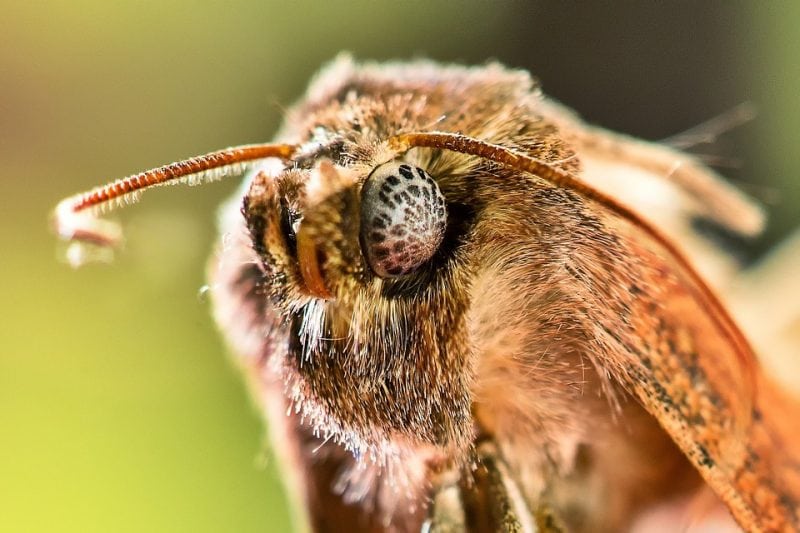
Nature has long inspired scientists around the world to engineer the materials of particular functional properties, such as anti-icing, non-wetting surfaces, self- assembly, healing abilities, or harnessing solar energy. Many naturally occurring systems exist that are able to precisely manipulate the interaction of light with matter.
The structures such as photonic crystals or opals are the inherent parts of peacock feathers, butterfly wings, and insect elytron. Thanks to fast progress in microscopy techniques, it is possible to peep into nature and mimic the structures with desired properties via advanced engineering methods.
The eye of the moth is a perfect example of an anti-reflective (AR) system, which is used by the insect to see in the dark, while also preventing light from reflecting off their eyes and possibly alerting predators. The eyes of moths are covered with sub-wavelength, light-trapping structures (Fig. 1a). In the sub-wavelength structures, the effective suppression of the reflection is implemented via tapered index design, where the ordered array of tapered pillars acts as a layer for the gradually changing refractive indexes (Fig. 1b). The AR structures are insensitive to the polarization of light and the angle of incidence. Furthermore, the suppression of light reflection occurs for a broad range of wavelengths.
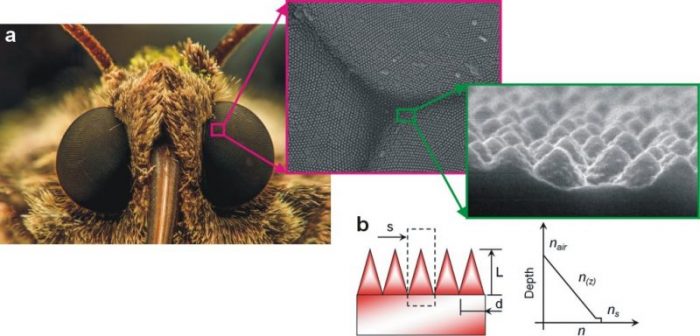
Fig. 1. Moth-eye structure (a); Schematic diagram of antireflective layer with gradually changed refractive index (n), L and d denote the length and diameter of the individual nanostructures; n(z) represents refraction index as a function of depth, nair and ns represents the refractive index of air and a material, respectively (b) (Y. F. Huang, S. Chattopadhyay, J. Nanophotonics, 7, 2013, 073594). Image of moth from freeimages.com
The widespread production of the AR coatings is of utmost importance for solar cells, light emitting diodes, and many widely-used optical instruments. For many aerospace and military applications, including night vision devices, camouflage, active and passive imaging sensors, detectors, or laser communication systems, AR coatings operating in infrared (IR) regions are of great interest. Usually, time-consuming, complicated, and expensive techniques are employed in order to imitate the moth-eye structure, such as electron-beam lithography, photolithography, or reactive ion etching. Electrochemical methods are relatively less complicated, more affordable, and suitable for large-scale production.
Electrochemical oxidation (anodization) of aluminum has been widely used to obtain protective and decorative layers on its surface. Based on a two-step replicating process within narrow regions of processing conditions, a self-ordered porous anodic alumina (PAA) membrane with hexagonally arranged, parallel pores can be formed (Fig. 2). The geometrical parameters of PAA, such as pore diameter (Dp) and the interpore distance (Dc), are easily controlled by the operating conditions during the synthesis imposed by an applied voltage, type of electrolyte, or temperature. Nowadays, PAA is one of the most prominent template materials for design and synthesis of high-density arrays of nanostructures (nanowires or nanotubes) with monodisperse controllable diameter. Moreover, it can be employed as 1-D or 2-D photonic crystals.
