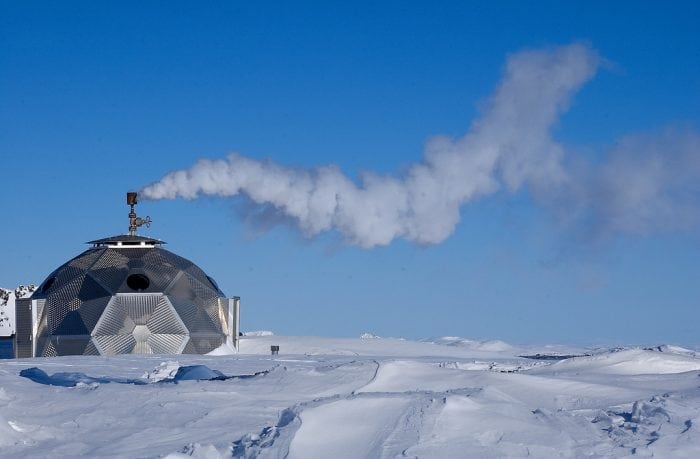
One of the ways to extract geothermal heat from the Earth’s crust is through Deep Borehole Heat Exchangers (DBHE). These can be either drilled especially for a heat extraction or, more cost-effectively, reconstructed from already-existing, negative, or abandoned oil or natural gas wells.
In many depleted boreholes, exploiting underground geothermal waters is either impossible or technically complex, therefore potential reconstruction for a borehole heat exchanger might be the only potential solution that allows for utilizing geothermal heat. Poland, a highly coal-dependent European country with declining air quality, has a considerable potential in implementing DBHE technology, mainly due to a large number of deep and abandoned petroleum wells (being drilled since mid-19th Century), which are currently located in the close vicinity to the potential heat recipients.
Borehole heat exchangers allow an exchange of geothermal heat between rock formation and heat carriers, circulating in the closed-loop system between the surface and an underground reservoir. The heat can be supplied directly, for instance from deeper wells with higher geothermal gradient, or indirectly using heat pump systems. During reconstruction operations of an already-existing well, the inner column is the most important feature, which in large part determines the overall success of the DBHE investment. Other properties include already existing well construction and characteristic of an underground rock mass.
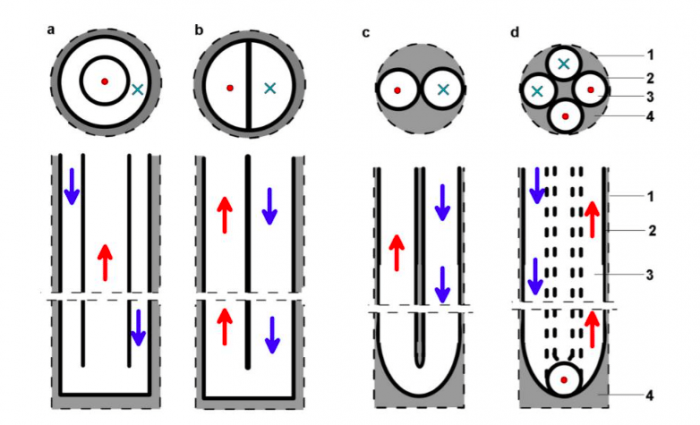
Figure 1: Potential construction designs of BHE and DBHE systems (a – coaxial heat exchanger, b – demi-type heat exchanger, c – heat exchanger with single U-pipe, d – heat exchanger with double U-pipe, 1–wall of the borehole, 2–heat exchanger pipe, 3–heat carrier, 4–sealant). Republished with permission from Elseiver from: https://doi.org/10.1016/j.geothermics.2018.04.001
The application of an insulated inner pipe with the lowest thermal conductivity coefficient will drastically reduce heat losses of a circulating heat carrier and, as a result, will increase the overall heat uptake. Well reconstruction for the DBHE includes partial abandonment, which constitutes of removing heavy mud from the borehole, sealing off perforated intervals using cement plugs and implementing inner, insulated column in leak tight, closed-loop system.
Decisive factors for inner column selection are economic efficiency, as well as its technical properties such as mechanical strength. It is crucial to properly evaluate insulation of upper parts of the well, as the temperature of circulating fluid might be cooled down significantly by the lower temperatures in the upper formation layers and decrease the efficiency of the DBHE system. Mechanical and thermal stresses will occur in an inner column during run-in operations and geothermal heat production. In static conditions, the inner column is influenced by external and internal pressures that can cause the column to collapse or burst. During the design process, elongation (or reduction) of the inner column length under its own weight has to be considered.
Vacuum Insulated Tubing (VIT), widely used in offshore industry, might be one of the potential technologies to efficiency extract geothermal heat from the DBHE installations, with other solutions being single one-layered steel coaxial inner column, double steel coaxial inner column with insulation fluid, coaxial inner column with thermal insulation layer, coaxial inner column made from polymer materials, coaxial inner column made from polymer materials with greater wall thickness, and coaxial inner column made from double polymer pipe. VIT constitutes of two coaxial steel pipes, where air between them is evacuated using a vacuum pump during the manufacturing process.
After achieving the desired level of vacuum, pipes are sealed and welded. This process creates very high thermal insulation and minimizes heat exchange between the vacuum pipe and annulus. VIT technology decreases heat transfer between the inner coaxial column and existing well construction. Such insulated tubes are implemented in order to eliminate high heat exchange caused by convection, radiation, and conduction. These features can lengthen the life expectancy of the DBHE systems, increase efficiency and decrease costs without having any negative impact on the environment. VIT demonstrate thermal conductivity coefficient varied from 0.006 to 0.0008 W/(m·K), whereas for conventional steel pipes this value amounts to 40 W/(m·K).
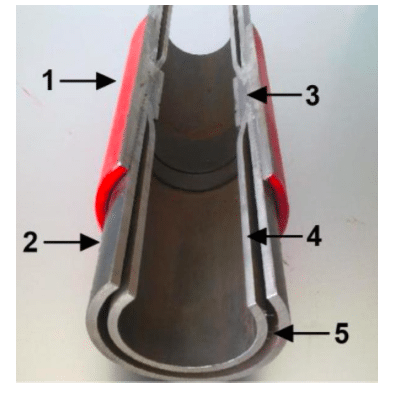
Figure 2: Components of Vacuum Insulating Tubing (1–coupling, 2–outer steel pipe, 3–internal coupling insulator and weld, 4–inner steel pipe, 5–vacuum with getter material) (adapted from Helix Oilfield Services Ltd., 2017). Republished with permission from Elseiver from: https://doi.org/10.1016/j.geothermics.2018.04.001
Conventional in the petroleum industry, L-80 steel grade is most commonly used for an outer VIT pipe, whereas steel grades with higher chrome content are applied for inner pipe due to potentially hostile and corrosive downhole environment. The main drawback of VIT is the significantly high weight of double steel pipes, which leads to increased costs of transport and operations of running into the borehole with a drilling rig onsite. Other disadvantages include high market price and limited availability.
These findings are described in the article entitled Potential application of vacuum insulated tubing for deep borehole heat exchangers, recently published in the journal Geothermics. This work was conducted by Tomasz Sliwa and Aneta Sapinska-Sliwa from AGH University of Science and Technology, Michal Kruszewski from AGH University of Science and Technology and the International Geothermal Centre Bochum, and Alireza Zare and Mohsen Assadi from the University of Stavanger.