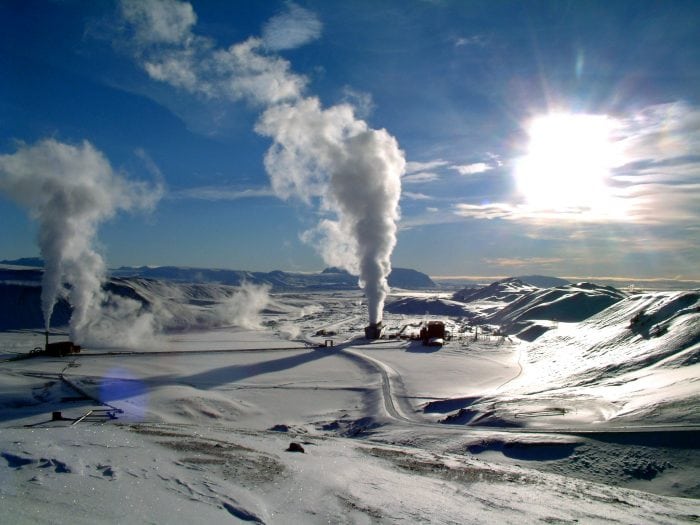
Borehole data are important for both scientific investigation and technical usage of geothermal systems. However, even simple measurements as pressure and temperature logs meet technical limitations.
Especially complex technologies are missing the step from laboratory level to downhole operation. One example is chemical sensors, which require electronics for data recovery and transmission in housing with heat shields and cooling systems for longer operations (Gerlach et al, 2014). Thus, for optical measurements windows, a ceramic metal connection for the given ambient constraints and protected electronics able to process visual data are required. Another difficult application is a seismic measurement device for real-time monitoring during drilling (Jakusch, 2014).
ZWERG represents a comprehensive concept for logging and sampling that addresses harsh conditions that are encountered in geothermal wells. The system platform approach targets complete mastering of geothermal wells by engineering methods. These include real-time remote-controlled tools for measurement and more complex operations as video-inspection, fully-controlled sample taking, downhole tracer testing, and maintenance operations as downhole repair of casing leakages. In a first step, a modular system platform with important components is being developed matching the Soultz-sous-Forêts’ reservoir condition with 200 °C, 600 bar at 5.000 m depth and open-hole diameter 8 ½ inches (BINE, 2017). The platform solutions are supposed to be advanced in later steps using a modular design.
Modular system platform concept
In large industry sectors, the system platform approach is a common method that allows for rapid development and the continuous realization of new products at reduced costs and without quality losses (Sheridan, 2013; Danilovic et al., 2007). A basic element in this strategy is the combination of parts and components from different producers in complete end products (Lemke, 2017).
The system platform for downhole tools ZWERG contains basic components, which are identified to be necessary for every wireline operation, including pressure resistant housing, energy supply, heat shield, cable connection, control electronics, housing connectors, seals among others. In combination with functional modules (e.g., camera or other sensors), functional tools are derived. The platform is supposed to support independently developed sensors and actuators for accelerating the development to the operational state.
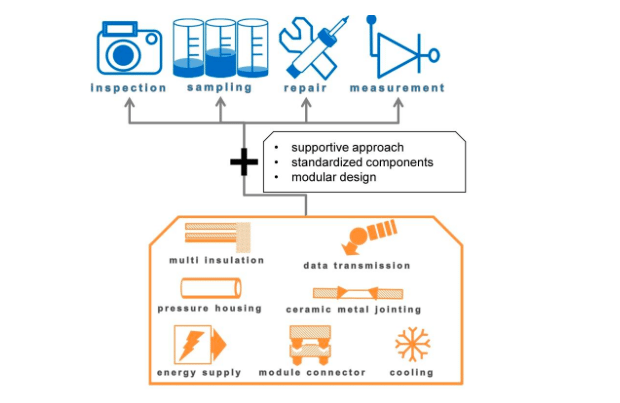
Figure 1: System platform concept for downhole tool applications. Credit: Benedict Holbein
Tool housing and interior design
For the high surrounding pressures, material strength is important. Additionally, the material properties are influenced by high temperatures and corrosion. For offshore oil and gas plants or high-temperature steam turbines, nickel-base alloys with high tensile strength and corrosion resistance even at high temperatures are used. For the platform components, the alloy 2.4668 is selected, allowing minimal wall thickness (8mm for housing diameter 95 mm) at 600 bar ambient pressure and matching the requirements regarding machinability and availability.
