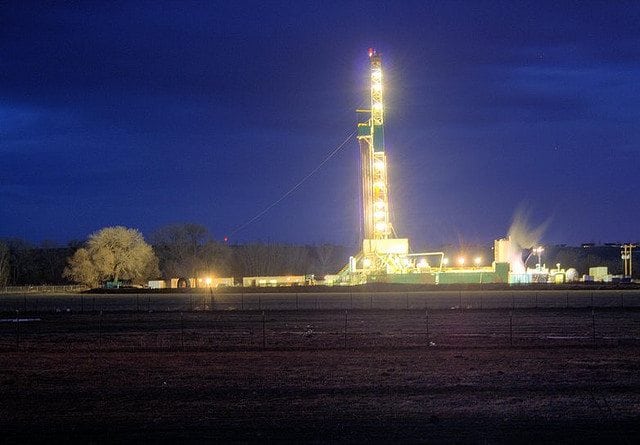
Welcome to the My Science Life submission by Jim Pazos, Drilling & Completion Fluids Engineer. The ‘My Science Life’ project is a core part of Science Trends’ mission to communicate science. It is an opportunity for people, like yourself, to share the knowledge you’ve built up over the years without the endless peer reviews.
Interested in being part of the My Science Life project? You can find the details about submission here.
The Uintah Basin is a basin within the larger Colorado Plateaus province that extends through Utah, Arizona, Colorado, and New Mexico. It is a complex basin that is the source of oil and gas production in the area. The unconventional play is targetted for its oil and gas in multiple horizons.
Drilling in the Uteland Butte formation in N.E. Utah, you can experience an unusual problem.
It is known for its “Black Wax” & “Yellow Wax” paraffin that, while using an Oil based mud, goes into solution & causes funnel viscosity & gel strength to climb extremely high. The best solution when using an OBM has been to dilute it back with diesel.
Because of this problem paraffin causes OBM, most found a better solution is to use of a specialty WBM which is sometimes referred to as an SAGD fluid (Steam Assisted Gravity drainage). Highly inhibitive cationic mud prevents accretion of bitumen on tubulars while preventing swelling of clay.
It’s the Green River Formation through the Uteland Butte (the pay target) that we drill here.
We drill the vertical with WBM. From 8000’ – 9000′ TVD drill the lateral with OBM, for an additional approximately 10000′ – 12,000’ MD more.
In the laterals, we use OBM’s. In hopes to find an answer to the problem of paraffin contamination of OBM, I field tested using a store purchased Fabric Softener, which is an anionic Surfactant. The brand used was Downey Ultra.
Keep in mind that this was FIELD experiments. Taken from a sample of one, 200 barrel batch of paraffin contaminated OBM & it had already been diluted back with diesel. I was not around for it so I don’t have details on particulars. My understanding is during contamination, gels were +200 and even this diluted back batch, still had rather high gel strengths.
Due to my equipment limitations, measurements were +/- while pilot testing, so possibly 5% or so could be off on my estimated barrel sample (ie +/-350 ml).
Rheology all at 150°F | Scenario 1 | Scenario 2 | Scenario 3 |
Sample | 1% Fabric Softener | 1.5% Fabric Softener | 2.5% Fabric Softener |
15.05 ppg | ES 443 | ES 584 | ES 534 |
81/19 OWR | PV/YP 34/22 | PV/YP 35/22 | PV/YP 39/26 |
ES 447 | 600/300 90 / 56 | 600/300 92 / 57 | 600/300 104 / 65 |
PV/YP 33/24 | 200 /100 44 / 30 | 200 /100 45 / 32 | 200 /100 52 / 37 |
600/300 90 / 57 | 6/3 14/12 | 6/3 13/12 | 6/3 17/15 |
200 /100 44 / 30 | Gels 18/42/51 | Gels 19/28/32 | Gels 23/34/34 |
6/3 14/12 | |||
Gels 19/46/58 |
Some observations:
It has a definite positive effect’s on the gel strengths.
I have no idea what chemical treatments (other than basics) might have been made before. Therefore there may be some chemical interactions that could create variations of my results.
I do not know how it will react under high temperatures, shearing & pressure at the bit.
What will it do if a “clean system” is pretreated with Fabric Softener (I could call it anionic surfactant, but it’s funnier calling it by its grocery store name) as opposed to treating after or during contamination?
