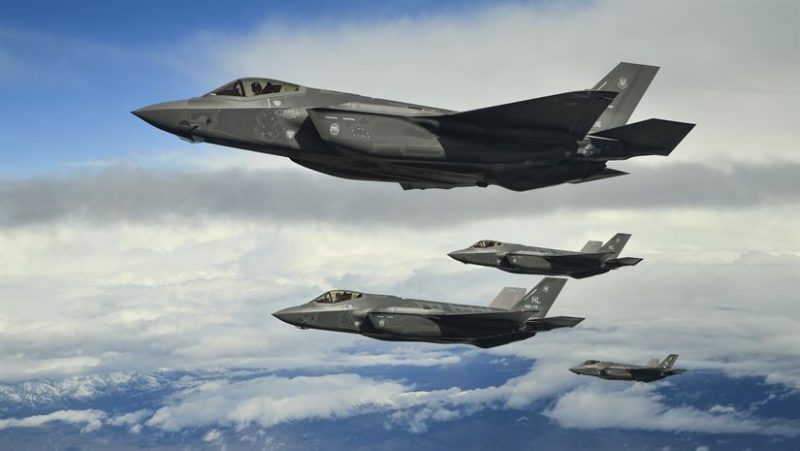
This research investigates the potential of using drones to inspect subsurface damage in composite aircraft materials. We develop a proof-of-concept remote line scan thermography capability in order to demonstrate the effectiveness and potential of such a system. A novel form of thermographic processing is developed and applied to detect subsurface damage on carbon fiber composite structures. This study suggests the viability of a drone-based thermography technology for the rapid and automated inspection of composite aircraft materials and paves the way for further implementation and testing.
Over the past few decades, the application of composites materials in aircraft construction has been steadily growing. When compared to metals, aircraft composites possess a high stiffness and strength-to-weight ratio, which affords reductions in aircraft weight, fuel consumption, and construction costs. Additionally, composites are more resistant to fatigue, but they are more vulnerable to impacts. Sources of such impacts range from hailstones to bird strikes to runway debris. Low energy impacts are of particular interest to operators as they can leave a surface unmarked yet cause significant damage inside. This type of damage is referred to as “barely visible impact damage” (BVID).
As this damage is unpredictable and difficult to detect visually, it poses a challenge for current inspection practice. A popular method of inspection for this damage is manual ultrasonic testing (UT), but this method is time-consuming if the location of impact is not known. As a result, routine screening for damage using UT is not undertaken by industry which means that subsurface damage can go unnoticed. As such, the development of a rapid and automated system to detect subsurface damage in aircraft composites is an area of considerable appeal in both research and industry.
In this study, we investigate the feasibility of a drone-based inspection system that employs thermal techniques to detect defects over wide areas. Active thermography is a technique that is well-suited to such an application. It employs a thermal imager to capture the heat signatures of a structure following an externally applied thermal excitation, which is then analyzed to identify potential subsurface defects. Sections that exhibit a temperature evolution different from that of surrounding structure can suggest the presence of a subsurface defect.
Heat evolution can be examined by heating a structured via a focused line of light. This line is scanned across the structure while a thermal imager records the cooling profile, allowing, in theory, an unlimited horizontal range to be scanned. This is known as line scan thermography (LST). Deploying such a technology on a drone offers a number of significant advantages but primarily the ease and speed with which BVID can be detected and sized.
A complicating factor in developing this technology is that there must be a reasonable stand-off distance between the drone and aircraft. Nearly all existing studies in LST assume a small standoff distance between heat source and specimen however for a drone-based application such distances introduce too many potential hazards. Through simulation, we demonstrated that it is feasible to provide sufficient light concentration to conduct LST from a distance, but implementation also requires the design of an optical device to produce this concentration. Using a custom design algorithm, we developed a reflector to maintain a highly concentrated beam of light at a distance of 500 mm, something that hasn’t been applied to LST previously.
To enhance the detectability of the defects, we also developed a novel processing method. By leveraging the movement of the imager, noise can be dramatically reduced by enhancing the contrast of moving parts of the thermogram. Because the imager is in motion, defects are seen as moving relative to the imager, while random noise does not. The dynamic elements in the scene are enhanced by applying pulse phase thermography (PPT) directly to the moving thermogram in a technique we have dubbed “dynamic pulse phase thermography” (DPPT). While more conventional methods such as static pulse phase thermography (SPPT) perform a preprocessing step to stabilize the dynamic scene, DPPT eliminates this requirement. By using DPPT, deeper defect detection was achieved at high scanning velocities.
To emulate the performance of a drone, this concentrator was mounted with a thermal imager onto a gantry. This configuration was used to inspect composite materials with both simulated and real impact damage. With a high-sensitivity infrared photon detector as the imager, a 10 J impact was detectable at a 200 mm/s scan speed, while using a low-cost microbolometer detection required a lower speed of 30 mm/s. These speeds are sufficient to inspect a full aircraft wing within a relatively short time.
Since the conclusion of this study, work has commenced on developing a software solution to simplify interfacing with the scanning technology and a drone deployable prototype for flight testing.
These findings are described in the article entitled Remote Line Scan Thermography for the Rapid Inspection of Composite Impact Damage, recently published in the journal Composite Structures. This work was conducted by James Moran and Nik Rajic from the Australian Defence Science and Technology Group.