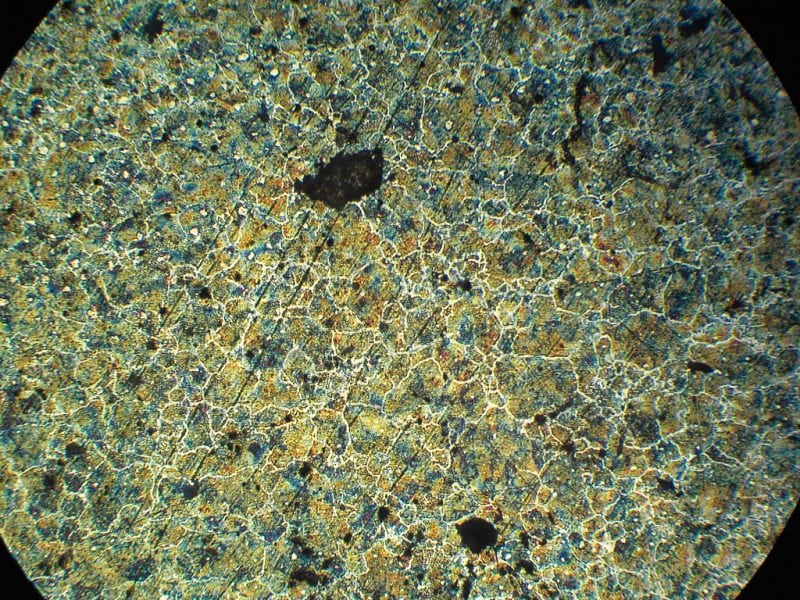
Composite materials are inherently anisotropic and heterogeneous at the micromechanical scale, and its microstructure provides the bridge between manufacturing and performance. Prediction of performance and its variability requires modeling of the microstructure.
Therefore, accurate homogenization techniques become essential to minimize design cycle time for new composite material systems in accordance with operational environments. However, the heterogeneous microstructure may suffer from the matrix cracks and debonds along the fiber-matrix interphase during the manufacturing process, as shown in the figure below.
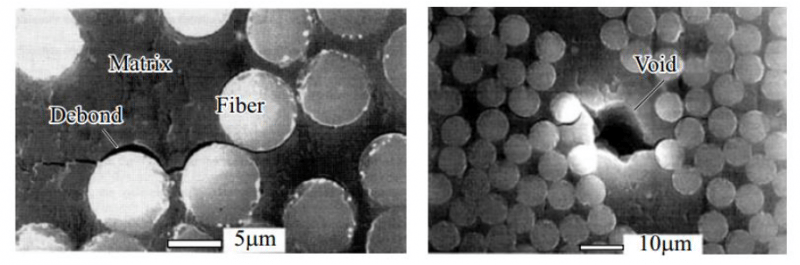
Republished with permission from Elsevier from https://doi.org/10.1016/j.compstruct.2018.01.009
Homogenization transforms a structure with material heterogeneity into a constitutively equivalent structure with a homogeneous material. The Unit Cell (UC) approach can be employed to homogenize the heterogeneous materials for determining effective properties under the assumption of periodicity in the presence of a small ratio of UC size to the characteristic deformation, as shown in the figure below.
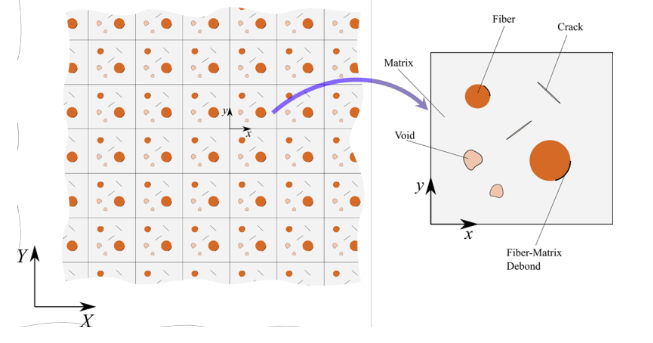
Republished with permission from Elsevier from https://doi.org/10.1016/j.compstruct.2018.01.009
Many existing homogenization techniques lead to accurate predictions for effective material properties while accounting for microstructural topology and constituent material properties. However, they are not suitable to capture the effect of defects on the effective properties, due to the singular nature of stress field due to the presence of cracks and voids in the matrix and cracks in the interphase. Therefore, they fail to provide capture for damage essential to the progressive failure analysis of composites.
A nonlocal continuum approach, Peridynamics (PD), introduced by Silling from Sandia National Labs in 2000, circumvents this limitation by simply removing the PD bonds between material points, as shown in the figure below. It is extremely suitable for modeling structures with material and geometric discontinuities with arbitrary shapes and number of reinforcement materials, voids, and cracks. Also, PD enables the application of periodic boundary conditions in a natural way without any constraint conditions. Furthermore, PD introduces the idea that an internal length parameter, lacking in the existing model, provides the ability for multi-scale material modeling capability.
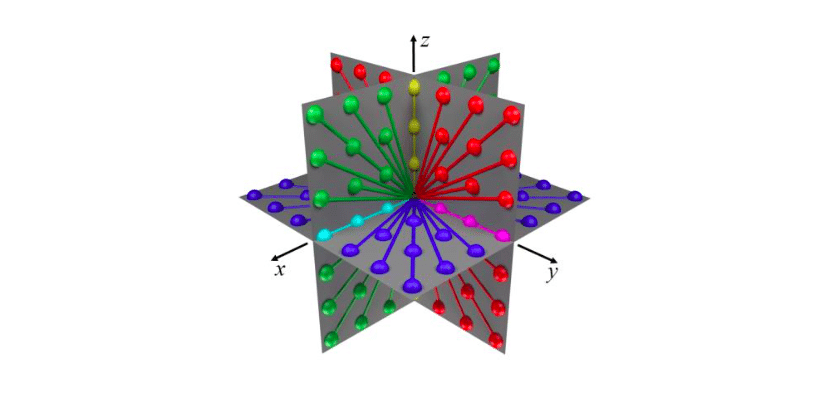
Republished with permission from Elsevier from https://doi.org/10.1016/j.compstruct.2018.01.009
The PD unit cell introduced by Madenci from the University of Arizona in 2017 estimates the effective thermoelastic properties of complex heterogeneous structures in the presence of defects and voids at multiple-length scales coupling the micro- and macro-structural levels. Unlike the existing unit cells, it also provides the damage tensor, which enables the transfer of information between micro- and macro-scale analyses. This capability provides not only an accurate prediction for effective properties but also enables the recovery of the local displacement, stress, and strain fields within the UC, which may be necessary for a further analysis. Thus, it leads to a viable progressive failure prediction capability.
It is part of a multi-scale PD analysis tool for damage initiation/propagation and damage tensor while including the microstructural architecture with or without defects to perform physics-based progressive failure analysis under complex loads in extreme environments. This tool accounts for the nature of failure at the governing scales consistent with the characteristic structural scale.
It integrates macro-, meso-, and micro-scale analyses under a single computational framework. It provides the basic foundation to perform life and remaining life prediction under cyclic loads and includes material property variability and manufacturing defects. The PD UC can be readily implemented into a commercially available finite element program for effective material and physical properties. The research provides design and manufacturing engineers with a better understanding of material interface properties.
These findings are described in the article entitled, Peridynamic unit cell homogenization for thermoelastic properties of heterogeneous microstructures with defects, recently published in the journal Composite Structures. This work was conducted by E. Madenci from The University of Arizona, A. Barut from Global Engineering Research and Technologies, and N. Phan from the US Naval Air Systems Command.