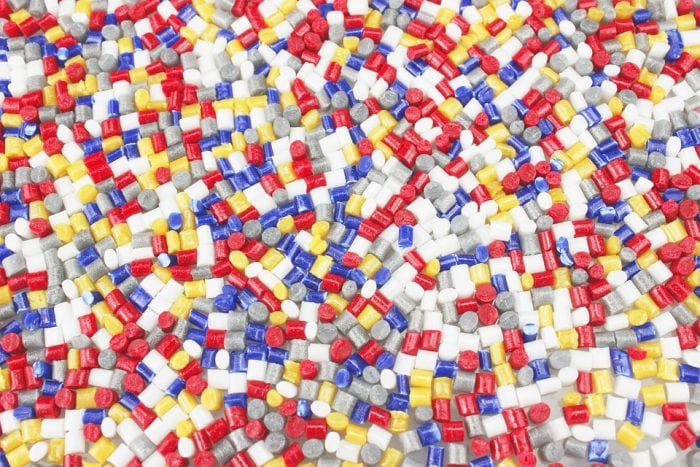
Adding nanosized and micrometer-sized particles to organic polymers instead of using pure organic polymers not only can reduce the cost of fabricated plastic products, but also improve the functionalities of plastics (tensile strength, thermal resistance, and electrical conductivity). These particulate additives in organic polymers can agglomerate and form “hydroclusters” during the fabrication processes of polymer composite products (such as injection molding or extruding) caused by interparticle interactions.
In recent times, small injection-molding and extruding machines like 3D printers have drawn much attention. These kinds of machines have short, narrow nozzles which can be easily clogged by hydroclusters of particulate additives in organic polymers, and this can cause even greater difficulties during operation of these machines. In addition, to maximize the effects of adding particular additives for improving functional properties of polymer composites, particular additives should be well dispersed.
Then, for reducing the agglomeration of additives, the surfaces of additives are generally coated with various modifiers. One of the generally-used surface modifiers for additives is stearic acid or its salts, and the coating process for this modifier is frequently based on wet chemical processes.
In a recent paper published in Polymer, researchers chose SiO2 nanoparticles and polyethylene (PE) as the base materials for the polymer composites and confirmed that polydimethylsiloxane (PDMS) coating on SiO2 can assistance the distribution of SiO2 nanoparticles in injection-molded SiO2-PE composites.
Researchers modified the surface of SiO2 nanoparticles with polydimethylsiloxane (PDMS) by simple and facile thermal vapor deposition (TVD) method without using any solvents. Moreover, the PDMS layer on the surface of SiO2 showed greater chemical stability than a stearic acid layer and good thermal stability that could endure the conditions of the injection-molding and extruding processes.
Researchers also confirmed that the PDMS coating on SiO2 can lessen the agglomeration of SiO2 in a polymer composite simultaneous exposure to shear stress and help even distribution of SiO2 in injection-molded polymer composites. The PDMS coated SiO2 (P-SiO2) + PE sample showed weakened shear-thickening behavior than that of bare SiO2 (B-SiO2) + PE sample which means P-SiO2 particles in a PE polymer were less aggregated than B-SiO2 when they were exposed to same shear stress. The P-SiO2 + PE sample also showed more even distribution of SiO2 than that of B-SiO2 + PE sample and this was verified through elemental distribution analysis of their cutting plane.
Based on these results, researchers suggest that the TVD of PDMS is a potential method for solving the dispersion problem of inorganic additives in polymer composites and this method also can help facile fabrication of composite materials using injection or extrusion processes through even dispersion of additives in the polymer.
These findings are described in the article entitled Polydimethylsiloxane thin-film coating on silica nanoparticles and its influence on the properties of SiO2–polyethylene composite materials, recently published in the journal Polymer. This work was conducted by Sang Wook Han, Il Hee Kim, and Young Dok Kim from Sungkyunkwan University, Ju Hwan Kim from Shinwoo Industry Co., Ltd, and Hyun Ook Seo from Sangmyung University.