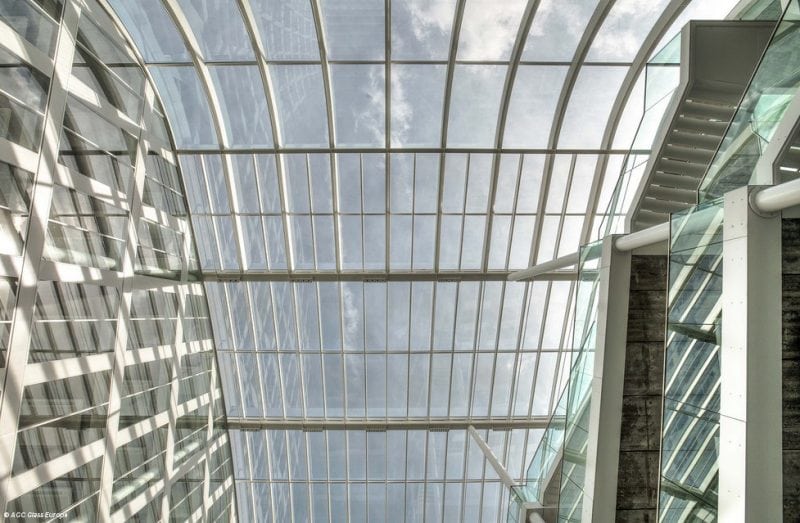
Laminated and hybrid glass systems are most typically made by bonding or joining together several structural components and materials. Their structural performance and safe design are, hence, related to the optimal combination of several parameters, including material properties and degradation, geometrical ratios, connections’ type and features, etc.
Given the typical brittleness of glass as structural material, as well as its increasing use in building components for load-bearing assemblies, research studies aimed to ensure appropriate safety levels as well as to optimize novel design concepts have been carried out by several researchers in the last years (see for example [1, 2]). So far, various projects have been also focused on the structural assessment of novel combinations or assessment of materials under certain loading conditions [3-10], as well as on the load-bearing performance of glass assemblies and composite/hybrid systems [11-17]. Different connection types have been also largely investigated [18-24], including mechanical, adhesive, and laminated solutions (see [25] for a state-of-the-art review).
Structural glass beams are already widely used in design projects for roofs and floors, as well as vertical fins and stiffeners for facades and pavilions. The design concept of “embedded laminated connections” to join together multiple glass parts, in this research scenario, currently represents a still-novel solution requiring further investigations.
In this regards, the ongoing research study takes advantage from past experimental efforts [26] and is focused on the numerical assessment of the load bearing performance of full-scale laminated glass (LG) beams with thick embedded connections [27], see Figures 1-2.
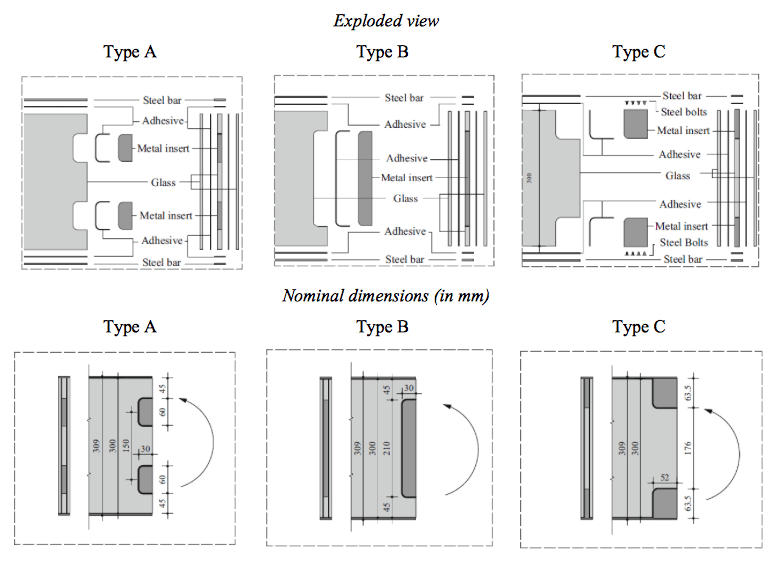
Figure 1. Geometrical features (frontal view) of embedded laminated embedded connections. Reproduced with permission from Elsevier, license number 4354080917915, May 2018
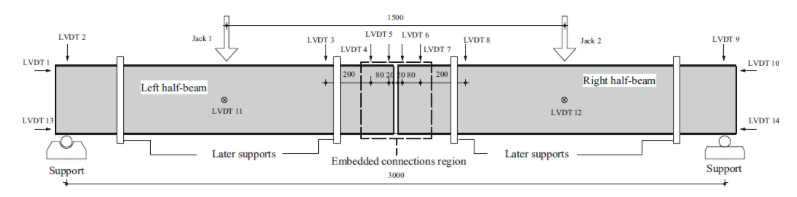
Figure 2. Reference test setup for bending experiments. Dimensions in mm, frontal view. Reproduced with permission from Elsevier, license number 4354080917915, May 2018
