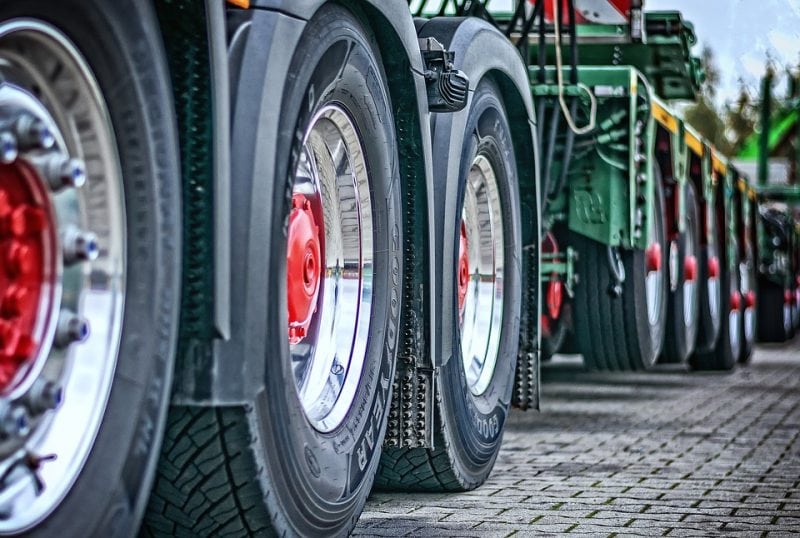
The heavy-duty engine industry in the United States faces a difficult challenge in demonstrating engine technologies to achieve 55% brake thermal efficiency (BTE) for future heavy-duty diesel engines under the aegis of the US Department of Energy’s ongoing SuperTruck II program (US DOE, 2017). BTE is a measure of the conversion of the fuel’s chemical energy to useful power at the engine shaft. As part of the portfolio of strategies being considered to enable high BTE operation, various advanced low-temperature combustion strategies and waste energy recovery (WER) are significant.
As researchers work hard to squeeze every last percentage point of BTE of the internal combustion (IC) engine, it becomes increasingly important to either prevent or to recover the fuel’s chemical energy that is wasted. Two major contributors to engine inefficiency include energy transferred in the form of heat transfer to the engine coolant and energy lost with hot exhaust gases that exit through the engine exhaust manifold. Strictly speaking, it is not the energy that is important here, but the usable portion of the energy, technically called “exergy,” which is always defined with respect to an environment (known, somewhat dramatically, as the “dead state,” which by definition has zero exergy) (cf. Bejan, 2016).
“Global” exergy analyses of engine processes have been used previously to quantify the fractions of the fuel’s chemical exergy that are lost due to irreversible processes (most “real” energy conversion processes are “irreversible”). Exergy destruction occurs in the combustion process and exergy is also lost with heat transfer to the coolant and with exhaust gas flows out of the engine. Global exergy analyses provide percentage-wise distribution of exergy in various channels, thus identifying the sources of irreversibilities. However, more detailed information is needed to reduce exergy destruction from these various sources. For example, it is necessary to quantify time (or crank angle) -resolved exergy flows in engine exhaust to determine how to extract useful work but no previous study has examined this important aspect of exergy flows in exhaust gases.
Recently, Mahabadipour et al. (2018) performed the first characterization of crank angle-resolved exergy flows in the exhaust of a diesel engine from the perspective of exhaust WER. In this work, the authors introduced a novel methodology that leveraged experimental high-speed exhaust pressure measurements with system-level engine simulations to calculate crank angle-resolved exhaust exergy.
They also presented the first results that quantify the thermal (i.e., due to temperature) and mechanical (due to pressure) components of exhaust exergy as well as the exergy apportionment between different temporal phases of the exhaust process such as the “blowdown” and the “displacement” phases. Although these results were presented only for diesel combustion in a single-cylinder research engine, the technical approach introduced in this study is applicable for determining the types of exhaust WER devices that are most appropriate for different engine configurations and operating conditions.
