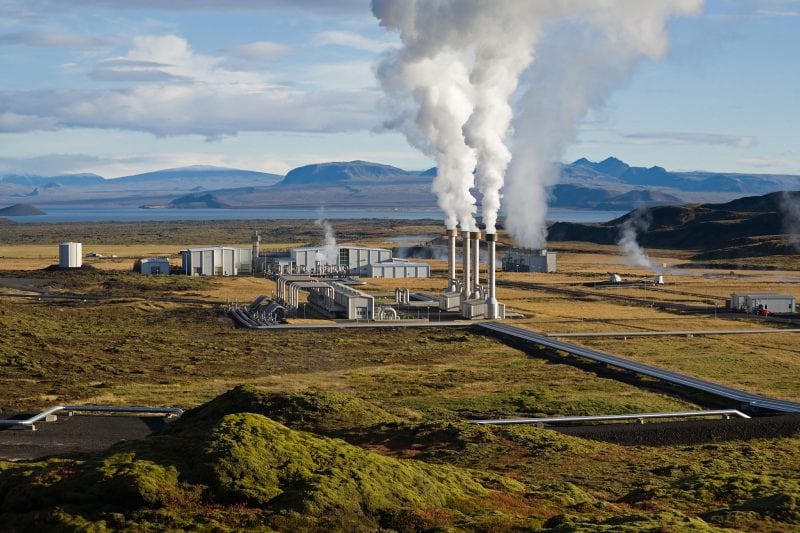
Utilization of medium- to low-temperature (<350°C) thermal energy, such as geothermal energy, solar thermal energy, and waste heat, is an important approach to promoting energy conservation and reducing environmental pollution.
The Organic Rankine Cycle (ORC) is an important and promising heat-power conversion technology for medium- to low-temperature heat sources. It has the advantages of a widely applicable heat source temperature range, simplicity, stability, flexibility, safety, and widely installed capacity range, compared to other heat-power conversion technologies utilizing the medium- to low-temperature thermal energy. The application of ORC systems is continuously expanding around the world, as shown in Fig. 1.
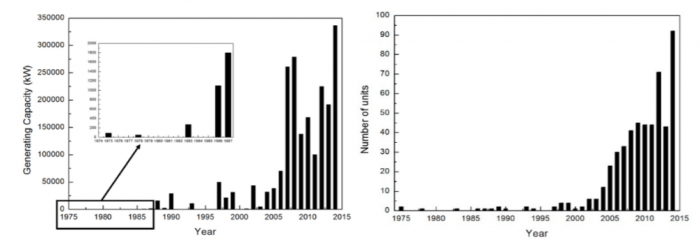
Fig. 1 Developments for added generating capacity and number of ORC systems around the world (Republished with permission from Elsevier)
In an ORC system, the working fluid is an important carrier for achieving the power generation from heat sources, and it crucially affects the system performance. The zeotropic mixture consists of two or more pure fluids, and it can significantly increase the selectable range of working fluids for ORC systems. Moreover, the zeotropic mixture has a varying phase-change temperature which is beneficial to reduce the exergy loss in the heat transfer processes, and thereby considerably increasing the heat–power conversion efficiency for ORC systems, compared to pure fluids. Using zeotropic mixtures in ORC systems has been a new trend in recent years.
However, compared to using a pure fluid, ORC systems using a zeotropic mixture generally need a larger heat transfer area, especially a larger condenser heat transfer area; mainly due to the decreases of heat transfer temperature difference and condensation heat transfer coefficient. The purchased cost of the condenser increases as the heat transfer area increases, and studies have shown that the condenser purchase cost can account for more than 35.8% of the total purchased equipment costs for an ORC system.
In addition, factory building area and system maintenance costs also increase as the condenser heat transfer area increases. The large condenser heat transfer area has been one of the crucial factors that impedes the broad application of ORC systems using zeotropic mixtures. Increasing the condensation heat transfer coefficient is an effective approach to reducing the condenser heat transfer area. However, conventional enhanced heat transfer methods generally increase the pressure drop during condensation, thereby degrading the thermodynamic performance of ORC system.