What effects (if any) will it have on HTHP & will that change over a temperature range.
Likely focus of research should be in the 1% – 2.5% range as a treatment recipe.
Ranges for pretreating probably should range 0% – 5% & checking properties after introducing contamination
Higher % Fabric softener might be warranted when dealing with undiluted OBM when encountering the paraffin contamination.
Clearly, there is more than sufficient evidence that further testing in a controlled environment is warranted & quite possibly, a magic bullet has been found, & of all places, on the shelf of the grocery store.
Because of my results, Newfield Exploration agreed to support my doing further testing in the laboratory. Halliburton agreed to some limited use of their facility in an information sharing agreement.
With the blessing of Newfield Explorations drilling engineer Sean Stevens, I am presenting my findings so far.
First I would like to present a sampling of some mud properties on what paraffin contaminated OBM can look like. The mud type is a Halliburton Invermul:
Mud weight: 15.0ppg 14.2ppg 15.0ppg 15.05ppg 15.1ppg | Rheology: |
OWR: 83/17 85/15 89/11 84/16 94/6 | 600/300: 87/50 84/51 124/82 117/73 159/117 |
WPS: 297K 290K 331K 255K 279K | 200/100: 35/23 39/28 52/36 95/77 |
LGS: 3.23% 7.51% 10.52% 6.42% 6.34% | 6/3: 10/9 15/14 19/12 41/39 |
PV: 37 33 42 44 42 | ES: 796 458 956 515 768 |
YP: 13 28 40 29 75 | |
Gels: 18/56/64 30/53/59 38/84/92 12/32/40 40/57/57 |
A few observations before I move on:
Each of the wells circulating system would end up being over 2000 bbls by the end of the well.
No type or amount of organaphilic clay, viscosifier or low-end modifier chemical was ever used on any of the wells. In fact, I was told that anyone who ever used a viscosifier on these paraffin wells should get run off! Apparently, several OBM thinners were attempted & only Halliburton’s OMC 42 was reported to have an even marginal effect. On the wells I had experience on, OMC 42 had no apparent effect. When I joined this project, I was told that they had experienced down hole losses in about 50% of the wells drilled due to the formation. The only solution for the paraffin contamination was dilution & when down hole losses occurred, to use the worst of the paraffin contaminated mud to lose to the hole.
Apparently, several OBM thinners were attempted & only Halliburton’s OMC 42 was reported to have an even marginal effect. On the wells I had experience on, OMC 42 had no apparent effect. When I joined this project, I was told that they had experienced down hole losses in about 50% of the wells drilled due to the formation. The only solution for the paraffin contamination was dilution & when down hole losses occurred, to use the worst of the paraffin contaminated mud to lose to the hole.
As you can see from earlier on this discussion, I began doing my own field experiments to find a way to economically chemically treat the paraffin contamination (ie fabric softener). During my last “time off” I was able to use Halliburton’s lab to run an experiment. I took with me, a sample of some paraffin contaminated OBM.
INVERMUL-15.4 ppg CONTAMINATED OBM Using a Fann Model 75 (77) |
Temperature ºF 150 225 275 |
Pressure, psi 3,900 7,000 10,000 |
Plastic Viscosity (cp) 44 27 24 |
Yield Point (#/100ft2) 44 31 25 |
600 rpm Reading 132 85 73 |
300 rpm Reading 88 58 49 |
200 rpm Reading 70 47 39 |
100 rpm Reading 50 34 28 |
6 rpm Reading 23 17 15 |
3 rpm Reading 20 16 14 |
As you can see, the mud does thin some with increased temperatures. True bottom hole temperatures ranged from 240*F – 270*F
With using my results I got using an anionic surfactant fabric softener, I found what appears to be a good industrial grade one. I used Stepan Companies NACCONAL 90G, which is also Halliburton’s DEEP TREAT, a SODIUM DODECYLBENZENE SULFONATE of Chemical class Linear alkylbenzene sulfonate. This chemical has been used for deep water projects to help stabilize rheologies as the mud passes through the coldest spot, the bottom of the riser. I simply am using it for a different application.
Using mud from the same sample container that the FANN 75 test was done on, a 4 ppb treatment of NACCONAL 90G/DEEP TREAT was given & then the sample was hot rolled at 150* F for 16 hours.
