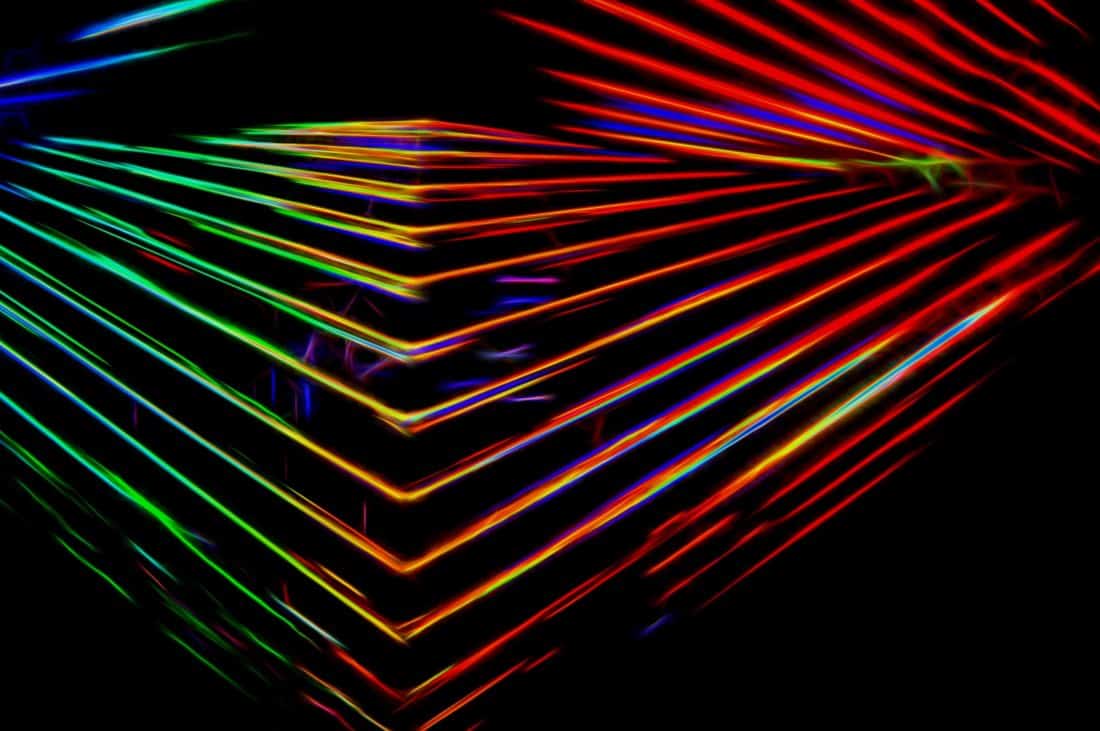
Lightweight structures have been in high demand in the automotive and aerospace industries in recent years, aiming to improve fuel efficiency and reduce gas emissions for vehicles and to increase load-bearing capacity for aircraft. The joining of dissimilar metal has been considered one of the most effective measures to meet such requirements.
As the lightest alloy with the prominent properties of recyclability, high specific strength, and low density, magnesium is an ideal candidate in automotive manufacturing. As a widely-used material, titanium also boasts some excellent properties, such as high strength and high heat resistance. Consequently, a reliable joining of Mg and Ti for the fabrication of hybrid lightweight structural components is very promising, which will, in turn, expand the application range of both materials.
Although a reliable joining of magnesium and titanium is of great significance in the advanced structural and engineering industry, it faces great challenges. The physical properties of Mg and Ti, such as melting point, heat conductivity, and coefficient of linear expansion, are totally different. The Mg-Ti system is substantially immiscible, and thus, no metallurgical reaction occurs.
To weld dissimilar metals like Mg and Ti, adding an intermediate element which can react with both materials is very helpful. Traditional methods are mainly divided into two options: utilize the effective alloying elements in base metals or filler metals immediately and add interlayers which contain the expected elements. On this foundation, researchers have adopted Al, Cu, and Ni to produce transition layers to metallurgically bond Mg and Ti via various welding techniques such as friction stir welding, cold metal transfer welding, transient liquid phase bonding, tungsten inert gas welding, and laser welding.
A burgeoning technique, laser welding-brazing has great advantages in joining dissimilar metals, which means a fusion welding occurs for the low-melting-point metals and a brazing takes place for the high-melting-point metals. Thus, it is particularly adaptable and flexible for joining materials with a big difference in melting points. Recently, we adopted this laser welding-brazing technique (see Fig.1) to join Mg and Ti in a butt joint for the first time, with the assistant of Al and Ni elements. An AZ92 filler metal was adopted to provide Al as an intermediate element, whereas the Ni element was supplied by electroplating it on the Ti substrate instead of an interlayer. A thermodynamic calculation was newly-developed to interpret the elemental diffusion mechanism and driving forces of formation phases at the Mg/Ti interface, which further lay the foundation for the bonding mechanism.