In accordance with [28-31], the structural interaction between multiple glass segments is offered by thick metal inserts, being embedded in the LG sections during the production stage. The overall bending response of such assemblies, given the same glass beam segments, is strictly related to the connection detailing, namely including the number, position, size, etc. of embedded connectors. In this regard, Finite Element numerical models able to properly capture their actual local and global behaviour can represent a robust support for time/cost-consuming, full-scale experimental investigations. Refined FE models are hence presented for selected specimen configurations and validated towards four-point bending experimental tests carried out on LG beams with three different types of embedded connections and available in the literature. Three different types of thick embedded connections according to [26] are presented. Careful consideration is spent for the mechanical interaction between the beam components, including damage mechanisms initiation and propagation.
In the typical FE model, the geometrical and mechanical properties of the reference specimens are in fact properly taken into account, so to explore both the elastic and post-cracked performance of the LG beams object of study under specific loading conditions. Comparative results are then critically discussed, giving evidence of major structural performances for the selected configurations (see Figures 3-4).
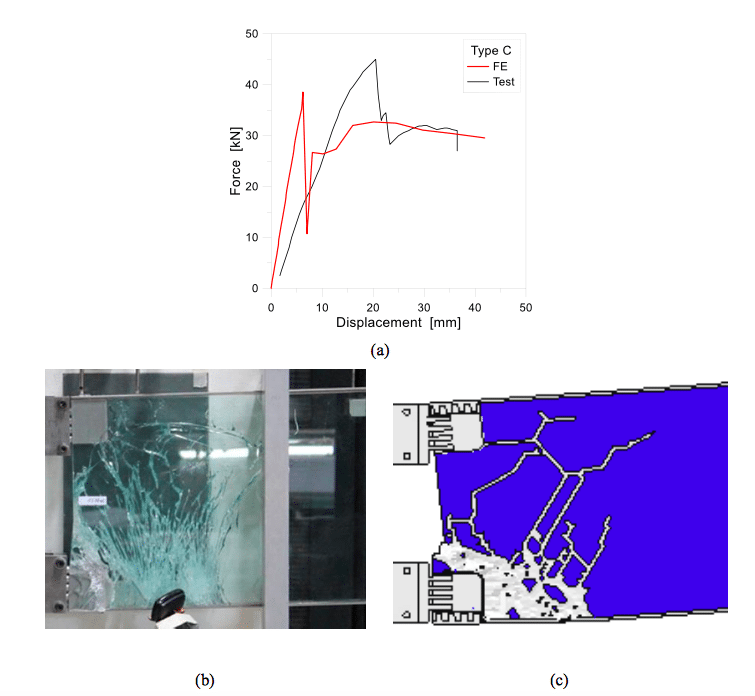
Figure 3. Experimental and numerical response of type C connections. (a) Load-displacement curves, with (b) experimental and (c) numerical crack pattern in glass at collapse (frontal view). Reproduced with permission from Elsevier, license number 4354080917915, May 2018
Given the rather close correlation between past experiments and actual FE estimations, a concise parametric study is finally reported, so to emphasize the effect of some key influencing parameters of technical interest on the bending performance of the selected configurations.
