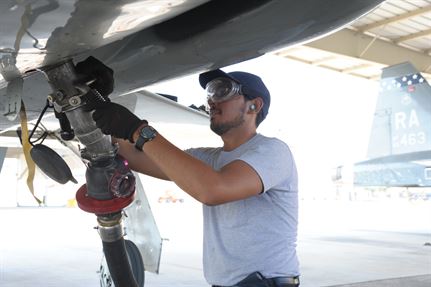
Solvent dehydration processes have a high economic and environmental relevance in the pharmaceutical, fine-chemistry, and chemical industries. In particular, ethanol dehydration is one of the most important applications. Bioethanol has an important advantage over other biofuels, since it can be directly integrated into existing fuel systems, typically as a mixture with gasoline, not requiring modifications of the current engines, ensuring environmental sustainability and process economy.
Gas dehydration can be used for the dehydration of natural gas, drying of gases for packaging purposes and humidity control in closed spaces, such as air conditioning in buildings, aviation, and space flight. In particular, dehydration of flue gas originated in the production of electricity by coal-fired power plants, has a great interest due to the energy saving in power plants and reduction of diffusion of pollutants through water. Another potential application is biogas dehydration which, after purification, can be used as an alternative to natural gas and be distributed as a power supply in rural and urban areas.
When compared to other dehydration methods, membrane-based dehydration has numerous benefits. Membrane technology involves a lower energy consumption since the only energy consumed is the amount required to maintain a partial pressure difference across the membrane. Additionally, this technology is usually rather flexible and involves a compact modular design, which is easy to maintain and control.
The critical issue is to achieve membranes with high permeability and selectivity combined with good chemical and mechanical stability at high temperatures, with a reasonable cost. Hydrophilic polymers, such as polyvinyl alcohol (PVA), polysulfone (PS), polyamides (PA), among others, have been selected as membrane materials for the dehydration of various solvents. In gas dehydration, hydrophilic polymers, such as polyacrylonitrile (PAN), sulfonated polyetheretherketone (SPEEK), and poly(vinyl alcohol (PVA), are usually used. Their drawback is that they are petrochemical-based polymers and involve the use of solvents in their manufacture.
Therefore, developing environmentally-friendly materials for the preparation of membranes is attracting much attention. Particularly, polysaccharides, such as alginate and chitosan, have been tried for solvent dehydration due to their high affinity for water, solvent resistance, and high separation performance. However, for gas dehydration, these are rarely reported, and cellulose acetate (CA) is the most common biopolymer used for drying of compressed air since it presents an adequate H2O/N2 selectivity.
Hybrid membranes have become an important research topic in membrane science because they combine the easy processing and low-cost of polymeric membranes with the high permeation fluxes and mechanical properties of inorganic membranes.
This work evaluates new membrane materials obtained from a renewable source, for ethanol and gas dehydration. The novel hybrid polysaccharide membranes were prepared with FucoPol – produced by Enterobacter A47, using as carbon source the glycerol by-product of the biodiesel industry. Microbial polysaccharides can advantageously be used as alternatives to other natural biopolymers, such as plant or algae-derived products, due to their novel or improved properties. These polymers offer the advantage of being produced from renewable resources, under controlled environmental conditions that assure both the quantity and the quality of the final products.
In order to reinforce the mechanical and thermal properties, incorporation of a SiO2 network homogeneously dispersed was obtained by using a sol-gel method with GPTMS as a crosslinker silica precursor.
These membranes were applied in ethanol dehydration with a higher transport performance (similar to PERVAP® 4101 commercial membrane), but an irreversible swelling in the presence of water was noticed, compromising long-term operation.
On the contrary, these hybrid membranes exhibited high selectivity to water vapor and showed a good stability during H2O/N2 separation, constituting potential candidates for other industrial gas dehydration processes, such as biogas and flue gas.
These findings are described in the article entitled, Development and Characterisation of Hybrid Polysaccharide Membranes for Dehydration Processes, recently published in the journal Carbohydrate Polymers. This work was conducted by Inês T. Meireles, Rosa M. Huertas, Cristiana A.V. Torres, Isabel M. Coelhoso and João G. Crespo from the Universidade Nova de Lisboa.