BASE MUD PLUS 4.0 PPB DEEP TREAT; POST 16 HR, 150º HOT ROLL |
FANN 75 |
Temperature ºF 150 225 275 |
Pressure, psi 3,900 7,000 10,000 |
Plastic Viscosity (cp) 46 26 25 |
Yield Point (#/100ft2) 14 18 15 |
600 rpm Reading 106 70 65 |
300 rpm Reading 60 44 40 |
200 rpm Reading 44 33 31 |
100 rpm Reading 27 21 20 |
6 rpm Reading 8 7 6 |
3 rpm Reading 6 6 5 |
These lab tests indicate that chemical treatment of paraffin in OBM is practical & all rheologies except plastic viscosities are reduced greatly by this treatment. This was sufficient evidence to begin field use.
When back on the well site, I waited till I started seeing the signs of the paraffin contamination, which is rheology, & gels slowly but steadily climbing during drilling.
I added 1 ppb Deep Treat to the active circulating system. This was added slowly at 0.5 ppb (pounds per barrel) per circulation. The results were improved viscosity & rheology.
1 complete circulation was done with only additions of diesel, water & Barite when needed. The amount of water & diesel remained constant from 2 circulations prior to treatment till 1 complete circulation after the final sack was added.
Rheology of untreated OBM | Rheology of OBM treated with 1 ppb Deep Treat |
14.85 ppg | 14.9 ppg |
OWR 81/19 | – |
WPS 270K | – |
PV 50 | PV 48 |
YP 26 | YP 16 |
LGS 3.87% | – |
RPM’s | RPM’s |
600 126 | 600 112 |
300 76 | 300 64 |
200 57 | 200 48 |
100 36 | 100 29 |
6 10 | 6 6 |
3 8 | 3 5 |
Gel strengths 13 / 27 / 35 | Gel strengths 8 / 16 / 19 |
ES 846 | ES 808 |
NO Barite sag was detected in the hot cup after rheology & gels were run.
Funnel viscosities tended to run in the 10% lower range with treatment.
Pump pressure also decreased 300-400 psi after treatment.
During the remainder of the well, the concentration was brought up to 2.2 ppb of Deep Treat. No excessive dilution was done throughout the well & dilution was just for maintaining volume & mud weight.
Mud weight 14.9ppg |
OWR: 85/15 |
WPS: 287K |
LGS: 5.17% |
PV: 45 |
YP: 15 |
Gels: 8/16/19 |
Rheology: |
600/300: 105/60 |
200/100 44/26 |
6/3: 6/5 |
ES: 1039 |
As you can see, it has performed great on its first field use. We drilled a 2nd well on this pad, the Lucy 3 well. On this well, I actually used a cumulative of 90, 50 lbs sacks of organophilic clay to maintain solids suspension (& I am not being run off!). The effects of the Deep Treat appear to have lasting effects & even with the centrifuges running on barite recovery mode, it appears to continue to keep the negative effects from the paraffin in check. No additions of NACCONAL 90G / Deep Treat were made until after we finished drilling & were towards the end of our clean up cycle.
One final field example.
When finished drilling our Lucy 3-15-022-3WH well | A 0.2 ppb treatment of NACCONAL 90G/DEEP TREAT was then added to the system |
Mud properties at TD: | Results after circulating: |
Mud weight 14.9ppg | Mud weight 14.9+ ppg |
OWR: 80/20 | OWR: 81/19 |
WPS: 304K | WPS: 317K |
LGS: 5.18% | LGS: 4.65% |
PV: 41 | PV: 39 |
YP: 24 | YP: 14 |
Gels: 11/22/28 | Gels: 7/9/11 |
Rheology: | Rheology: |
600/300: 106/65 | 600/300: 92/53 |
200/100 46/30 | 200/100 41/23 |
6/3: 9/8 | 6/3: 6/5 |
ES: 661 | ES: 683 |
There is no doubt that negative rheological effect of paraffin contamination of OBM can be cost effectively chemically treated using this. The next question is what, if any, will be the differences on effect be on other paraffin types in other parts of the world. Another question is can this be an effective treatment for OBM/SBM that has been over treated with an organophilic clay. Obviously, more field data needs to be compiled to fully understand & appreciate all the ramifications of this treatment.