Liquid-separated condensation is an emerging enhanced heat transfer method that separates the condensed fluid from the vapor-liquid mixture during condensation. It reduces the condensing film thickness on the cooling surface and increases the vapor quality. The key idea is to use the excellent heat transfer characteristics of high-quality vapor to increase the condensation heat transfer coefficient, as shown in Fig. 2. Separating the condensed fluid also reduces the flow resistance during condensation. Therefore, liquid-separated condensation can simultaneously increase the condensation heat transfer coefficient and reduce the pressure drop.
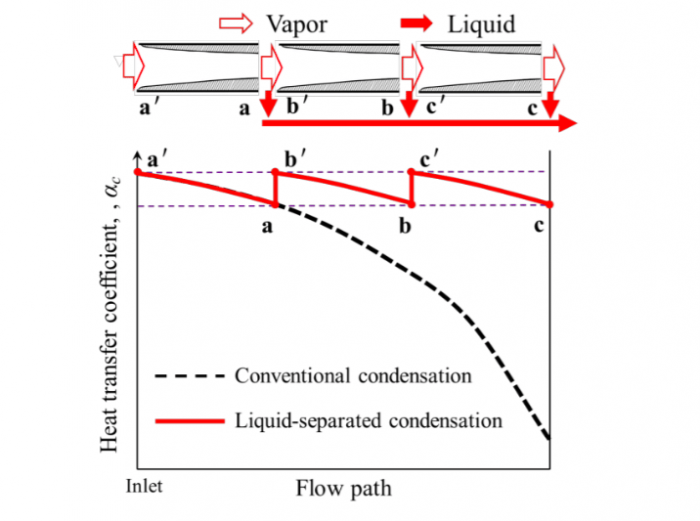
Fig. 2 Schematic for the liquid-separated condensation that enhances the condensation heat transfer (Vapor–liquid separation occurs twice) (Republished with permission from Elsevier)
However, unlike pure fluids, the composition of a zeotropic mixture will change after the liquid is separated from the vapor-liquid two phase flow in the liquid-separated unit, and characteristics of mixture condensation temperature are also different for various vapor qualities at the liquid-separated unit inlet (xLSI, which reflects the liquid-separated unit relative location in the condenser), as shown in Fig. 3. Therefore, for ORC system using zeotropic mixtures with liquid-separated condensation, effects of vapor quality at the liquid-separated unit inlet on the net power output, condensation heat transfer coefficient, and heat transfer area become important issues need to be studied.
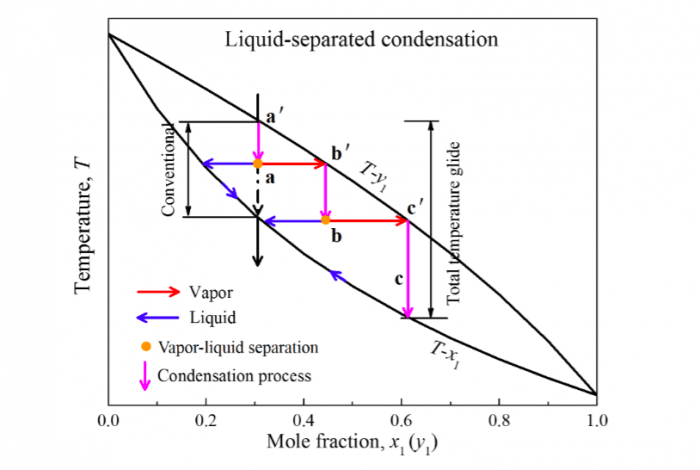
Fig. 3 Liquid-separated condensation changes the composition and condensation temperature characteristics of a zeotropic mixture (Republished with permission from Elsevier)
In this work, the liquid-separated condensation method was the first introduced into an ORC system using zeotropic mixtures (R600/R601a mixtures). The potential of liquid-separated condensation in reducing the heat transfer area was assessed, compared to the conventional condensation without liquid-separation. Effects of vapor quality at the liquid-separated unit inlet on the net power output, condensation heat transfer coefficient, and heat transfer area were studied. Characteristics of the ORC system using zeotropic mixtures with liquid-separation condensation were also revealed.
