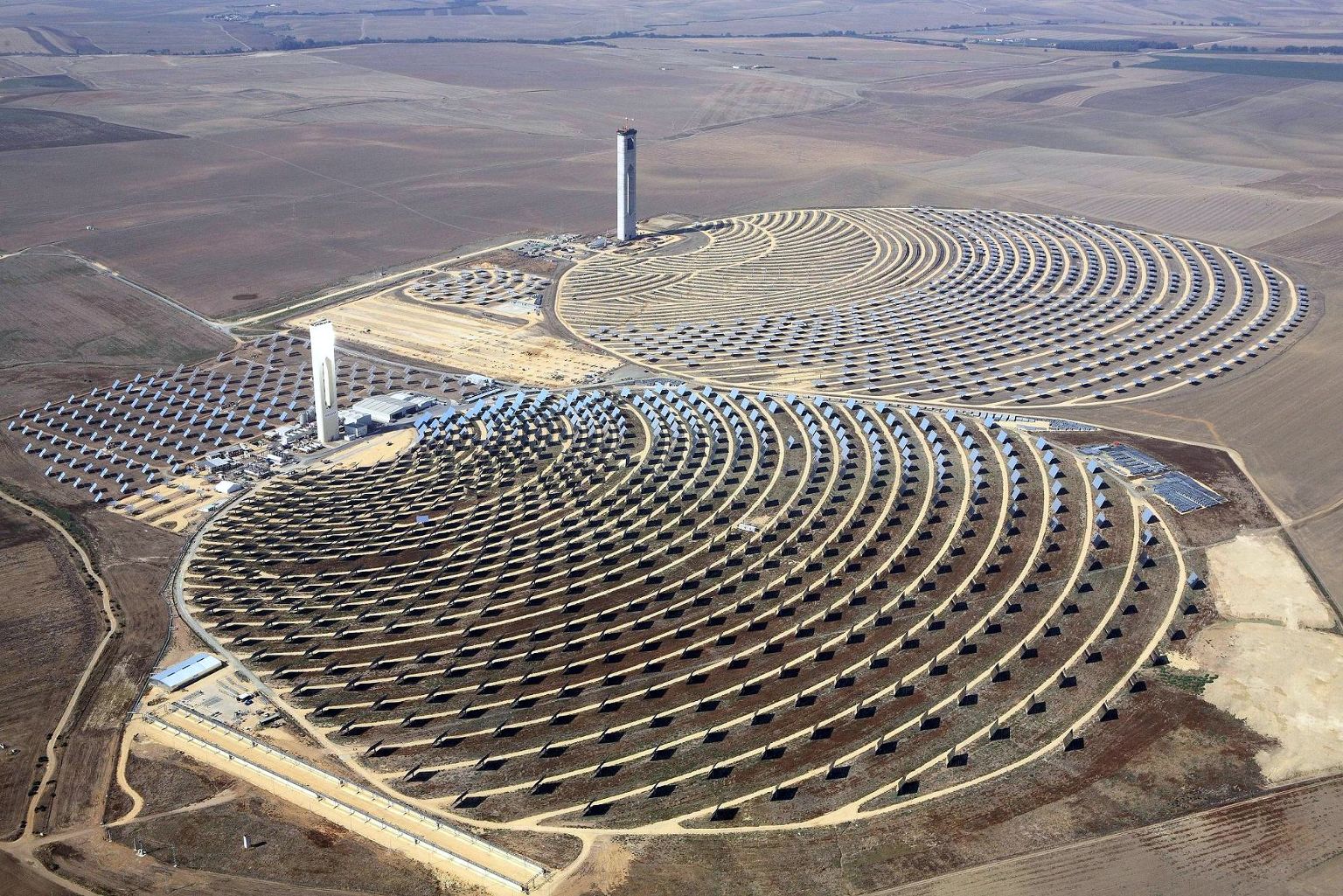
Global warming and climate change are probably the major challenges facing humanity today, which necessitates the reduction of the anthropogenic CO2 emissions into the atmosphere. In the context of increasing energy demand, renewable energies with a low carbon footprint have then to be developed, and among them, solar energy constitutes a viable option. This is the reason why the market of solar technologies has been growing in the last twenty years.
