano Energy. This work was conducted by Mohammadreza Nazemi, Sajanlal R. Panikkanvalappil, and Mostafa A. El-Sayed from the Georgia Institute of Technology.
References:
- Nazemi, M., Panikkanvalappil, S.R., and El-Sayed, M.A., 2018. Enhancing the rate of electrochemical nitrogen reduction reaction for ammonia synthesis under ambient conditions using hollow gold nanocages. Nano Energy, 49, pp.316-323.
“Electrocatalytic dinitrogen conversion for distributed ammonia production would be an inexpensive and sustainable approach for farmers to make their own fertilizer.”