A condenser with single-stage vapor–liquid separation in the working fluid flow path is defined as “single-stage liquid-separated condensation.” Fig. 4 shows the schematic of a condenser with single-stage vapor-liquid separation. The liquid-separated unit can be set at different locations along the condensation flow path in the condenser, representing the vapor-liquid separation occurs at different thermodynamic states during condensation. The liquid-separated unit is closer to the condenser outlet, and the xLSI is lower. The working fluid is cooled to the vapor-liquid two-phase in the first flow path (6-7 process).
The vapor and liquid are separated in the liquid-separated unit due to the difference in their densities (7-7″/1′ process). The separated vapor enters the second flow path (7″-1″ process) and continues to be cooled into liquid by the cooling water. The separated liquid (1′) flows to the condenser outlet through additional tubes. Two liquids (1′ and 1″) mix at the condenser outlet, leave the condenser, and then enter the feed pump. The working fluid mass flow rate decreases after the vapor-liquid separation. Therefore, the heat exchange tube number of the second flow path should be reduced to guarantee the working fluid inlet velocity. Several multi-hole metal laminates are placed in the liquid-separated unit. The separated liquid flows into additional tubes through the holes on the metal laminates whereas the vapor is prevented by the liquid seals on the metal laminate surfaces.
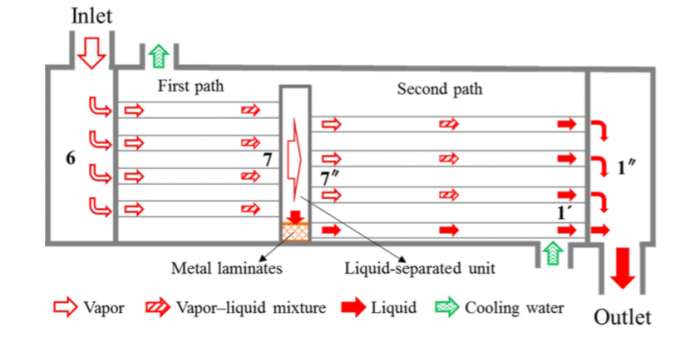
Fig. 4 Schematic of a condenser with single-stage vapor-liquid separation (Republished with permission from Elsevier)
Schematics of the ORC system using zeotropic mixtures with liquid-separation condensation and its thermodynamic processes are shown in Figs. 5 and 6, respectively. The mass flow rate of cooling water remains constant. The cooling water temperature rise of the first flow path is Tcool,pp–Tcool,p, and that of the second flow path is Tcool,p–Tcool,in.
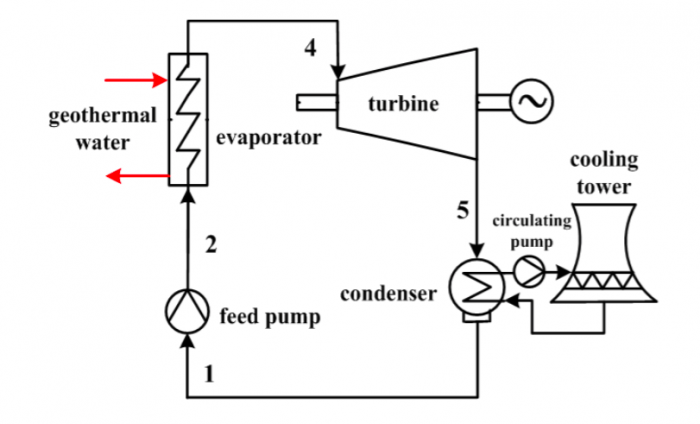
Fig. 5 Schematic of a geothermal ORC with a wet cooling system (Republished with permission from Elsevier)
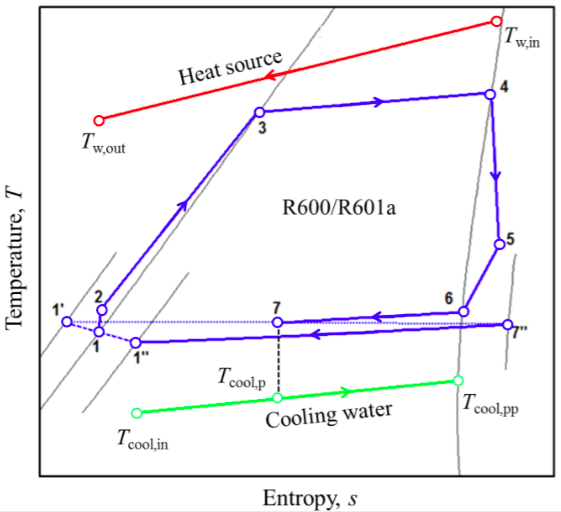
Fig. 6 Temperature-entropy diagram of an ORC system using the R600/R601a mixture with single-stage liquid-separated condensation (Republished with permission from Elsevier)
Results show that the liquid-separated condensation may reduce the maximized net power output of an ORC system using zeotropic mixtures. Moreover, the maximized net power output may decrease as the xLSI decreases for zeotropic mixtures, as shown in Fig. 7. The decrease of maximized net power output is strongly related to the increase of condensation pressure which is caused by the increase of the total condensation temperature glide, as shown in Fig. 3.
