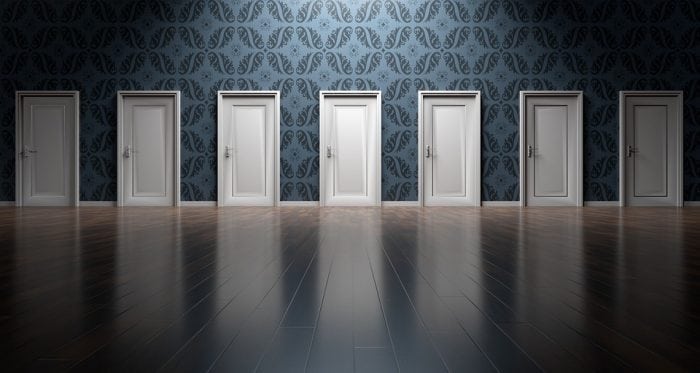
When I received an e-mail from Science Trends in November 2017 asking for a short article for Science Trends, I was happy and excited. Luckily, I hate procrastinating and have amazing time-management skills; no, not really, haha. Thus, I managed to complete the short article only now, many months later.
The three Science Trends example articles that I have seen are in “long abstract,” or, in other words, “paper summary” format. Well, I do not want to follow that path. I want to use more casual language in this short article in the hope that I can reach out to a few more readers, which is a quite significant difference in science, haha.
Considering the delay in writing the article and the casual language of it, I have no idea if Dr. Nace would be kind enough to publish it. Well, if you are reading the article, thanks to you, Dr. Nace. Otherwise, I am completely aware of the fact that the blame is on me. I am still hopeful though, because it says, “Opinions expressed are solely the authors and do not express the views or opinions of Science Trends nor the author’s institution,” at the end of every article. Thus, I can only humiliate myself, haha.
Starting with my Ph.D., my research focus is on managing/controlling/regulating the level of an important variable in a system aiming to improve its dynamics (i.e., its behavior) over time. This variable can be the number of items in an inventory, the number of people working in a department, production capacity, the density of blood-glucose, the amount of love in someone’s heart, the distance between two objects, the velocity of a train — everything really. I perceive systems as a collection of levels, in other words, accumulations. Wherever I look, levels present themselves to me.
Let’s consider an inventory. According to my knowledge, the best way to manage the level of this inventory is to consider the following while placing orders:
- The current level of the inventory
- The ideal level of the inventory
- The rate of shipments from the inventory
- The delays in receiving the placed orders
- The level of the supply line; supply line stands for work-in-process inventory in an inventory-production system, and it stands for in-transit orders in an inventory-distribution system
For many years and as a part of my systems-related courses, I was teaching a dynamic decision-making rule called “anchor-and-adjust,” which considers all of the above criteria and can be used in determining the amount of the orders that an inventory manager places every decision period. This rule has two parameter values; one parameter determines the speed with which one aims to correct the discrepancy between the ideal and current levels of the inventory, and the other parameter determines how much one considers the level of the supply line (i.e., incoming past orders).
In the past, I was so sure about the optimum parameter values of this rule (in discrete-time models), which is also supported by scientific studies in this area. One must make a full correction every period and one must fully consider the supply line, not partially. This claim is true for single-inventory systems. It has been shown that making partial corrections results in a slow response, and ignoring the supply line results in oscillations at the inventory level, which are both costly.
You all know about the costs of oscillations and slow adjustment. Assume you are showering; the first thing you will do is to adjust the temperature of the water. However, there is a delay before you can experience the resulting temperature of the current setting, as the water needs to go through a pipe before it reaches to you. If you make rapid adjustments, you will experience oscillations from cold to hot and hot to cold. If you make mild and infrequent adjustments, it will take a relatively long time to go from either hot or cold to the desired level of warmth. The anchor-and-adjust rule with the optimum parameter values correspond to making a single rapid adjustment and waiting until the water with the perfect setting reaches to you. Yes, the anchor-and-adjust rule with optimum parameter values can create perfect dynamics.
Now we can go back to inventories. There is a managerial board game called The Beer Game, which is played by teams of four members, and every team member manages the level of inventory of their echelon on their team’s supply chain. Interestingly, many “Beer Game” studies claim that the aforementioned optimum managerial decision parameter values are also valid for cascading inventories on a supply chain. Thus, the optimum parameter values minimize the aforementioned costs.
Mr. Mert Edali, who was my graduate student at that time, and I first constructed a mathematical model of The Beer Game and wrote a code for it that can be used in testing different cases. We also generated the results reported by other Beer Game studies and confirmed that the optimum managerial decision-making parameter values are indeed correct. Until now, there is nothing new in this short article; the optimum parameter values that depict the decisions of good inventory managers are confirmed to be valid.
Mr. Edali and I asked a new question: “Will the optimum values remain the same if the other inventory managers on the same supply chain behave non-optimally?” When we asked the question, we were not hoping for much; there might be small changes, but we were expecting the parameter values to remain pretty much as they are. However, our results suggest differently; if you are on a poorly-managed supply chain, you cannot use the optimum parameter values at all, especially if you are the one managing one of the downstream echelons.
In the study, we first selected an echelon and re-optimized the parameter values only for that echelon under the assumption that the other inventory managers use non-optimal parameter values. We repeated this process one by one for all echelons. Interestingly, much better results are obtained when controversial parameter values are used by the echelon of concern, values that correspond to non-optimum behavioral decision making.
In simple words, if you are managing an echelon on a supply chain and the other inventory managers don’t know the best way to manage their own inventories, you cannot use your “perfect” knowledge of managing inventories. I was shocked by the results and validated them many times as they were challenging my own “truth.” As a result of this surprising finding, we started to wonder if the “perfect” parameter values will remain perfect under more realistic settings, even if all managers on the supply chain are “good” inventory managers, which, by the way, is the topic of our current research.
Is it possible that we are opening the path to understand why many people claim that the information gained during university education does not necessarily transfer to real-life settings and, even if it does, it may not be easy to do so?
These findings are described in the articles entitled A Mathematical Model of the Beer Game, recently published in the Journal of Artificial Societies and Social Simulation and Results of a beer game experiment: Should a manager always behave according to the book?, recently published in the journal Complexity. This work was conducted by Mert Edali from Yildiz Technical University and Hakan Yasarcan from Bogazici University.