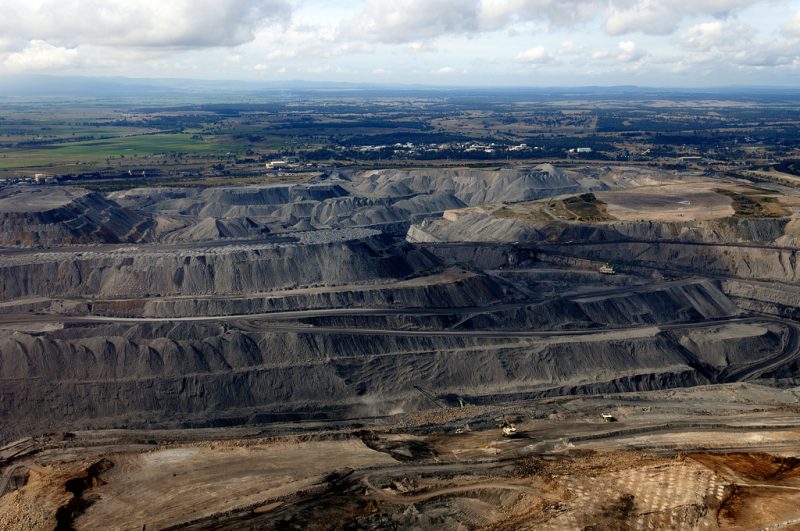
Coal dust pneumoconiosis is the number one killer of coal miners in China. According to the National Occupational Disease Report released by the National Health and Family Planning Commission of the People’s Republic of China, there were 864,825 cases of pneumoconiosis reported in China at the end of 2017, of which over 50% were in mines. There were 26,756 new pneumoconiosis cases reported in China in 2017, of which 51.5% were in miners. Each year, approximately 1,900 pneumoconiosis patients die in China, a number 3-5 times greater than the death toll caused by accidents in Chinese mines.
In order to reduce exposure to coal dust, international researchers generally recommend ventilation, spraying, and chemical methods for coal dust suppression, as well as the use of an air curtain for dust isolation. Spraying techniques for dust suppression are now widely used in mines; in particular, the external spraying technique is used in more than 80% of heading machines. The main factors that affect the dust suppressing performance of the spraying technique are the atomization characteristics of nozzles, specifically the nozzle type and spraying pressure.
This study focused on the 3lower 610 fully-mechanized excavation face in the Jiangzhuang coal mine, which is owned by Shangdong Energy Zaozhuang Mining Group Co., Ltd. If no dust prevention measures were taken, the mass concentration of dust in the head-on region was as high as 1600 mg/m3. Under single-forced ventilation conditions, these high concentrations of dust diffused 300 m along the tunnel, which not only greatly affected the visibility in the operating space, but also posed a significant threat to workers’ physical health.
In this study, a three-phase coupling model was constructed to describe the interactions between droplets, dust, and airflows, the crushing of liquid jet flows and their collision with each other, and the capture of dust by droplets. The dust suppression efficiencies of different nozzles were measured using an experimental system, and the results were used to validate the accuracy of the coupling model.
Simulations were performed to explore the diffusion trajectories of dust particles around the cutting head, the related polluted area, and the arrangement of nozzles that exhibited annular symmetrical distribution around the cutting head. In addition, the distribution patterns of dust concentrations, and the variation in the cumulative mass of dust along the heading direction, following the implementation of spraying schemes, were analyzed. Finally, the relationship between spraying pressure and dust suppression efficiency was clarified, and variations in dust particle size when the optimal spraying scheme was used were discussed.
The results showed that at spraying pressures of between 2 to 8 MPa, as spraying pressure increased, so too did dust suppression efficiency, but the efficiency increased more slowly as it neared 8 MPa. The most favorable dust suppression was achieved using K2.0 nozzles (K2.0 represent the X-shape flared-head nozzles with a diversion core, whose hole diameter was 2.0 mm) at a spraying pressure of 8 MPa, with dust clusters in which the dust concentration exceeded 110 mg/m3 in the fully-mechanized excavation face significantly reduced. The dust suppression efficiency was as high as 86.1%, with the proportion of respirable dust with a diameter smaller than 7 μm seen to increase gradually from 16% to 27%, suggesting that the threat of a high concentration of dust particles in the fully-mechanized face can be alleviated to a certain degree.
These findings are described in the article entitled An Investigation of the Nozzle’s Atomization Dust Suppression Rules in a Fully-mechanized Excavation Face Based on the Airflow-Droplet-Dust Three-Phase Coupling Model, recently published in the journal Advanced Powder Technology. This work was conducted by Haiming Yu, Weimin Cheng, and colleagues from the Shandong University of Science and Technology.