However, their deployment depends on the cost of the produced energy, which is directly linked to the lifetime of materials and components. To make a plant profitable, the service life aims to reach about 20 to 30 years. The energy production of solar plants, either photovoltaic or concentrated solar power (PV or CSP) plants, is also impacted by the solar radiation available on site. There is a paradox because locations on Earth with the better levels of this resource have a highly aggressive environment as well, with a lot of stress factors such as temperature, humidity, UV, etc., which can shorten the plant’s lifetime.
When a new solar technology is developed, such as PV panel or solar mirrors for CSP plants, it is necessary to evaluate its lifetime faster than waiting for many years that the material requires to undergo degradation on-site. A way to predict the effect of a stress factor on a material is to perform an accelerated test, usually increasing the level of stress or increasing cycles number in a laboratory device. The stress factors of interest, and so the ones to test, depending on the location considered for power plant installation. The objective of such tests is to determine either a degradation law or an acceleration factor of the test compared to the site of interest, which can be defined by equation (1):
where A is the acceleration factor, the time to failure on site and the time to failure in the test. As the time to failure on site is equal to the lifetime and so is obviously unknown, a relationship is needed to link a quantification of the stress level to time. In the case of solar mirrors, this approach is relatively new and so there is no existing law in the literature, to the best of our knowledge. This is why we looked in other fields with a greater maturity like electronic devices, polymer materials and PV to formulate a comprehensive review of laws and models of the main stress factors applied to mirrors.
The temperature is the most common stress factor because it enhances the degradation rate of many physical or chemical processes. The model commonly used is the Arrhenius relationship describes by equation (2):
where is the kinetic constant, the frequency factor, the apparent activation energy, the perfect gas constant, and the temperature. The kinetic constant is linked to time through the reaction rate, and so can be determined for simple reaction orders. Then, the acceleration factor of temperature can be calculated combining equations (1) and (2) to get equation (3):
where the temperature during the accelerated test is higher than the mean temperature on site. This relationship makes appear the parameter which depends on the degradation mechanism. That means that its value can vary according to the material of interest, but also to the range of temperature. Such parameter must be determined for each new system before trying to make a lifetime prediction. This can be done using tests at several levels of temperature, chosen in a range including the temperature of the accelerated test performed for the lifetime prediction.
Models should be based on a physicochemical process to avoid mistakes due to degradation mechanism changes, however, this is a rather complex task, so most of the available models are empirical. Empirical models can be perfectly suitable for the device and conditions which have allowed to establish them, nevertheless, they should be applied to other systems carefully. This is why a critical analysis of the different models regarding solar mirrors has been written too. This work has been realized for temperature, irradiance, humidity, water, and chemical stress factors, the problematic of coupling all these models together to get a global expression has shortly been addressed too.
We hope this work can help the community to assess the durability of solar materials and components in a better way to improve their performances.
Published by Coralie Avenel(a), Olivier Raccurt(a), Jean Luc Gardette(b) and Sandrine Therias(b)
(a) Université Grenoble Alpes – CEA LITEN – INES (France), (b) Université Clermont Auvergne – CNRS – SIGMA Clermont, ICCF (France)
These findings are described in the article entitled Review of accelerated ageing test modelling and its application to solar mirrors, recently published in the journal Solar Energy Materials and Solar Cells (Solar Energy Materials and Solar Cells 186 (2018) 29-41). This work was conducted by Coralie Avenel(a,b), Olivier Raccurt(a), Jean Luc Gardette(b) and Sandrine Therias(b) from the Univ. Grenoble Alpes, CEA LITEN, INES, F-38054 Grenoble, France, and the Université Clermont Auvergne – CNRS – SIGMA Clermont, ICCF F-63000 Clermont–Ferrand, France (b).