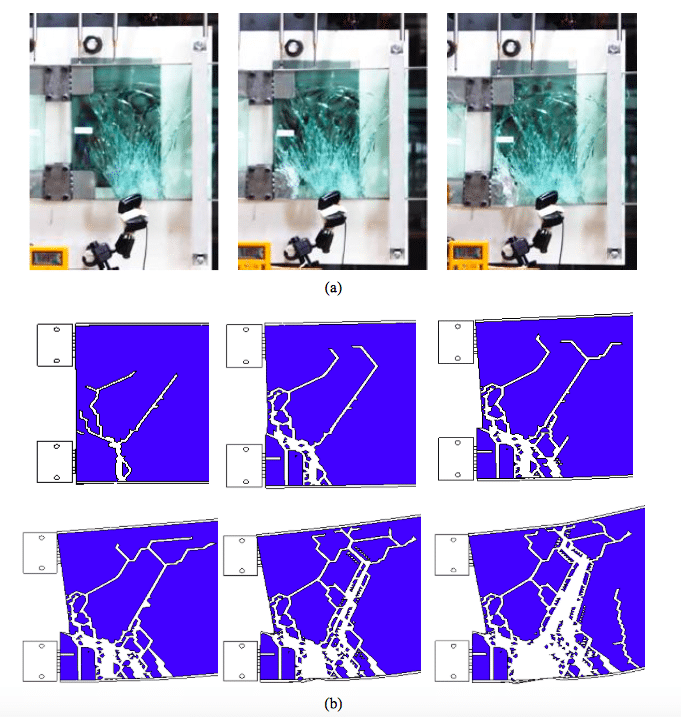
Figure 4. Type C specimen. Qualitative comparison of cracks propagation in glass, as obtained (a) experimentally and (b) numerically. Reproduced with permission from Elsevier, license number 4354080917915, May 2018
These findings are discussed in the article entitled, Laminated glass beams with thick embedded connections – Numerical analysis of full-scale specimens during cracking regime, recently published in the journal Composite Structures. This work was conducted by Chiara Bedon from the University of Trieste and Manuel Santarsiero from Eckersley O’Callaghan.
References:
- M Haldimann, A Luible, M Overend (2008). Structural use of glass. IABSE, ISBN 978-3-85748-119-2
- M Feldmann, R Kasper, B Abeln, P Cruz, J Belis, J Beyer, et al (2014). Guidance for European Structural design of glass components – support to the implementation, harmonization and further development of the Eurocodes. Report EUR 26439, Joint Research Centre–Institute for the Protection and Security of the Citizen, doi: 10.2788/5523, Pinto Dimova, Denton Feldmann (Eds.)
- M Santarsiero, C Louter, A Nussbaumer (2016). The mechanical behaviour of SentryGlas ionomer and TSSA silicon bulk materials at different temperatures and strain rates under uniaxial tensile stress state. Glas. Struct. Eng., http://dx.doi.org/10.1007/s40940-016-0018-1
- M Santarsiero, C Louter, A Nussbaumer (2016). Laminated connections for structural glass applications under shear loading at different temperatures and strain rates. Construction and Building Materials, 128: 214-237, http://dx.doi.org/10.1016/j.conbuildmat.2016.10.045
- M Santarsiero, C Louter, A Nussbaumer (2016). The mechanical behaviour of SentryGlas® ionomer and TSSA silicon bulk materials at different temperatures and strain rates under uniaxial tensile stress state. Glass Structures & Engineering, 1(2): 395-415
- J Dispersyn, S Hertelé, W De Waele, J Belis (2017). Assessment of hyper-elastic material models for the application of adhesive point-fixings between glass and metal. International Journal of Adhesion and Adhesives, 77: 102-117
- K Machalická, M Eliášová (2017). Adhesive joints in glass structures: effects of various materials in the connection, thickness of the adhesive layer, and ageing. International Journal of Adhesion and Adhesives, 72: 10-22
- D Callewaert, J Belis, D Delincé, R Van Impe (2012). Experimental stiffness characterisation of glass/ionomer laminates for structural applications. Constr Build Mater, 37: 685-692
- M Overend, C Louter (2015). The effectiveness of resin-based repairs on the inert strength recovery of glass. Constr. Build. Mater., 85: 165–174, doi: 10.1016/j.conbuildmat.2015.03.072
- C Pascual, J Montali, M Overend (2017). Adhesively-bonded GFRP-glass sandwich components for structurally efficient glazing applications. Composite Structures, 160 560-573
- JR Correia, L Valarinho, FA Branco (2011). Post-cracking strength and ductility of glass-GFRP composite beams. Composite Structures, 93(9): 2299-2309
- C Bedon, C Louter (2017). Numerical investigation on structural glass beams with GFRP-embedded rods, including effects of pre-stress. Composite Structures, 184: 650-661, https://doi.org/10.1016/j.compstruct.2017.10.027