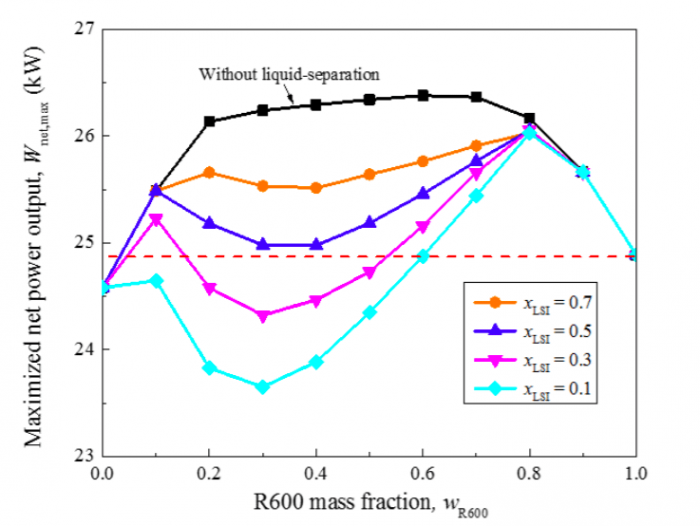
Fig. 7 Maximized net power outputs for various R600 mass fractions (Republished with permission from Elsevier)
The liquid-separated condensation can increase the average condensation heat transfer coefficient by 23.8% for R600/R601a mixtures, compared to the conventional condensation. The xLSI which obtains the maximum average condensation heat transfer coefficient is determined by the heat transfer coefficient profile in the condenser, and that is lower than 0.3 for the R600/R601a mixture, as shown in Fig. 8.
The xLSI has a crucial effect on the condenser heat transfer area, because it affects not only the average condensation heat transfer coefficient but also the integral mean temperature difference. Results show that the liquid-separated condensation can reduce the condenser heat transfer area by 44.1% for R600/R601a mixtures compared with the conventional condensation, as shown in Fig. 9. In addition, when the maximized net power output remains constant, the condenser heat transfer area can be reduced by 11.6% for R600/R601a mixtures with liquid-separation condensation.