Internal components are pressure protected by the housing, thus, alternative fabrication methods are usable. A used method which enables complex geometries while saving weight by an optimized topology is Selective Laser Melting (SLM). This 3D printing method is practicable with metals, e.g., aluminum. Additionally, the fabrication costs for a structure are up to 10 times lower compared to cutting fabrication because the fully automated process allows fabrication of several components at once in the melting furnace. However, the design rules and properties differ strongly from conventional cutting, e.g. Seepersad et al (2012). As opposed to conventional fabrication, SLM shaping is done starting from zero structure.
Figure 2 shows mounting frames fabricated with cutting fabrication b) and SLM a). The structure with cutting is already extremely complex and respectively expensive but it still represents a compromise. For example, the frame for camera sensors in a video inspection tool where an angle of 60° between two cameras is required to allow an uninterrupted 360° view could only be fabricated with SLM.
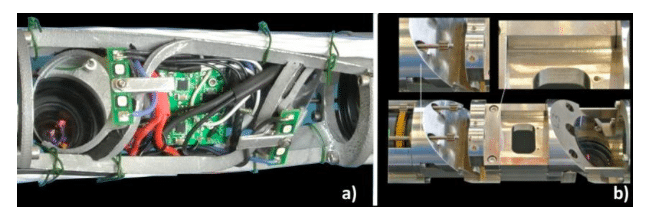
Figure 2: Complex 3D frame for taking optical components, fabricated with SLM a) and cutting b). Credit: Benedict Holbein
Down-hole data processing and data transmission
In order to support the communication between the downhole tool and surface, it is advantageous if data can be processed down-hole. A beneficial method for improving the data transmission over long distances is e.g. a pre-distortion of the signal which allows modifying the signal for the properties of a wire-line and thus optimizing the received data quality, as Schubert (2015) investigated. Other applications for down-hole data processing are the evaluation of measured data or logging signals and the processing of images. Therefore it is necessary to have electronic systems with sufficient computing power and a robust design, e.g. Metasch (2015).
For this purpose, the embedded system Z7Brd01 was designed. It is based on a concept with internal solid core processor and a Field Programmable Gate Arrier (FPGA) on a single chip. The main advantages of this structure are that an internal communication bus between FPGA and System on Chip (SoC) provides an optimal data consistency, a wide range of development tools, since both components come from the same manufacturer, and a low cooling effort, since the number of active elements is reduced.
In Figure 3, the internal board structure is illustrated. It contains a DDR3L as main memory, a high-performance dual-core processor and a memory band-with with a sufficient capacity to realize complex operations as multiple camera streams for realizing the processing of a panorama view and stereoscope video streaming, Wiegel (2015) and Spatafora et al (2015).
The complete system is usable at operating temperatures of up to 125 °C. Some components are only qualified for 105 °C but they can be cooled using Peltier elements. They may also be qualified for 125 °C perhaps by accepting a slightly decreased lifetime.
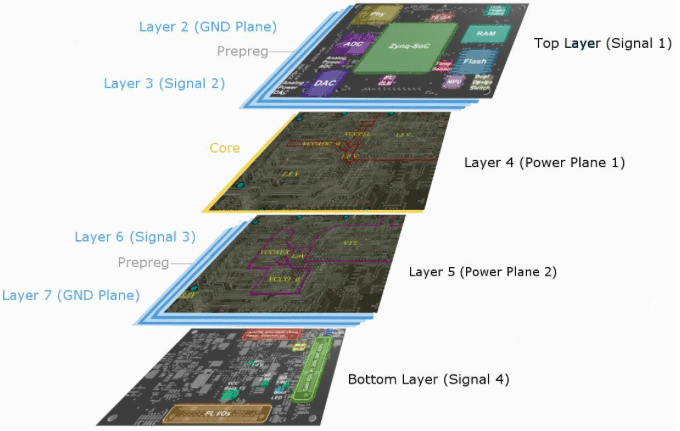
Figure 3: Structure of embedded downhole CPU system. Republished with permission from Elsevier from: https://doi.org/10.1016/j.geothermics.2017.10.010
Coaxial based wirelines are commonly used for communication and energy supply in downhole tool operation due to the reliability and mechanical robustness. Applications with low data complexity can be managed without additional effort but higher data rates bring the wireline transmission to its limits mostly because of the frequency-dependent damping, i.e. the high-frequency components of the signal are more attenuated than the low-frequency components. To compensate this frequency-dependent attenuation and other distortion from the communication environment, a pre-distortion at the transmitter and equalization at the receiver is necessary. The pre-distortion allows maximizing the channel capacity and the equalizers in the receiver minimizes other interferences such as group delay distortion, which acts during transmission.