- J Cupać, K Martens, A Nussbaumer, J Belis, C Louter (2017). Experimental investigation of multi-span post-tensioned glass beams. Glass Structures & Engineering, 2(1): 3–15
- S Jordão, M Pinho, JP Martins, A Santiago, LC Neves (2014). Behaviour of laminated glass beams reinforced with pre-stressed cables. Steel Constr., 7: 204-207, doi: 10.1002/stco.201410027
- J Belis, D Callewaert, D Delincé, R Van Impe (2009). Experimental failure investigation of a hybrid glass/steel beam. Eng Failure Anal, 16: 1163-1173
- M Kozłowski, M Dorn, E Serrano (2015). Experimental testing of load-bearing timber–glass composite shear walls and beams. Wood Material Science & Engineering, 10: 276-286
- P Cruz, J Pequeno (2008). Timber-glass composite beams: mechanical behaviour and architectural solutions. Proceedings of Challenging Glass Conference 2008, pp 439-448
- S Sitte, A Wolf (2012). TSSA-bonded point-supported structural glazing of insulating glass units at Dow Corning’s European Distribution Center. Proceedings of Engineered Transparency 2012
- J Dispersyn, M Santarsiero, J Belis, C Louter (2014). A preliminary study of the nonlinearity of adhesive point-fixings in structural glass facades J. Facade Des. Eng., 2(1–2): 85-107
- M. Netusil, M Eliášová (2010). Experimental and Numerical Analysis of Glued Steel-Glass Joints. Proceedings of Challenging Glass 2, pp 269–276
- M Overend, Q Jin, J Watson (2011). The selection and performance of adhesives for a steel–glass connection. Int. J. Adhes. Adhes., 31:(7): 587–597
- P Carvalho, PJS Cruz (2012). Connecting Through Reinforcement – Experimental Analysis of A Glass Connection Using Perforated Steel Plates. Proceedings of Challenging Glass 3
- L Blyberg, E Serrano, B Enquist, M Stereley (2012). Adhesive joints for structural timber/glass applications: Experimental testing and evaluation methods. International Journal of Adhesion and Adhesives, 35: 76-87
- M Cervio, G Muciaccia, G Rosati (2018). Tension-shear interaction domain for EVA-laminated countersunk point-fixing devices. Glass Structures & Engineering, published online, https://doi.org/10.1007/s40940-018-0056-y
- C Bedon, M Santarsiero (2018). Transparency in Structural Glass Systems Via Mechanical, Adhesive, and Laminated Connections – Existing Research and Developments. Advanced Engineering Materials, published online, 10.1002/adem.201700815
- M Santarsiero, C Louter, A Nussbaumer (2017). Laminated connections for structural glass components: a full-scale experimental study. Glass Struct Eng, 2: 79-101, doi: 10.1007/s40940-016-0033-2
- Simulia (2016). ABAQUS v.6.14 computer software and online documentation, Dassault Systems, Providence, RI, USA
- C Bedon, C Louter (2017). Numerical analysis of glass-FRP post-tensioned beams – Review and assessment. Composite Structures, 177: 129-140, doi: 10.1016/j.compstruct.2017.06.060
- C Bedon, C Louter (2017). Finite-element analysis of post-tensioned SG-laminated glass beams with mechanically anchored tendons. Glass Structures & Engineering, 1(1): 19-37, DOI10.1007/s40940-0167
- C Bedon, C Louter (2016). Finite-Element analysis of post-tensioned SG-laminated glass beams with mechanically anchored tendons. Glass Structures & Engineering, 1(1): 19-37, doi: 10.1007/s40940-0167
- C Bedon, C Louter (2014). Exploratory numerical analysis of SG-laminated reinforced glass beam experiments. Engineering Structures, 75(9): 457-468