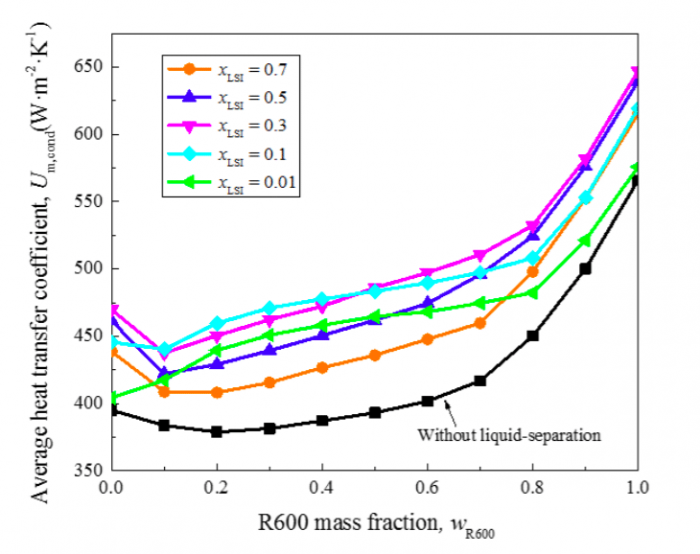
Fig. 8 Average condensation heat transfer coefficients at the optimal operation conditions for various R600 mass fractions (Republished with permission from Elsevier)
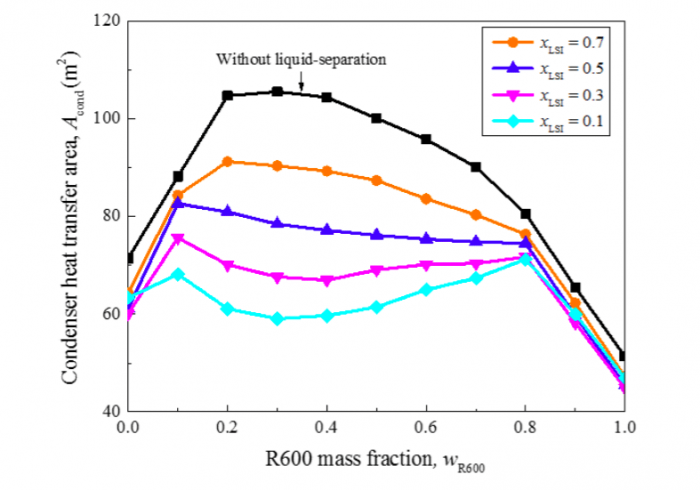
Fig. 9 Condenser heat transfer areas at the optimal operation conditions for various R600 mass fractions (Republished with permission from Elsevier)
This work also indicates that the thermo-economic method is more suitable to analyze the performance for ORC systems using zeotropic mixtures with liquid-separation condensation because the liquid-separated condensation can significantly reduce the condenser heat transfer area while it may also reduce the maximized net power output for ORC systems using zeotropic mixtures.
Therefore, a thermo-economic analysis was carried out. Results show that the single-stage liquid-separated condensation can reduce the electricity generation cost by 1.3%-2.6% compared with the conventional condensation for R600/R601a mixtures, as shown in Fig. 10. The lowest electricity generation cost occurs at the R600 mass fraction of 0.9 with xLSI = 0.3, and the electricity generation cost is reduced by 1.7% compared to R600 with the conventional condensation, and 6.9% compared to R601a with the conventional condensation.
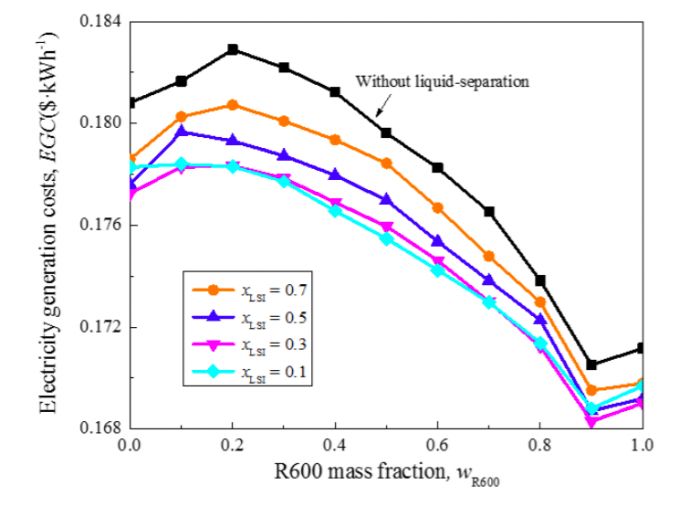
Fig. 10 Electricity generation costs (EGC) at the optimal operation conditions for various R600 mass fractions (Republished with permission from Elsevier)
These findings are described in the article entitled Performance analysis of organic Rankine cycles using R600/R601a mixtures with liquid-separated condensation, recently published in the journal Applied Energy. This work was conducted by Jian Li, Yuanyuan Duan, and Zhen Yang from Tsinghua University, and Qiang Liu from China University of Petroleum.