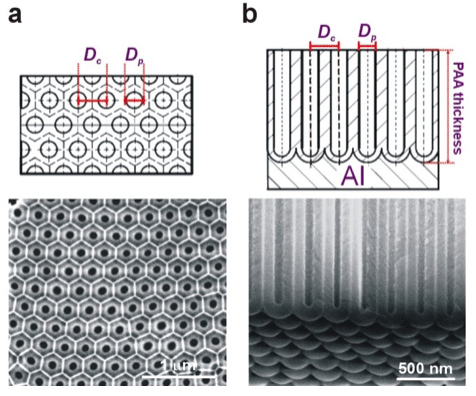
Fig. 2 The scheme and the SEM micrographs of porous anodic alumina (PAA): upper view (a) and a cross-sectional view (b). Republished from open access Springer paper: https://doi.org/10.1007/s10934-017-0419-9
The two-step anodization method can be also used for a production of PAA with tapered pore structure mimicking the moth-eye structure. The engineering of the tapered pores relies on the application of alternating anodization and pore broadening steps (Fig. 3). In our work, the anodization was performed in citric acid solution at relatively high voltages (210, 230, and 250 V), and the pore broadening was done in phosphoric acid solution.
In order to achieve highly-ordered pores (hexagonal close-packed structure), the procedure was preceded by a so-called hard anodization of aluminum (conducted under high current density) in etidronic acid. The advantage of hard anodization is a fast production of highly ordered pore structure. However, owing to a strong fluctuation of voltage and current applied at the begging of the process, the upper part of the resulted PAA was highly disordered.
To avoid this problem, the PAA membrane produced in this process is chemically dissolved in a mixture of chromic and phosphoric acids, and the close-packed hexagonal structure of concaves remaining on the aluminum substrate is used in the anodization conducted under mild conditions (under low current density). In this approach, the concaves serve as nucleation sides for the growth of regular arrays of pores, parallel throughout the whole PAA membrane thickness. The overall electrochemical synthesis resulted in fabrication of the PAA with tapered pores (conical shape) and Dc of 550, 590, and 650 nm (Fig. 4). The moth-eye structure can be employed as a template for a production of AR coatings operating in a broad spectral range expanding from visible to IR region.
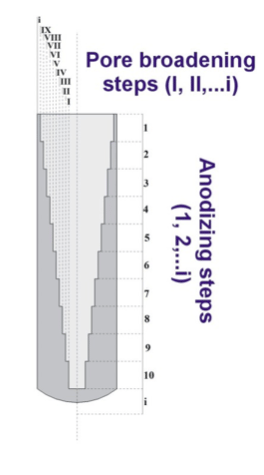
Fig. 3 The scheme representing a multi-step anodization and pore broadening process applied for the fabrication of a tapered pore. The Arabic numerals: 1, 2, 3,…i signify the number of anodization steps, whereas the Roman numerals: I, II, III,…i indicate the number of etching steps. Republished from open access Springer paper: https://doi.org/10.1007/s10934-017-0419-9
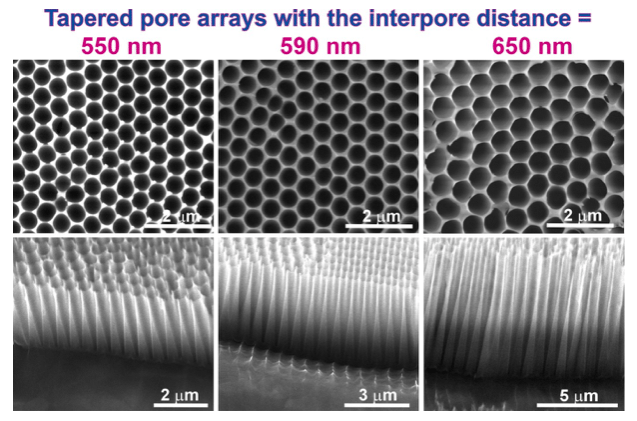
Fig. 4 SEM images of the PAA membranes with tapered pore structure: the top view (upper row) and a cross-sectional view (bottom row). Republished from open access Springer paper: https://doi.org/10.1007/s10934-017-0419-9
These findings are described in the articles entitled “Morphological and chemical characterization of highly ordered conical-pore anodic alumina prepared by multistep citric acid anodizing and chemical etching process,” published in the Journal of Porous Materials, and “Manufacturing of highly ordered porous anodic alumina with conical pore shape and tunable interpore distance in the range of 550 nm to 650 nm,” published in Materials Science – Poland. This work was led by Małgorzata Norek from the Military University of Technology.