A pre-distortion method called water-filling is based on a model of the damping behavior, where, “good sub-bands” (with low SNR) have greater performance than bad ones, and individual sub-bands may not be loaded at all. A static solution for measured wirelines exists, e.g. Schubert et al (2015) but real wireline behavior is not static. Indeed, the distortion of the signal depends on the total length of the wireline and environmental factors, such as the ambient temperature in different depths. An adaptive method which automatically adjusts the model of the transmission situation during operation transmission is part of current research.
Heat management
When operating in high-temperature environments heat management is a basic factor, even if special electronics are used. A first step is the reduction of external heat input using high-performance heat insulation.
For axial insulation, PTFE is a suitable material since it has a low heat transfer coefficient, good shape-ability and sufficient solidity for mounting components. For radial insulation of the systems, a combination of vacuum insulation and Multi-Layer Insulation (MLI) is used. Vacuum insulation strongly reduces heat transfer by conduction and convection which depends on the number of fluid molecules in the evacuated volume. It is realized by cylindrical Dewar flasks. For the reduction of heat transfer by radiation, thin layers of reflecting material (tin foils) are mounted between the Dewar flasks and the housing. If transparency is required, simpler glass Dewar flasks can be used.
No insulation is perfect and electronics also produce heat inside the tools, thus cooling is another important factor. For many operations down-hole an operation period of several hours is sufficient, e.g. Holbein et al (2015). Since down-hole temperatures increase with increasing depth and a large part of the operation time is the time for driving the tool up and down, only part of the operation takes place at maximal ambient temperature. A simple and reliable concept is a combination of PCM (Phase Change Materials) and heat-pipes cooling. PCM is used as heat-sink which absorbs heat during the melting process at certain temperatures which are below the maximal allowed electronics temperature.
The heat produced by electronics is transferred to the PCM sink using heat-pipes. These small pipes filled with a small amount of refrigerant (e.g. water) are evacuated to reduce the internal pressure and therefore the evaporation temperature (this can be done to achieve a specific evaporation point). Once they are heated up at one side (connected to the heat source) over this temperature, the refrigerant evaporates and the vapor expands with sonic speed inside the pipe. Reaching the other side which is connected to a heat sink, the vapor is cooled down and condenses. Heat is thus transferred to the heat sink. Through capillary structures inside the pipes, the condensate flows back to the heat source side, so the process can be repeated. This way a huge amount of heat can be transferred using a minimal amount of space.
Figure 4 shows a PCM based cooling system. In order to optimize the heat transfer between the cooling body and heat-pipes, they are pressed into the body using heat transfer paste with a higher heat transfer coefficient as air. The storage body is pressed on its mounting surface using a mechanical press mechanism.
The heat-sink storage itself is hermetic so there is no risk of heat-sink liquid flowing into the electronic section. It can be removed quickly and exchanged for another one. Hence the heat-sink capacity can be adjusted by simply mounting a larger (longer) storage. The heat-sink material can be regenerated by cooling it down to initial temperature (e.g. -10 °C).
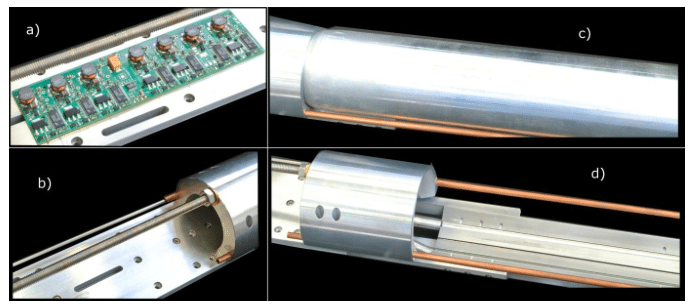
Figure 4: A cooling body for electronic installation a), integration of heat-pipes for heat transfer b), mounting surface for heat-sink storage with c) and without heat-sink storage d). Republished with permission from Elsevier from: https://doi.org/10.1016/j.geothermics.2017.10.010
If some hours are not sufficient operation time, permanent cooling is required. The concept of cooling without theoretical time limitation by designing a downhole refrigeration system is a highly challenging task, because of the extremely harsh ambient conditions. Therefore the development of such systems is part of the currently-ongoing research.