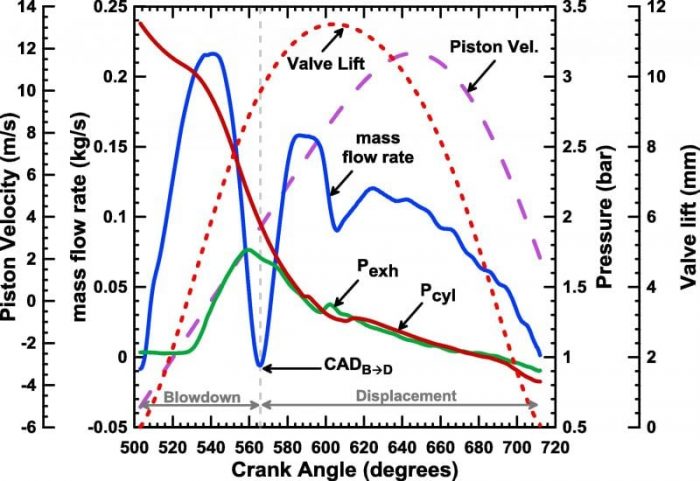
Figure 1. Blowdown and displacement phasing at 1500 rpm, intake pressure of 1.2 bar [Mahabadipour et al., 2018]. (Republished with permission from Elsevier)
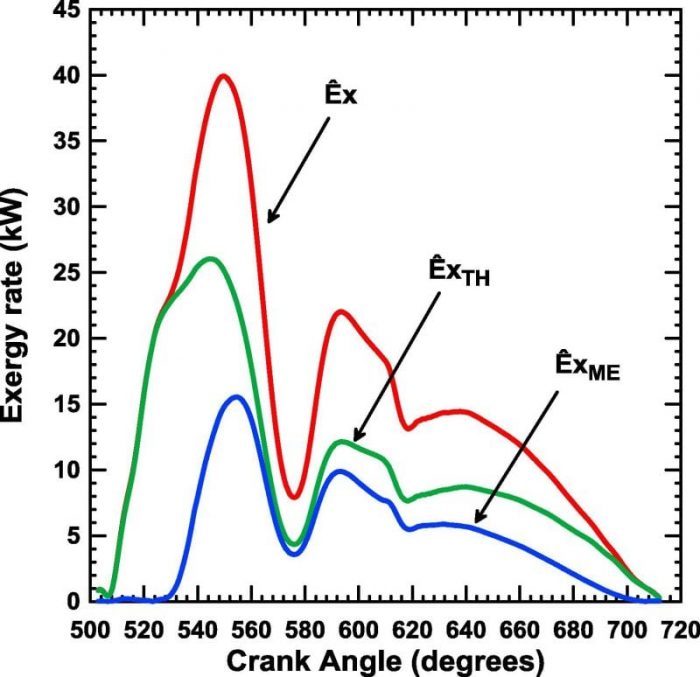
Figure 2. Crank angle-resolved total exergy rate (Ex) and its thermal (ExTH) & mechanical (ExME) portions at 1500 rpm and intake pressure of 2 bar [Mahabadipour et al., 2018]. (Republished with permission from Elsevier)
Another exhaust WER strategy that recovers the thermal component of exhaust exergy utilizes an organic Rankine cycle (ORC)-based “bottoming cycle.” In essence, ORC-based bottoming cycles are very similar to Rankine cycles utilized in thermal power plants except that ORC cycles employ organic working fluids (e.g., refrigerant mixtures) instead of steam. In contrast to turbocharging and ORC cycles, other “direct” WER devices (e.g., positive displacement expanders) endeavor to directly utilize the mechanical component of the exhaust exergy.
In summary, Mahabadipour et al. provide a systematic approach, firmly rooted in fundamental thermodynamic principles, for engine designers to determine the best possible ways to recover exhaust exergy for a variety of engines and operating conditions to achieve potentially significant efficiency improvements.
These findings are described in the article entitled Crank angle-resolved exergy analysis of exhaust flows in a diesel engine from the perspective of exhaust waste energy recovery, recently published in the journal Applied Energy. This work was conducted by Hamidreza Mahabadipour, Kalyan Kumar Srinivasan, and Sundar Rajan Krishnan from the University of Alabama and Swaminathan Subramanian from Eaton Corporate Research and Technology.
References:
- Bejan, A. (2016). Advanced Engineering Thermodynamics, 4th Edition, Wiley, ISBN 978-1119052098
- Mahabadipour, H., Srinivasan, K.K., Krishnan, S.R., Subramanian, S. (2018). Crank angle-resolved exergy analysis of exhaust flows in a diesel engine from the perspective of exhaust waste energy recovery. Applied Energy, 216, 31-34, (https://doi.org/10.1016/j.apenergy.2018.02.037.)
- US DOE (2017). SupertTruck II, Vehicle Technologies Office Program Wide Selections to Accelerate the Development of Innovative Technologies; https://www.energy.gov/articles/energy-department-announces-137-million-investment-commercial-and-passenger-vehicle (accessed April 2, 2018)