From mud testing standpoints:
Another problem with paraffin contamination for OBM – trying to do a solids analysis. Paraffin dissolves in diesel (but makes rheology climb). Paraffin solidifies at a certain temperature & become liquid when heated. Despite it being a liquid, it will not fully boil until it reaches a very hot temperature – hotter than retorts run. In other words, its chemical makeup will allow a certain portion to evaporate & show up as liquid in the graduated cylinder but the heavier chemicals in its makeup will stay liquid & not evaporate. The retort result will appear that there is more solids in the mud than actually is. A recent retort as an example – I had a 13 ppg OBM with 80/20 OWR. PV 33 yp 7, gels 4/6/7 – with those rheologies you can see I probably have a “clean mud”, yet my retort readings would indicate that it had over 15% LGS – it isn’t true, it’s just that some of the liquid never gets boiled off from the retort.
The retort result will appear that there is more solids in the mud than actually is. A recent retort as an example – I had a 13 ppg OBM with 80/20 OWR. PV 33 yp 7, gels 4/6/7 – with those rheologies you can see I probably have a “clean mud”, yet my retort readings would indicate that it had over 15% LGS – it isn’t true, it’s just that some of the liquid never gets boiled off from the retort.
The retort result will appear that there are more solids in the mud than actually is. A recent retort as an example – I had a 13 ppg OBM with 80/20 OWR. PV 33 yp 7, gels 4/6/7 – with those rheologies you can see I probably have a “clean mud”, yet my retort readings would indicate that it had over 15% LGS – it isn’t true, it’s just that some of the liquid never gets boiled off from the retort.
Despite that, wrapping condenser & stem is still very important to retain the heat as long as possible, because even with total cleaning of retort & condenser every test, the paraffin can still solidify in stem or condenser & turn it into a pressurized bomb (had a 50 ml retort exhibit metallurgic stress fractures on one test when paraffin packed it off). A 10 or 20 ml retort better simply because of less length of stem, so easier to retain heat while wrapped in aluminum foil.
A very low HTHP is better. Since the diesel dissolves paraffin, the higher filtrate, the worse the paraffin will be.
Over balanced helps keep the paraffin at bay.
Use disposable syringes for titrations, not glass. Paraffin can lock the glass ones up. I had one shatter in my hand while trying to pull back on it. Disposable ones are only good from 1-3 tests, but far better & safer.
Electrical Stability – Hard to say whether the paraffin hurts or helps ES. I had one well where it seemed to hurt ES, but another well where it seemed to increase ES. Jury out here…Weighing mud. I always cool down my mud sample then check its weight & then run retort & titrate. Until this area, the mud weight differences has always been between 0.2 ppg – 0.45 ppg. With this paraffin, I have seen weight increases ranges of 0.25 ppg – 0.8 ppg.
The cool vs hot differences in weight also doesn’t seem consistent. I don’t know if the paraffin is the reason for my never before seen up to 0.8 ppg differences or not, but something to note at least.
If you have a reserve tank farm, regularly circulating is important so paraffin doesn’t pack things off.
Special credits for this study being possible:
- Sean Stevens, Sr Drilling Engineer at Newfield who had enough faith in me to find an alternative solution to dilution (“the magic bullet”).
- Dan Gwin, Service Coordinator at Halliburton who helped arrange laboratory use at Halliburton’s facilities in Broussard Louisiana.
- James Leger, Lab scientist at Halliburton’s Brossard Facility, for his help in running the series of tests.
- Richard deBoisBlanc for asking me to be a part of this project on Performance Fluids Management behalf.
- Tommy Gaydos, the drilling superintendent for Newfield whose desire to use oil based muds to drill these wells, set the events in motion, that eventually lead to this study.
- Enderson Cruz, Chief Executive Officer en Poly Alphas de Venezuela C.A, whose similar experiences with an anionic surfactant gave me the confidence I was on the right track.
Additional credits for peer review:
- Stephan Bruce Fry, Senior Global Technical Advisor at Baroid / Halliburton
- Eric Villepreaux, Consultant Fluids & Cement, Waste Management Coordinator
- Hanjo Ledgister, Consultant at Xa2Xe Energy Services
- Thierry Maysounabe, Drilling Fluids & Cement Specialist at Shell