Conclusion
A wide range of tools for different applications which are suitable for the harsh ambient conditions in deep geothermal boreholes could support an advanced quality management in geothermal systems. The development of those tools is expensive and time-consuming. The results are often not reproducible or transferable. The system platform ZWERG represents a method for reaching this target by finding solutions to basic technical problems and translating it into a pool of basic components and functional modules. The supportive approach can accelerate the development of operational tools and bring innovative (sensor) technologies into in situ operations. A step towards the claimed target of mastering boreholes with engineering methods is done.
The modular structure of the ZWERG platform allows accelerated development of new components and tools. A first exemplary complete tool is realized with the camera system GeoKam, Spatafora et al (2016). Currently, a second complete tool for a remote-controlled taking of undisturbed water samples is being developed.
These findings are described in the article entitled Quality management and improvement for geothermal energy projects using the platform-based tool development technology − ZWERG, recently published in the journal Geothermics. This work was conducted by Benedict Holbein, Stefan Dietze, Franziska Hurst, Jörg Isele, Luigi Spatafora, Friedrich Wiegel, and Veit Hagenmeyer from the Karlsruhe Institute of Technology.
References:
- Gerlach F., Berthold M., Vonau W.. 2014. Chemosensorik für die Erkundung von Tiefbohrungen (engl. Chemo-sensors for the investigation of deep wells). Geothermal Congress 2014. Essen, Germany.
- BINE Information Service. 2017. Geothermal electricity generation in Soultz-sous-Forêts, project 30 info, website: www.bine.info/en/publications/publikation/geothermische-stromerzeugung-in-31 soultz-sous-forets/.
- Holbein, B. et al. 2015. Integrated Cooling Systems for an Extended Operation Range of Borehole Tools, proceedings, Geothermal Resources Council, 39th Annual Meeting, Reno, Nevada.
- Lemke, H. 2017. MQB – Die Modul-Baukasten-Strategie des Volkswagen-Konzerns im Zusammenspiel mit globalen Systemlieferanten (ENG. The modular Platform Strategy of the Volkswagen Corporation with Global System Deliverers). http://www.rkw-bw.de/rde/pdf/RKW-Organisation-2013/Vortrag-Lemke-VW.pdf.
- Metasch, R.. 2015. Methoden zur zuverlässigen thermischen und mechanischen Auslegung von Elektronik in der Geothermie (Eng. Methods for the reliable thermal and mechanical design of electronics for geothermal energy applications), proceedings, Geothermiekongress Essen, Germany.
- Schmitt, S. 2011. Gesellschaftlicher Nutzen und Akzeptanz von Geothermie (engl. Social Benefit and Acceptance of Geothermal Energy); 4th North-german Geothermal Conference; Nov. 26.-27, 2011; Hannover, Germany.
- Schubert, B. et al. 2015. Concept of a cable Modem for Data Transmission over a Wireline, proceedings, Geothermiekongress 2015, Essen, Germany.
- Seepersad, C. et al. 2012. Design Rules For Selective Laser Sintering, Mechanical Engineering Design Projects Program, University of Texas, Austin, Texas.
- Sheridan, M. 2013. Product Platforms: A Winning Strategy, Spotlight Article, www.ptc.com.
- Spatafora, L. et al. 2015. Forschungsergebnis: Geokam – Mechanik, Elektronik und Design des Videoinspektionssystem (Eng. Research result: GeoKam – Mechanic, Electronic and Design of the video inspection system), proceedings, Geothermiekongress Essen, Germany.
- Spatafora, L. et al. 2016. The GeoKam – A Tool for Video Inspections in Hot Deep Geothermal Boreholes, PROCEEDINGS, 41st Workshop on Geothermal Reservoir Engineering, Stanford University, Stanford, California, SGP-TR-209
- Wiegel, F.. 2015. Entwicklung eines Kommunikations- und Steuerrechners für eine Bohrlochsonde (Eng. Development of a communication and control computer), proceedings, Geothermiekongress Essen, Germany.