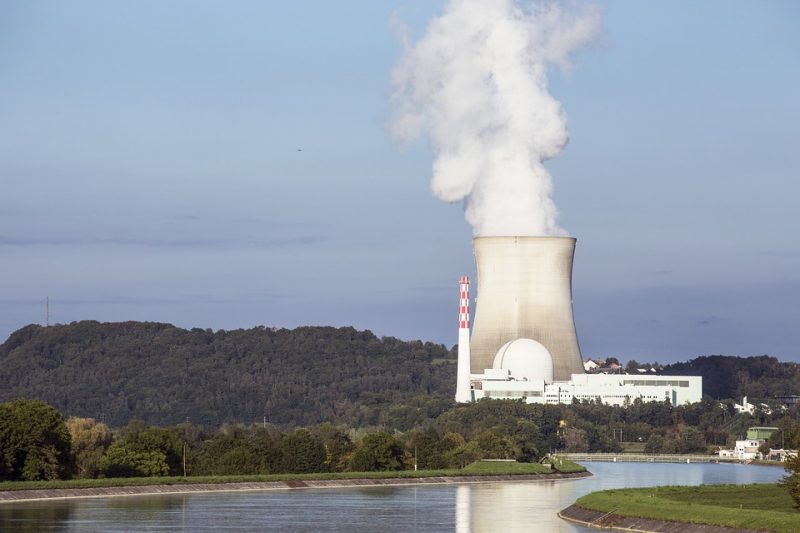
Bring a couple system such as brass, a copper-zinc alloy, in contact with a liquid metal — say, mercury. Mechanically stretch brass with a tensile machine past its yield point (the stress at which the alloy irreversibly plastically yield), and a brittle crack will suddenly initiate and propagate at a fast speed of the order of ten centimeters per second. This rupture, triggered by the liquid metal, occurs in an otherwise ductile alloy.
Such process, which can lead to catastrophic fracture well below usual engineering safety loads in several couples like brass/mercury, is called liquid metal embrittlement (LME). First reported in 1914, LME is still the subject of active research to understand its small-scale mechanisms. In spite of decades of investigations, the prediction of its occurrence still escapes our reach. The number of LME cases keeps increasing with time, as many couples have still not been properly investigated.
The nuclear power community faces the challenge of better understanding this phenomenon as future reactors, so-called fourth-generation reactors for sustainable nuclear energy, plan to use low melting point liquid metals such as sodium or lead-bismuth alloy as a coolant for the reactor core. The concentrated solar energy field is concerned as well, as sodium is a serious candidate as a heat transfer medium. In these systems, the materials to be used, mostly steels, must resist irradiation (when applicable), corrosion, and LME all at once. It is, therefore, important to gain as much knowledge as possible on the effect of LME on the materials planned to be used in these future reactors in order to prevent detrimental effects by material selection, optimization, or by a safe design.
Most of the knowledge on LME comes from the study of specific systems like elemental materials (iron, aluminum, copper, nickel, zinc, titanium, etc) in contact with easy-to-handle liquid metals (mercury, gallium, lead, bismuth, or tin, for example). The materials we are interested in today for practical applications are more alloyed, more corrosion resistant, and often optimized materials relative to high-temperature mechanical resistance or irradiation resistance. This requires one to study experimentally difficult systems like stainless austenitic steels — a material also used in pressure cookers — in contact with the highly chemically reactive liquid sodium.
How they behave in relation to LME, however, is often a question that has not been fully addressed in the past. Several research items with the structural materials planned for future nuclear reactor are to be conducted. First, detailed investigations of the LME sensitivity have been carried out by studying the proper condition for a potential occurrence of LME (the subject of the article Investigation of crack propagation resistance of 304L, 316L and 316L(N) austenitic steels in liquid sodium). Second, one needs to understand the LME mechanisms at work using detailed microstructural investigation method such as electron microscopy down to nano-scale resolution (work reported in references therein for the 304L steel in contact with sodium). This is aimed at bringing crucial experimental insights that will potentially feed the theoretical understanding of LME in complex cases and help at deciphering metallurgical strategies to mitigate it.
What has been found out up to now is that several austenitic steels, thought to be immune to LME, are indeed susceptible to that environmental effect. These cases were hidden due to the complex thermodynamics of the interface in contact with a reactive liquid metal. In the case of sodium, for example, traces of oxygen completely change the interfacial phases that will be formed and it affects wettability. The key experimental factor for an LME-induced crack to develop under a mechanical loading is to have a good wetting by the liquid metal. Most metallic elements oxidize in an oxygen-containing atmosphere, gold and platinum being the exceptions. This leads to the formation of a native oxide scale that protects the metal from being wetted by most liquid metals. So in order to reveal whether or not there is LME, it is usually required to etch the oxide layer either mechanically or by electrochemically dissolving that barrier.
What was found out is that another path would work as well, that is to rely on reactive wetting. The phase formation at the interface can be oriented towards the formation of complex oxides, often ternary or quaternary compounds, will promote good wettability by the liquid metal. In the case of austenitic steels, the crucial addition of sodium oxide to the liquid allowed to build a layer of sodium chromite, an oxide that is totally wet by liquid metallic sodium. This was demonstrated in a prior work on the 304L steel (the 18-8 steel of our pressure cooker). By extension, it should also be true for any stainless austenitic steels provided the right interface is formed in-situ by adding a small amount of oxygen to sodium.
Indeed, this turned out to be a sufficient condition to observe LME with three of the austenitic steels commonly envisioned for this environment. This is essentially what was demonstrated in the work reported in the article. The small-scale understanding of the key role of wettability is that during plastic deformation in tensile loading, any location at the surface that will expose a material’s interface (a prior grain boundary or a twin interface formed during deformation for example) to the liquid metal will provide the right conditions for the liquid metal penetration.
These findings required the development of a complex test apparatus (glove boxes both for pre-exposure and for mechanical testing) with highly efficient in-situ oxygen or water removal techniques for the manipulation of sodium. Ironically, the addition of oxygen in sodium has to be carried out later on, but it is viewed as a trick to reproducibly trigger an LME crack. Nevertheless, such a condition is far from the running condition of sodium loops in practical applications. It is also to be noted that these LME cases with austenitic steels are, in terms of mechanical resistance reduction, far from the catastrophic cases of the above mentioned LME model systems. The crack speed is many orders of magnitude lower while requiring a constantly increasing loading, a condition difficult to meet in practice.
The question of susceptibility of these steels to LME is now settled, but there remains to bring a microstructural understanding to these results in terms of microstructural crack path. The fracture surfaces of the steels in the brittle area all look alike indicating that a common mechanism leads to premature fracture. It could be shown in one case that it is linked to the steel’s trend to bear phase transform as well as a follow-up consequence of a special plastic dissipation mechanism known as mechanical twinning. It creates interfaces in the material that are later on embrittled by sodium. This scenario remains to be confirmed for all cases.
These findings are described in the article entitled Investigation of crack propagation resistance of 304L, 316L and 316L(N) austenitic steels in liquid sodium, recently published in the Journal of Nuclear Materials. This work was conducted by B. Barkia, J.L. Courouau, E. Perrin, V. Lorentz, M. Rivollier, R. Robin, L. Nicolas, C. Cabet, and T. Auger from the Université Paris-Saclay and CNRS.