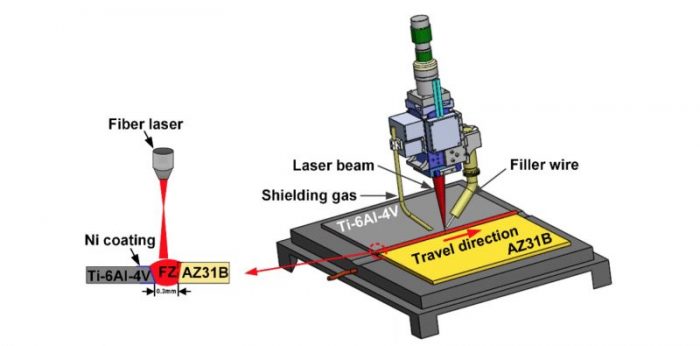
Fig.1 Schematic of laser welding-brazing process to join AZ31B-Mg and Ti-6Al-4V in a butt configuration. Credit: Xiaoye Zhao
The welding-spreading ability of the filler wire on Ti substrate was significantly improved when using a Ni coating, regardless of the laser power. As for the joints with a Ni coating, the interfacial microstructure varied greatly with increasing laser power, from an ultra-thin Ti3Al layer, to a mingled structure of Ti2Ni and Ti3Al, and to a Ti3Al layer again which was accompanied by Ti2Ni phases on the Ti substrate. The mingled microstructure (Ti3Al+Ti2Ni) was identified by the transmission electron microscopy (TEM) (see Fig.2).
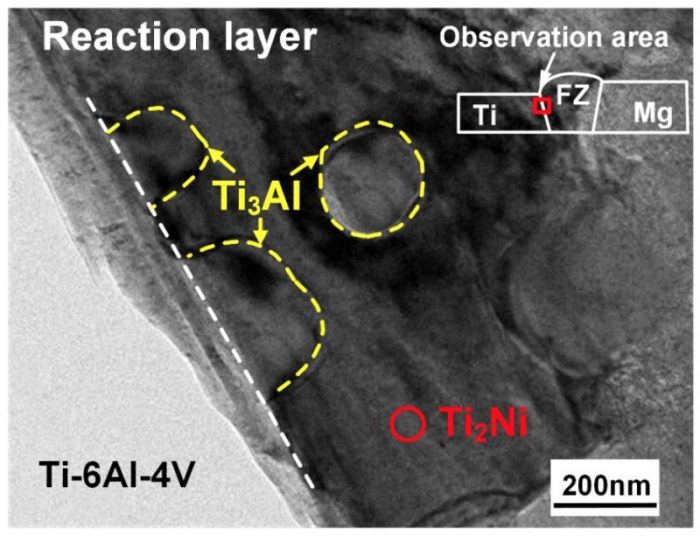
Fig.2 TEM investigation of the fusion zone/Ti interface of Mg/Ni-coated Ti joint at a laser power of 1500 W. Credit: Xiaoye Zhao
A Miedema theoretical model was employed for thermodynamic calculation, based on which a Toop model applied to the ternary system, and an extended Toop model suitable for the quaternary system were also developed. The results evaluated not only the respective role of Al and Ni in joining Mg and Ti, but also the interactions between them. An enthalpy comparison between Mg-Al-Ti and Mg-Ni-Ti ternary systems indicated that Al and Ni shows very similar promoting effects on the immiscible Mg-Ti system. But further calculation and analyzation of Mg-Ni-Al-Ti quaternary system revealed that the heat input can influence the interaction mechanism of Al and Ni on Mg/Ti joint. At low laser powers, the driving force of Al diffusing to Ti substrate was higher than that of Ni (see Fig.3). While at a high laser power, the driving force of Ni to Ti was much higher. This interaction mechanism of Al and Ni varying with laser power brings about the diversity in the interfacial microstructure.
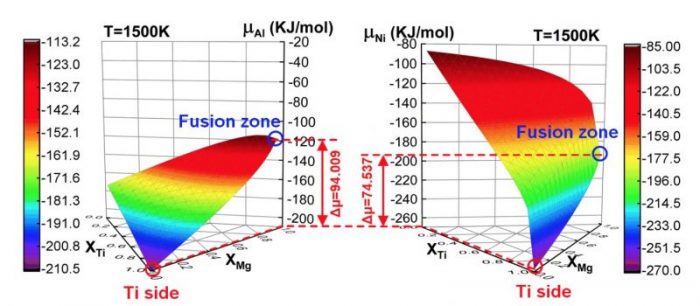
Fig.3 Chemical potential gradients of Al and Ni elements at 1500 K (represents the value at a low laser power). Credit: Xiaoye Zhao
The thermodynamic calculation also helps to interpret the phase formation in the fusion zone. Mg, Al, and Ni atoms tend to accumulate, and a Mg-Al-Ni ternary phase is estimated to form by analyzing an (Mg-Ni-Al)-0.047Ti pseudo-ternary system. The Mg-Ti bonding mechanism is clearly clarified with the assistance of the thermodynamic calculation.
The paper also establishes the relationship between the microstructure and the mechanical properties. The fracture loads of joints with Ni coating were much higher than that of joints without coating in the identical conditions. As for the joints with a Ni coating, a higher laser power enhances the interfacial bonding and gives rise to an improvement in the fracture load. However, further increase of laser power caused the dispersion of reaction phases in the fusion zone and at the Ti substrate instead of at the interface. The reinforcement of interfacial bonding is thus weakened, leading to the decline of the fracture load. The maximum value attains 3900 N at the laser power of 1500 W, which is three times of joints without coating. In this case, the joints fracture at Mg base metal, while others crack from the fusion zone-Ti interface.
These findings are described in the article entitled Influence of Ni coating on interfacial reactions and mechanical properties in laser welding-brazing of Mg/Ti butt joint, recently published in the Journal of Alloys and Compounds. This work was conducted by Caiwang Tan, Jia Yang, Xiaoye Zhao, Kaiping Zhang, Xiaoguo Song, Bo Chen, Liqun Li and Jicai Feng from the Harbin Institute of Technology and Harbin Institute of Technology at Weihai.