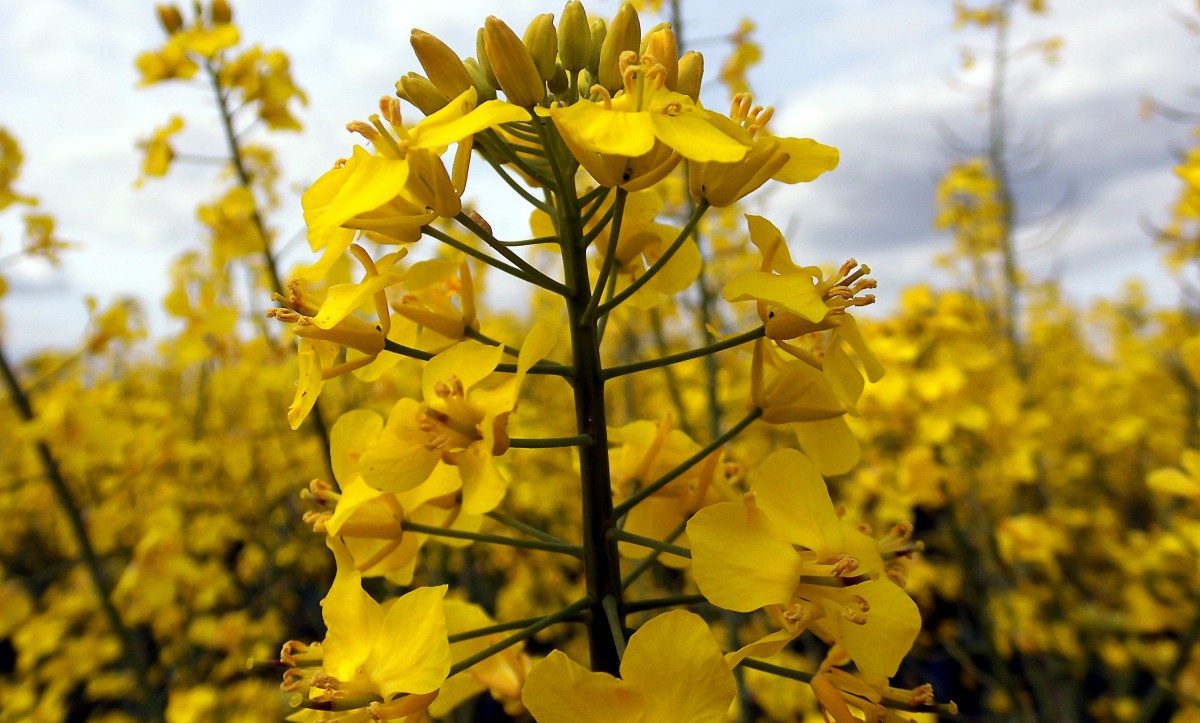
The biodiesel industry has been growing substantially around the world and given the increasing demands for renewable diesel, further growth is expected. Compared with mineral diesel, biodiesel offers unique advantages such as biodegradability, being non-toxic, as well as safe storage and handling. Moreover, its combustion is associated with substantially reduced polluting emissions.
Along with biodiesel, also known as alkyl esters of long chain fatty acids (C14-C24), a great deal of glycerol as a by-product is also generated, typically equaling 10% of the whole production volume. If not handled properly or, in better words, if it ends up as waste, such a huge stream of organic waste could to some extent jeopardize the environmentally-friendly nature of the whole process. In light of that, efforts have been directed to convert biodiesel glycerol to value-added products to not only address the above-mentioned challenge but to also enhance the economic viability of the process.
Among value-added products, glycerol acetates (also known as acetins) has attracted a great deal of attention owing to its diverse industrial applications (as cryogenics, cosmetics, and fuel additives) and is produced through the esterification of glycerol with acetic. This reaction is reversible and multi-step and a number of factors such as higher reaction temperatures and acetic acid to glycerol molar ratios could lead to higher yields of the product, i.e., acetins. However, the conditions resulting in higher yields are not necessarily the most eco-friendly, resource-efficient, and cost-effective ones. Fortunately, through the application of advanced engineering tools such as exergy analysis, this shortcoming could be overcome to a great extent. In better words, the irreversibility aspects of energy and material conversion processes can be precisely located and quantified using the exergy analysis.
In a recently published work, we performed a detailed exergy analysis of a continuous reactor we developed to valorize glycerol through esterification with acetic acid. All the exergetic analyses were based on the experimental data obtained. We also used response surface methodology (RSM) to develop mathematical models for three major exergetic parameters namely normalized exergy destruction, universal exergetic efficiency, and functional exergetic efficiency based on four independent variables including feed flow rate, acid acetic to glycerol molar ratio, reaction temperature, and pressure. We then used the developed models to optimize the operating conditions of the reactor by maximizing universal and functional exergetic efficiencies and minimizing normalized exergy destruction. Interesting results were obtained which have been summarized herein.
More specifically, the normalized exergy destruction of the process was decreased significantly by increasing feed flow rate. On the contrary, elevating both acetic acid to glycerol molar ratio and reaction temperature led to increased normalized exergy destruction of the process. In case of the universal exergetic efficiency of the process, this parameter was increased by increasing feed flow rate, while a negative correlation was observed between this index and both acetic acid to glycerol molar ratio and reaction temperature. The functional exergetic efficiency of the process was decreased by elevating all the four independent parameters mentioned above.
Moreover, it was found out that RSM could adequately predict the exergetic performance parameters of the reactor (R2 > 0.98). Accordingly, the most thermodynamically favorable conditions for glycerol esterification with acid acetic were found to be reaction temperature of 117 °C, feed flow rate of 0.6 mL/min, acid acetic to glycerol molar ratio of 1.1, and pressure of 1 bar. Under these conditions, the normalized exergy destruction, universal exergetic efficiency, and functional exergetic efficiency stood at 3.1, 37.5%, and 20.8%, respectively.
Overall and based on the findings of this study, exergy analysis would be highly recommended to be used for locating and quantifying the resource depletion associated with chemicals production processes from renewable sources. Moreover, in order to achieve the most cost-effective and eco-friendly production conditions of renewable chemicals such as acetins, future research should also take into account the economic and environmental aspects by using exergoeconomic and exergoenvironmental approaches.
These findings are presented and discussed in the article entitled Exergy-based optimization of a continuous reactor applied to produce value-added chemicals from glycerol through esterification with acetic acid, recently published in the journal Energy. This work was led by Mortaza Aghbashlo from the University of Tehran and Meisam Tabatabaei from the Biofuel Research Team (BRTEam) /Agricultural Biotechnology Research Institute of Iran (ABRII). The research team also included Elena Valijanian from ABRII as well as Hajar Rastegari and Hassan S. Ghaziaskar from the Isfahan University of Technology.
* Source: https://doi.org/10.1016/j.energy.2018.02.151; Necessary permissions have been acquired from Elsevier; Copyright 2018© License Number: 4324990009317.