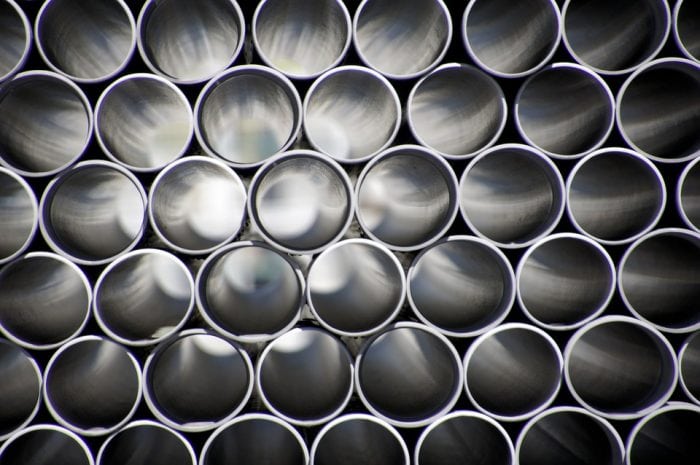
A fluid transient analysis of the Power Operated Relief Valve (PORV) discharge piping, which is connected to the Main Steam Line (MSL), has been performed to evaluate the hydrodynamic loads caused by a sudden opening of the PORV (Lim, 2018).
One component of the pipe reaction force is called the wave load. The wave load is induced by pressure waves propagating at an acoustic speed along the fluid piping systems. Pressure waves are produced by a sudden change in fluid momentum during the brief period of acoustic transient immediately after the valve opening or closure. Consequently, it is important to ensure whether the hydrodynamic load will challenge the allowable stresses for the piping and its supports as observed in the PORV transient incident.
Given the complexity and highly transient nature of this phenomenon, a detailed calculation of the fluid transient can be performed using the RELAP5/MOD3.3 (Patch 03) computer code. RELAP5 (Reactor Excursion and Leakage Analysis Program, version 5) is a light water reactor transient analysis code developed for the United States Nuclear Regulatory Commission (U.S. NRC) for simulation of a wide variety of hydraulic and thermal transients in both nuclear and non-nuclear systems involving mixtures of steam, water, non-condensable gases, and solutes under single-phase and two-phase conditions.
RELAP5 Model
The RELAP5 model of the PORV discharge piping, which is connected to the MSL, has been prepared to evaluate the hydrodynamic loads resulting from the PORV sudden opening. Each pipe reaction force was computed using the AptPlot software post-processing command files that use the results from the RELAP5 calculation as the inputs. The pipe reaction force was computed by the calculation approach presented in the next section.
Pipe Reaction Force
The generalized force equation in one-dimensional form, which can be resolved for a piping segment bounded by two elbows, is written as:
where ρ = density, A = flow area, V = velocity, α = void fraction, z = distance along piping axis, gc = gravitational constant (used for English unit calculation), and subscripts f and g refer to liquid and gas phases. This is the unsteady reaction force, which is called the wave load that is caused by the rate of fluid momentum change within the control volume represented by the pipe segment. The sign convention applied in all calculations shows that the force is positive in the nominal direction of the flow, unless defined otherwise.
In addition to the wave load, this system has thrust loads due to the discharge of the fluid from the 18-inch (0.457 m) pipe spool to the 71-inch (1.803 m) silencer. The thrust loads include the momentum flux of the discharging fluid (Fm) as well as the differential pressure at the pipe exit (Fp).
where me = mass flow rate at the pipe exit, Ve = exit velocity, and gc = gravitational constant. The exit velocity can be calculated with the static quality (x) and the velocities of the liquid and the gas phases, which is written as:
where P = pressure, A = flow area, and subscripts e and a refer to the exit and the ambient.
Results
The peak loads compared to the flooded weights for each pipe segment. The flooded weight is the summation of the weight of the pipe and the weight of water. As a result, the peak loads are greater than the flooded weights at the PORV discharge piping (pipe components 009 to 013). This result is expected with the criterion for the disturbance time.
In this analysis, the PORV opening time, which was assumed as 0.05 seconds, is the disturbance time. The distance from the PORV to the SG (upstream pressure boundary) is approximately 280 ft (85 m) and the speed of sound is approximately 1,640 ft/sec (500 m/sec). Consequently, the pressure wave propagation time is computed as 0.171 seconds. If the disturbance time is at least 10 times larger than the calculated pressure wave propagation time, i.e. 1.71 seconds, the pressure wave propagation is insignificant.
In contrast, the peak loads are less than the flooded weights at the MSL (pipe components 003 to 007). This is due to the limited pressure wave propagation at the tee where the 8-inch (0.203 m) PORV piping (pipe component 009) connects to the 30-inch (0.762 m) MSL piping (pipe component 007). At this location, 7% of the pressure pulse is transmitted to the MSL, but the remaining 93% is reflected to the PORV discharge piping based on the pressure pulse transmission coefficient calculation.
The hydrodynamic load calculation can be used for stress analysis of the piping systems, including the evaluation of active supports. However, the forces calculated with RELAP5 are purely dynamic loads. Therefore, thermal loads, if applicable, as well as the static loads due to the weights of pipes, internal fluids, and piping supports, are not included in the RELAP5 analysis and are the responsibility of the piping structural analysis.
These findings are described in the article entitled RELAP5 analysis of hydrodynamic loads in response to PORV actuation, recently published in the journal Annals of Nuclear Energy. This work was conducted by Jaehyok Lim from Fauske and Associates, LLC.